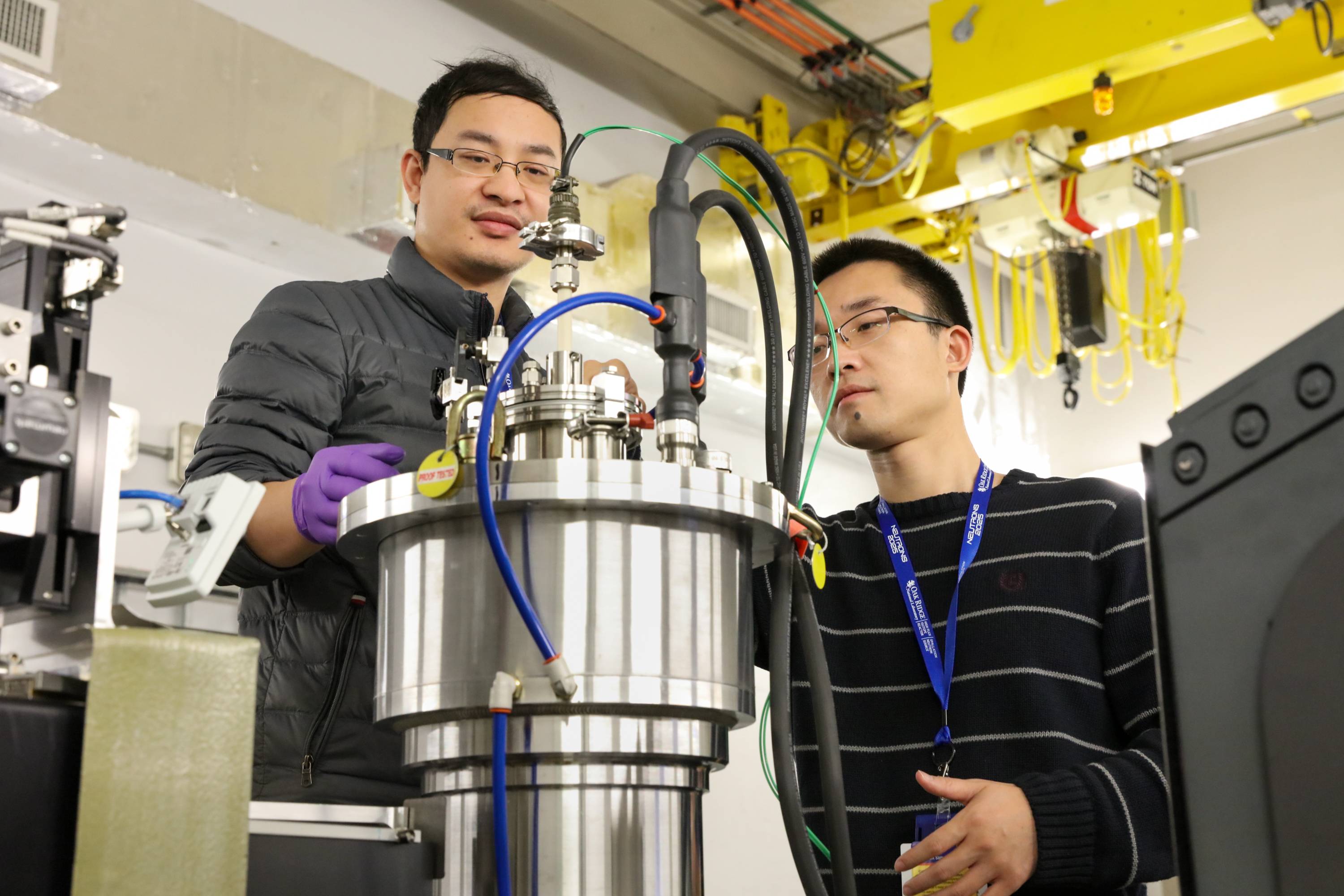
The Great Recession saw 166,000 jobs being lost by Ohio manufacturing companies. The recovery of Ohio's manufacturing industry has been slow. Ohio's manufacturing sector is still at a lower level than it was before the recession.
Ohio's drop in manufacturing jobs is due largely to the rise of European and Japanese manufacturing competition. Manufacturers are being forced to be more technologically-advanced and lower labor costs. Global economic conditions have been difficult, leading to job losses.
Ohio's workforce shortfall is one of the greatest challenges that manufacturers have to face. There are several state initiatives to address the skilled labor shortfall. These initiatives are not comprehensive and can't solve all the workforce challenges faced by manufacturers. A special report by the Ohio Governor's Office of Workforce Transformation on the workforce shortage recommended that educators and businesses work more closely together. However, the report discovered a gap between business and school needs.
