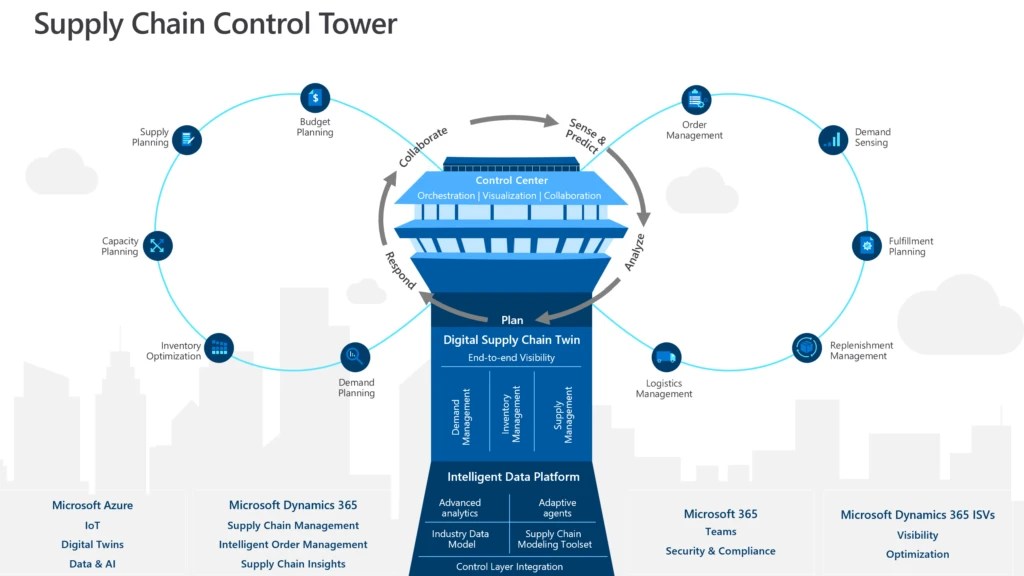
If you're interested in a supply chain management career, you can start by researching industries that offer good opportunities. It is important to research the industry to see how many people are employed in it, what skills they have, and what jobs are available. If you're looking for a job, recruiters or human resource specialists can help. You can join a professional organization to learn more about certifications, depending on your goals.
Supply chain management requires many skills. It is a fast-paced industry that demands a lot of flexibility. While it may seem like a challenging and complex career, it's also extremely rewarding. There's a huge amount of flexibility and opportunity, and you'll have the chance to use all your skills in a variety of industries.
Logistics and supply chain managers must have skills in project management, critical thinking, interpersonal communication, sustainability, and organizational leadership. They must also be able communicate effectively with all levels of stakeholders. They must also know how to implement new technologies and understand international regulations.
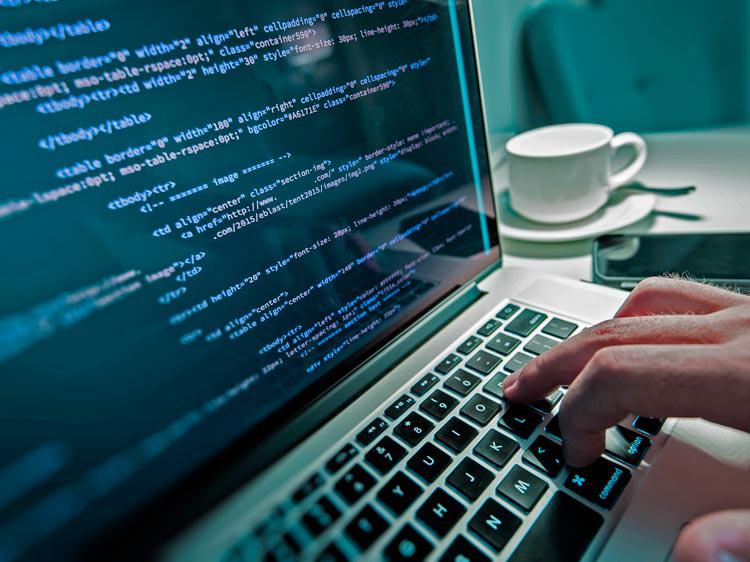
Companies today look at their supply chains from a larger perspective. You'll see that not all supply chains are the same. While a large company may have many product lines you can work on, a small family-owned business might offer less career progression opportunities. Your satisfaction can also be affected greatly by the company's size.
To get started you will need a strong support network. Make friends with supply chain management professionals in HR, and learn more about the industries that you are interested. Once you have built up a solid network, then you can search for a supply-chain job. You will need to demonstrate that you are competent and have experience in supply chain jobs.
