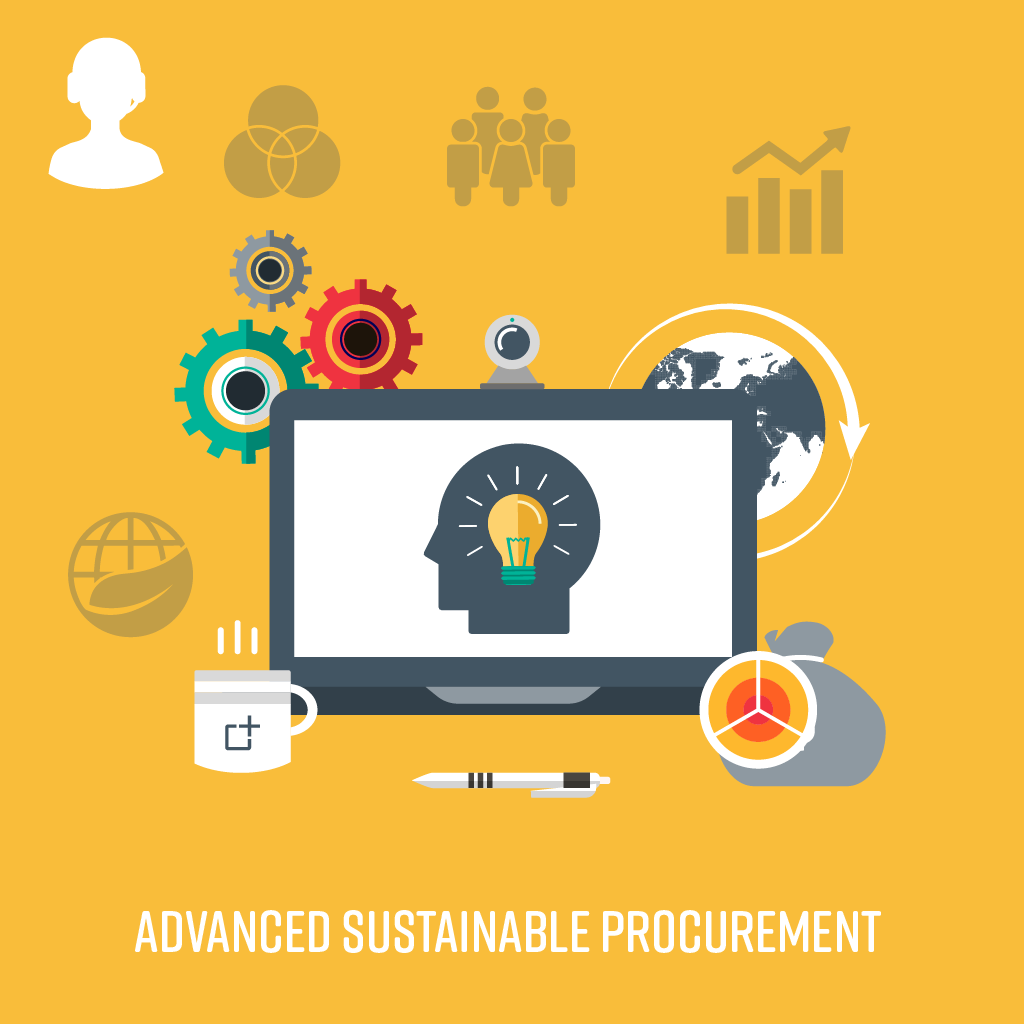
The term "global supply-chain management" describes the process of distribution of goods and services in a transnational company's global network. The main idea behind global supply-chain management is to maximise profit while minimising waste. This distribution method has many advantages, but there are also drawbacks. Let's examine some of these issues. Find out more about global supply management. We will also address some of the problems associated with global supply chain management.
Resilience
As an effective global supply chain manager, it is crucial to build a strategy that promotes resilience. You can increase the resilience of your supply chain by redesigning it, making redundancies and using multiple sourcing. Supply chains may appear rigid at first, but they can evolve with creativity, innovation, and constant vigilance. Cin7 is an inventory management software company that has provided various educational materials as well as advice to its customers.
Information sharing
While the role of information sharing in global supply chain management may seem ambiguous, it is vital to the survival of enterprises. This study examines the benefits of information sharing in supply chains. Information sharing can have many benefits. These benefits may differ depending upon the type of information that is shared. Information is generally valued differently depending on who it is shared with. Here are some examples to illustrate the benefits of information for supply chains.