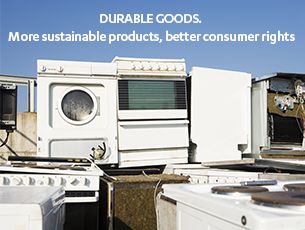
Ohio's workforce is multifaceted, complex and diverse. Unions are less likely for manufacturing workers than in other industries. However, unionized manufacturing jobs still offer livable wages and solid benefits.
Ohio's manufacturing sector is a major contributor to its economy. Interstate highways, railways and inland waterways allow manufacturers to efficiently distribute goods. Additionally, the state is a top exporter. Private investors will also be attracted by the state's natural-gas production.
The state has managed to recover 50,000 manufacturing jobs during the last four years. However, Kasich's first term saw slow job gains. In the first three years of his administration, manufacturing job gains averaged 7 percent. In the past two years, manufacturing jobs have declined by a combined 1,771 jobs. These losses are caused by the slowing economy, the automobile industry, and lukewarm global demands.
Ohio is a top exporter of goods, with top export markets including the U.S., Canada, Mexico, and the U.K. Exports have declined by $1.4 billion over the past year. Ohio manufacturers still face major challenges in trade policy. While changes in trade policy can help workers in specific industries, the full range of challenges will be addressed only by policymakers.
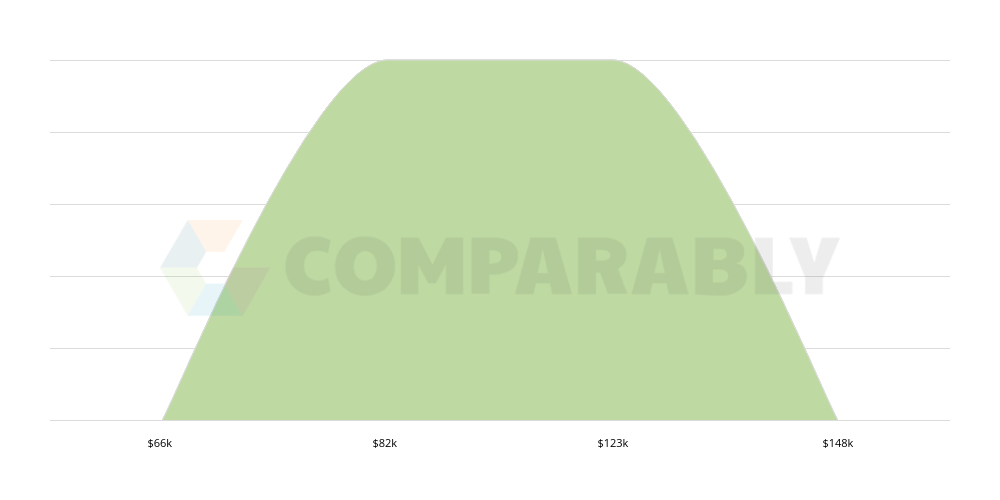
Ohio's main industry, manufacturing, is still very important. Manufacturing jobs can be a high-paying job for semi-skilled workers, even if they don't have post-secondary training. But Ohio's wages have not kept pace the growth in Ohio. Although manufacturing jobs pay higher than other occupations in Ohio, they are not enough for middle-class lifestyles.
Ohio's manufacturing workforce includes a variety of workers. In order to keep up with the rest, the state's manufacturing sectors have been diversifying. Ohio's economy is now more service-oriented. Manufacturing is no longer Ohio's primary employer. Manufacturers are focusing more on international exposure and developing skills for future generations.
FAQ
What are the 7 Rs of logistics?
The 7R's of Logistics is an acronym for the seven basic principles of logistics management. It was developed by the International Association of Business Logisticians (IABL) and published in 2004 as part of its "Seven Principles of Logistics Management" series.
The acronym consists of the following letters:
-
Responsible – ensure that all actions are legal and don't cause harm to anyone else.
-
Reliable - Have confidence in your ability to fulfill all of your commitments.
-
Reasonable - make sure you use your resources well and don't waste them.
-
Realistic - consider all aspects of operations, including cost-effectiveness and environmental impact.
-
Respectful: Treat others with fairness and equity
-
Resourceful - look for opportunities to save money and increase productivity.
-
Recognizable is a company that provides customers with value-added solutions.
What is the difference between Production Planning, Scheduling and Production Planning?
Production Planning (PP), is the process of deciding what production needs to take place at any given time. This is done through forecasting demand and identifying production capacities.
Scheduling is the process of assigning specific dates to tasks so they can be completed within the specified timeframe.
