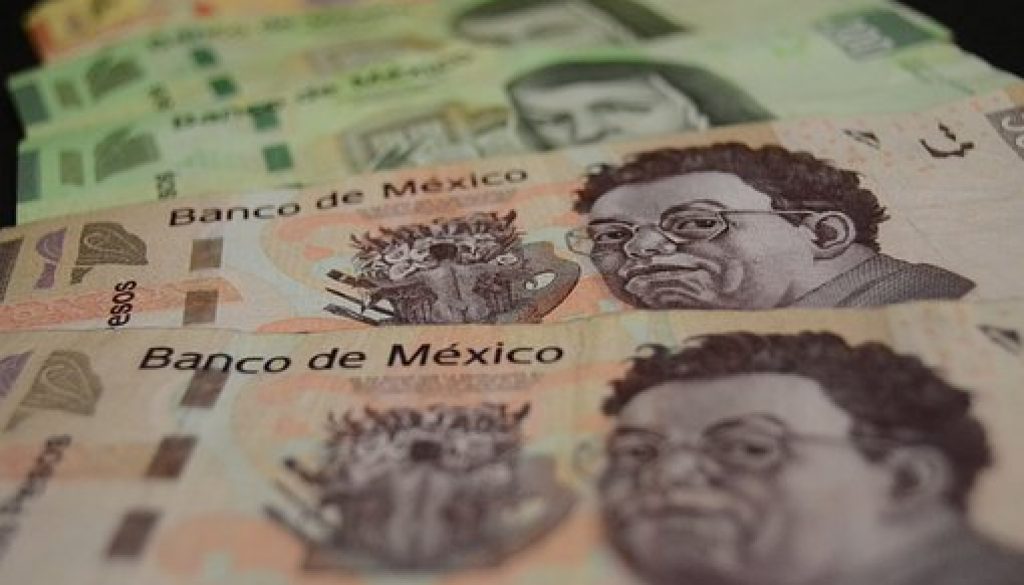
Demand management can be described as a strategy to make sure that a company is meeting its customers' demands. It basically involves bridging between supply and marketing, allowing companies to predict the demand. This process can increase speed and quality of delivery and reduce invoice disputes. It also lowers the cost of running a business.
Companies that have a robust demand management process are more open to market changes. Because they have a system to identify the ideal customers, this can result in effective marketing.
Business can use demand management to help plan for the future and increase customer satisfaction. If done properly, it can reduce invoice disputes and increase asset utilization. An effective demand management strategy can improve operational flexibility as well as operational resilience.
A project management program can improve the demand management approach. These software programs can be used by teams to coordinate their work and avoid silos. Companies can also use change management plans to quickly address supply chain issues.
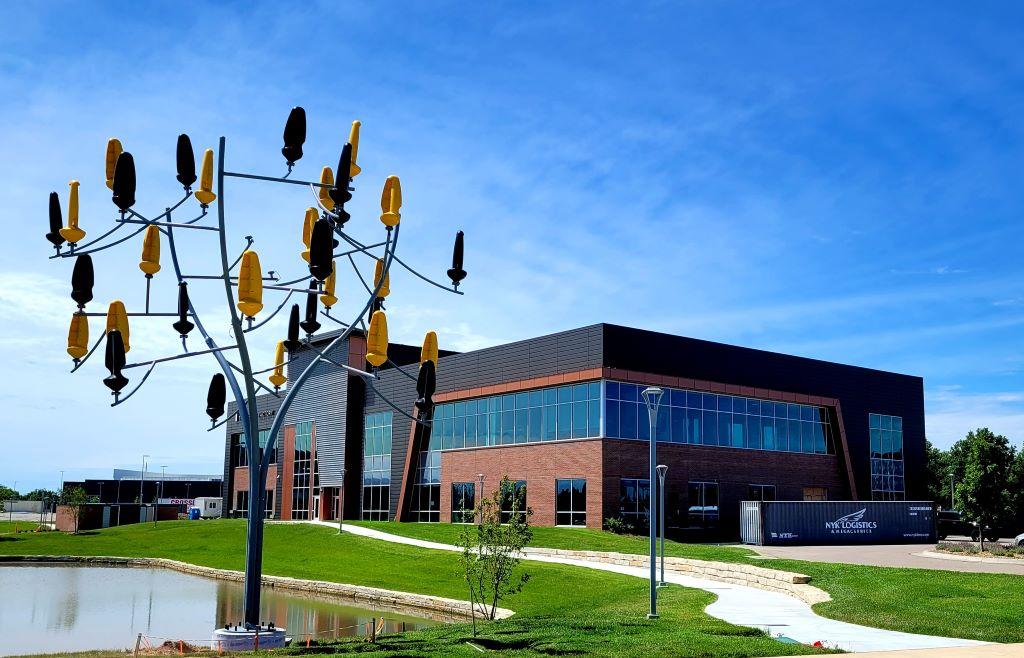
For example, ILOG's PowerOps Suite integrates manufacturing scheduling functions. Dynasys, QAD, and Dynasys also offer applications that help organizations create a demand- and supply plan. These applications can be used to help organizations understand the impact of any changes made on their supply chains. And Optiant offers ERP solutions to enable organizations to develop effective, efficient and consistent order and supply management processes.
