
A BLS Mechanical Engineer is a highly sought-after professional with a specialized education and experience in the field of engineering. A BLS Mechanical Engineer is highly skilled and has a strong educational background. They are also highly qualified to serve as managers and team leaders. This career path has a positive outlook with a 7 percent increase in positions available by 2030. That equates to another 20,900 jobs on the job market. To qualify for this profession, candidates must have experience using computer-aided design and simulation software, as well as extensive knowledge of specialized software and simulation.
Job duties
A mechanical engineer works to plan, design, or develop power-producing equipment. These professionals can also oversee the maintenance, installation, maintenance, and repair machines. They can work as independent consultants or in large engineering services firms. They can also design refrigeration systems for frozen food and air-conditioning systems in buildings. Below are details about the salaries and employment of mechanical engineers.
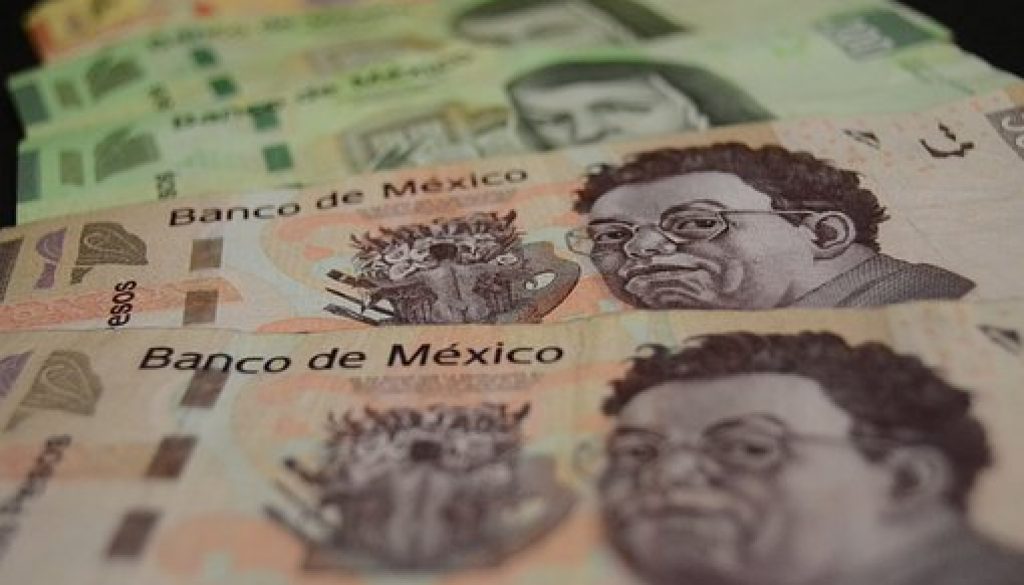
Most entry-level mechanical engineers work in an office setting, but may be required to travel to the construction site to resolve a problem with equipment. The entry-level position requires an understanding of basic business principles. Furthermore, mechanical engineers will frequently use computers so it is important that they have a good understanding of IT and computer science. A strong technical skill set is important for analyzing designs and integrating sensors within machinery.
Education is required
A Bachelor of Science degree in Mechanical Engineering (BSME), can help you get into the field of mechanical engineering. The degree takes four years and teaches the principles of design and testing as well as manufacturing. Computer software is also taught to students to create drawings and other designs. Whether you are interested in the design of airplanes, cars, or other machinery, a BSME will help you find a career in this exciting field.
The BLS is optimistic about this field. BLS expects that there will be a 4 per cent increase in jobs for mechanical engineering workers between 2019-2029. However, some engineers will have the opportunity to take on more management roles or even work as a faculty member in higher education institutions or research and development programs. The average salary for this profession is $84,190. Additionally, the U.S. is expected to see a rise in employment for mechanical engineers over the next decade.
Salary
According to U.S. Bureau of Labor Statistics', the number of mechanic engineers will grow by 5% between 2012-2022. This is a slower growth than the average of all occupations, but still very impressive. Those who stay on top of the latest technological advances will stand to benefit in a competitive job market. There are many factors that can affect the salary of a mechanic engineer.