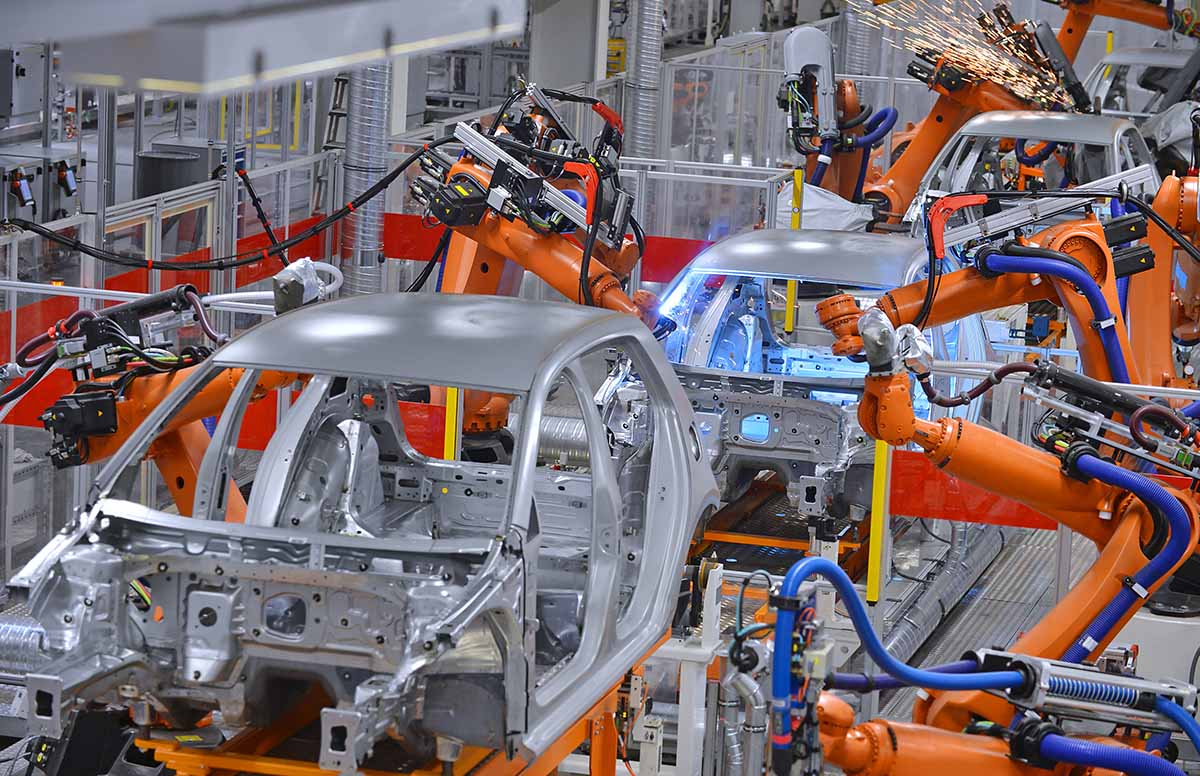
Quality management
Quality issues are an essential part of any supply-chain. Quality management is critical for any supply chain. While companies should be focusing on product quality, it's equally important to address secondary issues to manage supply chain risks. This article will cover the role and importance of quality management for global supply chain management. It will also demonstrate how businesses can fail to meet this challenge. Let's talk about how companies can overcome such challenges and implement better quality assurance practices.
Logistics links
The business's needs change with the changing demands and preferences of consumers. The global supply chain is a complex web of suppliers, individuals, and companies that works together to deliver goods on time and to the right place. Logistics plays an important role in global supply chain management. It helps companies reduce their costs and improves their performance. In addition to businesses, supply chains include vendors, producers, warehouses, transportation companies, distribution centers, retailers, and more.
Pandemic COVID-19
Global supply chain management is urgently needed due to the large-scale spread of COVID-19. Global supply chain management is essential for emergency response efforts. It ensures that critical supplies are delivered promptly. But the global supply chain has been strained by other issues, such as the ongoing Chinese lockdown and global economic uncertainty. This pandemic proves to be a test of supply-chain resilience and flexibility. In the wake of this crisis, companies will be judged not only on their response, but also on their corporate values.
Economic Impact
Global supply chain management is vital for the global economy. As manufacturers move to JIT (just as-needed) production, they will become more dependent upon one source for vital supplies. JIT production models do have one major problem: they leave companies open for disruptions in their supply networks. A recent survey revealed that almost half of executives intend to eliminate some Chinese production and one-third plan de-emphasize JIT manufacturing.
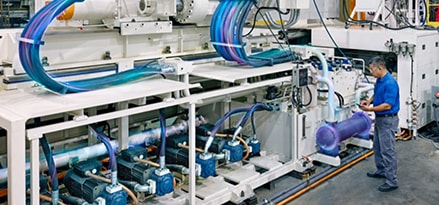
There are many career opportunities
Global supply chain managers oversee all aspects of a business's international procurement strategy. They manage inventory logistics and work with suppliers to ensure top-quality products. They also monitor and analyze data related the supply chain. This role requires collaboration with many departments within a company. These are just a few career options that people with this type of background can choose from. All of them provide valuable career benefits.
FAQ
What is the job of a manufacturer manager?
A manufacturing manager has to ensure that all manufacturing processes work efficiently and effectively. They must also be alert to any potential problems and take appropriate action.