Real-Time Inventory, Terra Technology and CDC Software all offer real-time forecasting tools that can reduce supply-chain disruptions. The collaborative management strategy enables companies to exchange information and resources. It also includes performance indicators, knowledge sharing and joint planning.
However, before implementing a demand management strategy, it is important to consider a few factors. These factors will allow professionals to understand the process better, and be able to focus on what is most important.
One of the most critical factors in a demand management process is leadership buy-in. Because demand management is collaborative and involves several levels of leadership, this is crucial. Among the highest-level players are top executives and managers who are responsible for ensuring that all members are on the same page. To ensure the success of the initiative, it is also crucial to include those at the lower levels.
There are many apps that can be used to help companies implement a demand-supply plan. Here are some key points:
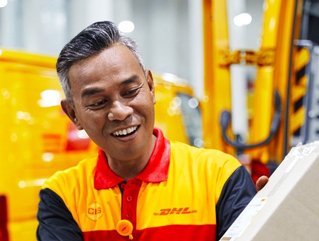
It is crucial to understand the market and identify the ideal customer. Not only should the company know which customers it should target, but they must also be able analyze and measure the effectiveness of their efforts.
Companies must be able to adapt to change in order to grow and become more flexible. An effective plan can decrease supply chain disruptions, tactical forecast error, and supply chain disruptions. Lastly, demand management is a valuable tool to help develop and implement portfolio and strategic plans.
FAQ
What is the responsibility of a logistics manager?
Logistics managers ensure that goods arrive on time and are unharmed. This is done by using his/her experience and knowledge of the company's products. He/she also needs to ensure adequate stock to meet demand.
What is the difference between manufacturing and logistics
Manufacturing is the process of creating goods from raw materials by using machines and processes. Logistics includes all aspects related to supply chain management, such as procurement, distribution planning, inventory control and transportation. Logistics and manufacturing are often referred to as one thing. It encompasses both the creation of products and their delivery to customers.
How can excess manufacturing production be reduced?
Better inventory management is key to reducing excess production. This would reduce time spent on activities such as purchasing, stocking, and maintaining excess stock. This will allow us to free up resources for more productive tasks.
One way to do this is to adopt a Kanban system. A Kanbanboard is a visual tool that allows you to keep track of the work being done. Kanban systems are where work items travel through a series of states until reaching their final destination. Each state has a different priority level.
For instance, when work moves from one stage to another, the current task is complete enough to be moved to the next stage. However, if a task is still at the beginning stages, it will remain so until it reaches the end of the process.
This allows work to move forward and ensures that no work is missed. Managers can see how much work has been done and the status of each task at any time with a Kanban Board. This information allows managers to adjust their workflow based off real-time data.
Lean manufacturing can also be used to reduce inventory levels. Lean manufacturing works to eliminate waste throughout every stage of the production chain. Any product that isn't adding value can be considered waste. Here are some examples of common types.
-
Overproduction
-
Inventory
-
Packaging that is not necessary
-
Excess materials
These ideas can help manufacturers improve efficiency and reduce costs.
How can manufacturing avoid production bottlenecks
To avoid production bottlenecks, ensure that all processes run smoothly from the moment you receive your order to the time the product ships.
This includes planning for capacity requirements as well as quality control measures.
Continuous improvement techniques such Six Sigma can help you achieve this.
Six Sigma is a management method that helps to improve quality and reduce waste.
It emphasizes consistency and eliminating variance in your work.
Statistics
- (2:04) MTO is a production technique wherein products are customized according to customer specifications, and production only starts after an order is received. (oracle.com)
- It's estimated that 10.8% of the U.S. GDP in 2020 was contributed to manufacturing. (investopedia.com)
- [54][55] These are the top 50 countries by the total value of manufacturing output in US dollars for its noted year according to World Bank.[56] (en.wikipedia.org)
- Many factories witnessed a 30% increase in output due to the shift to electric motors. (en.wikipedia.org)
- Job #1 is delivering the ordered product according to specifications: color, size, brand, and quantity. (netsuite.com)
External Links
How To
How to Use 5S to Increase Productivity in Manufacturing
5S stands to stand for "Sort", “Set In Order", “Standardize", and "Store". Toyota Motor Corporation created the 5S methodology in 1954. This methodology helps companies improve their work environment to increase efficiency.
This approach aims to standardize production procedures, making them predictable, repeatable, and easily measurable. Cleaning, sorting and packing are all done daily. These actions allow workers to perform their job more efficiently, knowing what to expect.
Implementing 5S involves five steps: Sort, Set in Order, Standardize Separate, Store, and Each step requires a different action, which increases efficiency. If you sort items, it makes them easier to find later. When you arrange items, you place them together. Once you have separated your inventory into groups and organized them, you will store these groups in easily accessible containers. Make sure everything is correctly labeled when you label your containers.
This process requires employees to think critically about how they do their job. Employees should understand why they do the tasks they do, and then decide if there are better ways to accomplish them. They must learn new skills and techniques in order to implement the 5S system.
The 5S method not only increases efficiency but also boosts morale and teamwork. They are more motivated to achieve higher efficiency levels as they start to see improvement.