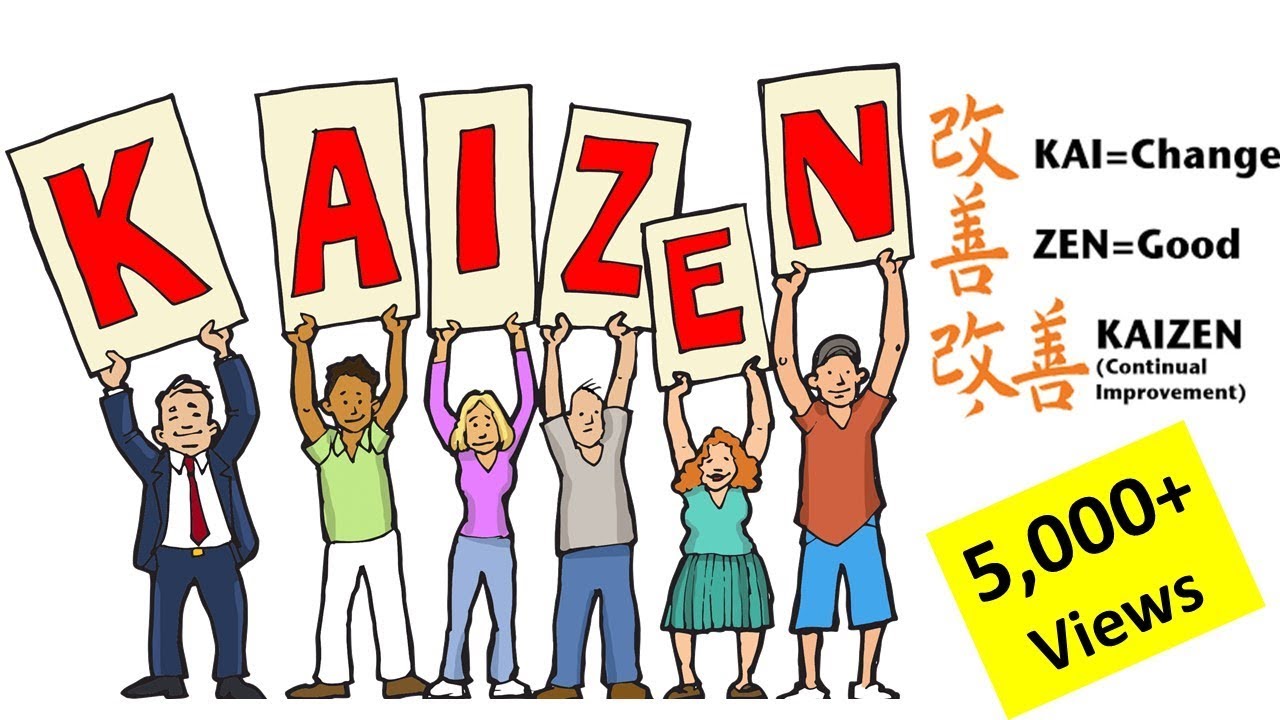
Although there are many factors that affect the amount of a salary, mechanical engineers usually make more than other types of engineers. In fact, the top 10 percent earned more than $126,430 per year. Mechanical engineers can also expect to make a career in electronic product and computer manufacturing, along with higher salaries. California, New Mexico, and Alaska have the highest salaries currently for mechanical engineers. These states are ranked on the basis of their average wage, which can vary widely depending upon education and experience.
FAQ
What is production management?
Production Planning includes planning for all aspects related to production. This document aims to ensure that everything is planned and ready when you are ready to shoot. It should also contain information on achieving the best results on set. This includes location information, crew details, equipment specifications, and casting lists.
First, you need to plan what you want to film. You may have already decided where you would like to shoot, or maybe there are specific locations or sets that you want to use. Once you have identified your locations and scenes it's time to begin figuring out what elements you will need for each one. Perhaps you have decided that you need to buy a car but aren't sure which model. If this is the case, you might start searching online for car models and then narrow your options by selecting from different makes.