They must also be able to communicate with sales and marketing departments.
They should also be knowledgeable about the latest trends in the industry so they can use this information for productivity and efficiency improvements.
What is the importance of automation in manufacturing?
Automation is essential for both manufacturers and service providers. It enables them to provide services faster and more efficiently. It reduces human errors and improves productivity, which in turn helps them lower their costs.
Is it possible to automate certain parts of manufacturing
Yes! Automation has been around since ancient times. The Egyptians invent the wheel thousands of year ago. We now use robots to help us with assembly lines.
There are many uses of robotics today in manufacturing. These include:
-
Assembly line robots
-
Robot welding
-
Robot painting
-
Robotics inspection
-
Robots that make products
There are many other examples of how manufacturing could benefit from automation. 3D printing makes it possible to produce custom products in a matter of days or weeks.
How can I learn about manufacturing?
The best way to learn about manufacturing is through hands-on experience. However, if that's not possible, you can always read books or watch educational videos.
What is the job of a logistics manger?
Logistics managers are responsible for ensuring that all goods arrive in perfect condition and on time. This is done through his/her expertise and knowledge about the company's product range. He/she should ensure that sufficient stock is available in order to meet customer demand.
What does warehouse mean?
A warehouse, or storage facility, is where goods are stored prior to being sold. It can be either an indoor or outdoor space. Sometimes, it can be both an indoor and outdoor space.
Statistics
- In the United States, for example, manufacturing makes up 15% of the economic output. (twi-global.com)
- You can multiply the result by 100 to get the total percent of monthly overhead. (investopedia.com)
- (2:04) MTO is a production technique wherein products are customized according to customer specifications, and production only starts after an order is received. (oracle.com)
- In 2021, an estimated 12.1 million Americans work in the manufacturing sector.6 (investopedia.com)
- Many factories witnessed a 30% increase in output due to the shift to electric motors. (en.wikipedia.org)
External Links
How To
How to Use Lean Manufacturing in the Production of Goods
Lean manufacturing (or lean manufacturing) is a style of management that aims to increase efficiency, reduce waste and improve performance through continuous improvement. It was developed by Taiichi Okono in Japan, during the 1970s & 1980s. TPS founder Kanji Takoda awarded him the Toyota Production System Award (TPS). Michael L. Watkins published the book "The Machine That Changed the World", which was the first to be published about lean manufacturing.
Lean manufacturing can be described as a set or principles that are used to improve quality, speed and cost of products or services. It emphasizes the elimination of defects and waste throughout the value stream. Lean manufacturing can be described as just-in–time (JIT), total productive maintenance, zero defect (TPM), or even 5S. Lean manufacturing emphasizes reducing non-value-added activities like inspection, rework and waiting.
Lean manufacturing can help companies improve their product quality and reduce costs. Additionally, it helps them achieve their goals more quickly and reduces employee turnover. Lean Manufacturing is one of the most efficient ways to manage the entire value chains, including suppliers and customers as well distributors and retailers. Lean manufacturing is widely practiced in many industries around the world. Toyota's philosophy is the foundation of its success in automotives, electronics and appliances, healthcare, chemical engineers, aerospace, paper and food, among other industries.
Lean manufacturing includes five basic principles:
-
Define Value: Identify the social value of your business and what sets you apart.
-
Reduce Waste - Remove any activity which doesn't add value to your supply chain.
-
Create Flow – Ensure that work flows smoothly throughout the process.
-
Standardize and simplify – Make processes as repeatable and consistent as possible.
-
Build Relationships- Develop personal relationships with both internal as well as external stakeholders.
Lean manufacturing is not a new concept, but it has been gaining popularity over the last few years due to a renewed interest in the economy following the global financial crisis of 2008. Many businesses are now using lean manufacturing to improve their competitiveness. Many economists believe lean manufacturing will play a major role in economic recovery.
Lean manufacturing is becoming a popular practice in automotive. It has many advantages. These include improved customer satisfaction, reduced inventory levels, lower operating costs, increased productivity, and better overall safety.
The principles of lean manufacturing can be applied in almost any area of an organization. This is because it ensures efficiency and effectiveness in all stages of the value chain.
There are three types of lean manufacturing.
-
Just-in-Time Manufacturing: Also known as "pull systems", this type of lean manufacturing uses just-in-time manufacturing (JIT). JIT means that components are assembled at the time of use and not manufactured in advance. This method reduces lead times, increases availability, and decreases inventory.
-
Zero Defects Manufacturing (ZDM): ZDM focuses on ensuring that no defective units leave the manufacturing facility. You should repair any part that needs to be repaired during an assembly line. This is true even for finished products that only require minor repairs prior to shipping.
-
Continuous Improvement (CI: Continuous improvement aims to increase the efficiency of operations by constantly identifying and making improvements to reduce or eliminate waste. Continuous Improvement (CI) involves continuous improvement in processes, people, tools, and infrastructure.