Supply chain management is a fast-paced, unpredictable field. It's important to be flexible and have the ability to solve problems quickly. Problems can be solved quickly to avoid disruptions in your supply chains and ensure your organization's goals.
As part a supply chain career, your role will include data gathering and organizing. This ability is crucial for making good decisions and allocating team resources. It is essential to collect and manage data in order to support all the processes involved with serving consumers.

Managers of supply chains should be able manage projects and monitor finances. Although they may be responsible for managing several projects simultaneously, they should also be able decide which ones to prioritize. They'll have to weigh the pros and con of each choice.
For those who want to pursue a supply chain management career, you can find positions in retail, healthcare, transportation, manufacturing, and food service. These positions can vary in salary and employment. You will need to have at least a few years' experience in order to be hired in each industry.
Supply chain management is a growing field, and there are plenty of jobs for you to consider. You can use what you love about working with people to make a career out of this fast-paced field.
FAQ
What is the importance of logistics in manufacturing?
Logistics is an integral part of every business. They can help you achieve great success by helping you manage product flow from raw material to finished goods.
Logistics are also important in reducing costs and improving efficiency.
What is the responsibility of a manufacturing manager?
A manufacturing manager has to ensure that all manufacturing processes work efficiently and effectively. They should also be aware and responsive to any company problems.
They should also be able and comfortable communicating with other departments like sales and marketing.
They should be informed about industry trends and be able make use of this information to improve their productivity and efficiency.
What are the 7 Rs of logistics?
The acronym 7R's for Logistics stands to represent the seven basic principles in logistics management. It was published in 2004 by the International Association of Business Logisticians as part of their "Seven Principles of Logistics Management" series.
The following letters make up the acronym:
-
Responsible - to ensure that all actions are within the legal requirements and are not detrimental to others.
-
Reliable - You can have confidence that you will fulfill your promises.
-
Reasonable - use resources efficiently and don't waste them.
-
Realistic - Take into consideration all aspects of operations including cost-effectiveness, environmental impact, and other factors.
-
Respectful - Treat people fairly and equitably
-
Reliable - Find ways to save money and increase your productivity.
-
Recognizable - Provide value-added services to customers
What does manufacturing industry mean?
Manufacturing Industries are businesses that produce products for sale. Consumers are people who purchase these goods. These companies use various processes such as production, distribution, retailing, management, etc., to fulfill this purpose. They create goods from raw materials, using machines and various other equipment. This includes all types and varieties of manufactured goods, such as food items, clothings, building supplies, furnitures, toys, electronics tools, machinery vehicles, pharmaceuticals medical devices, chemicals, among others.
What's the difference between Production Planning & Scheduling?
Production Planning (PP) refers to the process of determining how much production is needed at any given moment. This can be done by forecasting demand and identifying production capabilities.
Scheduling involves the assignment of dates and times to tasks in order to complete them within the timeframe.
What is the job of a production plan?
Production planners ensure that all project aspects are completed on time, within budget and within the scope. They make sure that the product and services meet client expectations.
Statistics
- It's estimated that 10.8% of the U.S. GDP in 2020 was contributed to manufacturing. (investopedia.com)
- (2:04) MTO is a production technique wherein products are customized according to customer specifications, and production only starts after an order is received. (oracle.com)
- In 2021, an estimated 12.1 million Americans work in the manufacturing sector.6 (investopedia.com)
- Many factories witnessed a 30% increase in output due to the shift to electric motors. (en.wikipedia.org)
- You can multiply the result by 100 to get the total percent of monthly overhead. (investopedia.com)
External Links
How To
How to use 5S in Manufacturing to Increase Productivity
5S stands for "Sort", "Set In Order", "Standardize", "Separate" and "Store". The 5S methodology was developed at Toyota Motor Corporation in 1954. This methodology helps companies improve their work environment to increase efficiency.
This method has the basic goal of standardizing production processes to make them repeatable. It means tasks like cleaning, sorting or packing, labeling, and storing are done every day. This knowledge allows workers to be more efficient in their work because they are aware of what to expect.
There are five steps to implementing 5S, including Sort, Set In Order, Standardize, Separate and Store. Each step has a different action and leads to higher efficiency. Sorting things makes it easier to find them later. When you arrange items, you place them together. You then organize your inventory in groups. Labeling your containers will ensure that everything is correctly labeled.
Employees need to reflect on how they do their jobs. Employees must understand why they do certain tasks and decide if there's another way to accomplish them without relying on the old ways of doing things. They will need to develop new skills and techniques in order for the 5S system to be implemented.
The 5S method increases efficiency and morale among employees. As they begin to see improvements, they feel motivated to continue working towards the goal of achieving higher levels of efficiency.