Why is logistics important in manufacturing?
Logistics are an essential part of any business. Logistics can help you achieve amazing results by helping to manage product flow from raw materials to finished products.
Logistics play an important role in reducing costs as well as increasing efficiency.
What are my options for learning more about manufacturing
Hands-on experience is the best way to learn more about manufacturing. You can also read educational videos or take classes if this isn't possible.
What does it mean to be a manufacturer?
Manufacturing Industries are companies that manufacture products. Consumers are people who purchase these goods. These companies employ many processes to achieve this purpose, such as production and distribution, retailing, management and so on. They manufacture goods from raw materials using machines and other equipment. This includes all types if manufactured goods.
What does it take for a logistics enterprise to succeed?
To be a successful businessman in logistics, you will need many skills and knowledge. You must have good communication skills to interact effectively with your clients and suppliers. You will need to know how to interpret data and draw conclusions. You must be able and able to handle stress situations and work under pressure. To increase efficiency and creativity, you need to be creative. You must be a strong leader to motivate others and direct them to achieve organizational goals.
It is also important to be efficient and well organized in order meet deadlines.
What are the responsibilities of a manufacturing manager
A manufacturing manager must ensure that all manufacturing processes are efficient and effective. They should also be aware and responsive to any company problems.
They should also learn how to communicate effectively with other departments, including sales and marketing.
They should also be aware of the latest trends in their industry and be able to use this information to help improve productivity and efficiency.
Statistics
- According to the United Nations Industrial Development Organization (UNIDO), China is the top manufacturer worldwide by 2019 output, producing 28.7% of the total global manufacturing output, followed by the United States, Japan, Germany, and India.[52][53] (en.wikipedia.org)
- It's estimated that 10.8% of the U.S. GDP in 2020 was contributed to manufacturing. (investopedia.com)
- In 2021, an estimated 12.1 million Americans work in the manufacturing sector.6 (investopedia.com)
- In the United States, for example, manufacturing makes up 15% of the economic output. (twi-global.com)
- Many factories witnessed a 30% increase in output due to the shift to electric motors. (en.wikipedia.org)
External Links
How To
How to use the Just-In Time Method in Production
Just-in-time (JIT) is a method that is used to reduce costs and maximize efficiency in business processes. This is where you have the right resources at the right time. This means that you only pay the amount you actually use. Frederick Taylor was the first to coin this term. He developed it while working as a foreman during the early 1900s. He noticed that workers were often paid overtime when they had to work late. He concluded that if workers were given enough time before they start work, productivity would increase.
JIT is an acronym that means you need to plan ahead so you don’t waste your money. It is important to look at your entire project from beginning to end and ensure that you have enough resources to handle any issues that may arise. You can anticipate problems and have enough equipment and people available to fix them. You won't have to pay more for unnecessary items.
There are many JIT methods.
-
Demand-driven JIT: You order the parts and materials you need for your project every other day. This will allow to track how much material has been used up. This will allow you to calculate how long it will take to make more.
-
Inventory-based: This is a type where you stock the materials required for your projects in advance. This allows you to predict how much you can expect to sell.
-
Project-driven : This is a method where you make sure that enough money is set aside to pay the project's cost. You will be able to purchase the right amount of materials if you know what you need.
-
Resource-based JIT: This type of JIT is most commonly used. Here, you allocate certain resources based on demand. For instance, if you have a lot of orders coming in, you'll assign more people to handle them. If you don't have many orders, you'll assign fewer people to handle the workload.
-
Cost-based: This is a similar approach to resource-based but you are not only concerned with how many people you have, but also how much each one costs.
-
Price-based: This is a variant of cost-based. However, instead of focusing on the individual workers' costs, this looks at the total price of the company.
-
Material-based: This is very similar to cost-based but instead of looking at total costs of the company you are concerned with how many raw materials you use on an average.
-
Time-based JIT is another form of resource-based JIT. Instead of focusing on how much each employee costs, you focus on how long it takes to complete the project.
-
Quality-based JIT is another variant of resource-based JIT. Instead of focusing on the cost of each worker or how long it takes, think about how high quality your product is.
-
Value-based JIT: One of the most recent forms of JIT. This is where you don't care about how the products perform or whether they meet customers' expectations. Instead, you focus on the added value that you provide to your market.
-
Stock-based: This stock-based method focuses on the actual quantity of products being made at any given time. It's used when you want to maximize production while minimizing inventory.
-
Just-intime (JIT), planning is a combination JIT management and supply chain management. This refers to the scheduling of the delivery of components as soon after they are ordered. It reduces lead times and improves throughput.