After you have selected the car you want, you can begin to think about additional features. Do you have people who need to be seated in the front seat? You might also need someone to help you get around the back. Maybe you want to change the interior color from black to white? These questions will help to determine the style and feel of your car. It is also worth considering the types of shots that you wish to take. You will be filming close-ups and wide angles. Maybe the engine or steering wheel is what you are looking to film. These factors will help you determine which car style you want to film.
Once you have determined all of the above, you can move on to creating a schedule. The schedule will show you when to begin shooting and when to stop. You will need to know when you have to be there, what time you have to leave and when your return home. This way, everyone knows what they need to do and when. Book extra staff ahead of time if you need them. You don't want to hire someone who won't show up because he didn't know.
When creating your schedule, you will also need to consider the number of days you need to film. Some projects only take one or two days, while others may last weeks. When creating your schedule, be aware of whether you need more shots per day. Multiple takes of the same location will lead to higher costs and take more time. It is better to be cautious and take fewer shots than you risk losing money if you are not sure if multiple takes are necessary.
Budget setting is another important aspect in production planning. As it will allow you and your team to work within your financial means, setting a realistic budget is crucial. Keep in mind that you can always reduce your budget if you face unexpected difficulties. But, don't underestimate how much money you'll spend. You will end up spending less money if you underestimate the cost of something.
Production planning is a detailed process. But, once you understand the workings of everything, it becomes easier for future projects to be planned.
What skills do production planners need?
To become a successful production planner, you need to be organized, flexible, and able to multitask. Communication skills are essential to ensure that you can communicate effectively with clients, colleagues, and customers.
What types of jobs can you find in logistics
There are many jobs available in logistics. Here are some examples:
-
Warehouse workers - They load and unload trucks and pallets.
-
Transportation drivers: They drive trucks and trailers and deliver goods and make pick-ups.
-
Freight handlers are people who sort and pack freight into warehouses.
-
Inventory managers - These are responsible for overseeing the stock of goods in warehouses.
-
Sales representatives - They sell products.
-
Logistics coordinators – They plan and coordinate logistics operations.
-
Purchasing agents - They buy goods and services that are necessary for company operations.
-
Customer service representatives - Answer calls and email from customers.
-
Shipping clerks – They process shipping orders, and issue bills.
-
Order fillers – They fill orders based upon what was ordered and shipped.
-
Quality control inspectors: They inspect outgoing and incoming products for any defects.
-
Other - Logistics has many other job opportunities, including transportation supervisors, logistics specialists, and cargo specialists.
How can manufacturing excess production be decreased?
Better inventory management is key to reducing excess production. This would reduce the time spent on unproductive activities like purchasing, storing and maintaining excess stock. We could use these resources to do other productive tasks.
You can do this by adopting a Kanban method. A Kanbanboard is a visual tool that allows you to keep track of the work being done. Work items are moved through various states to reach their destination in a Kanban system. Each state represents a different priority level.
To illustrate, work can move from one stage or another when it is complete enough for it to be moved to a new stage. But if a task remains in the beginning stages it will stay that way until it reaches its end.
This allows for work to continue moving forward, while also ensuring that there is no work left behind. Managers can see how much work has been done and the status of each task at any time with a Kanban Board. This allows them to adjust their workflows based on real-time information.
Another way to control inventory levels is to implement lean manufacturing. Lean manufacturing works to eliminate waste throughout every stage of the production chain. Any product that isn't adding value can be considered waste. Here are some examples of common types.
-
Overproduction
-
Inventory
-
Unnecessary packaging
-
Excess materials
Manufacturers can increase efficiency and decrease costs by implementing these ideas.
What are my options for learning more about manufacturing
Hands-on experience is the best way to learn more about manufacturing. If that is not possible, you could always read books or view educational videos.
Statistics
- It's estimated that 10.8% of the U.S. GDP in 2020 was contributed to manufacturing. (investopedia.com)
- You can multiply the result by 100 to get the total percent of monthly overhead. (investopedia.com)
- [54][55] These are the top 50 countries by the total value of manufacturing output in US dollars for its noted year according to World Bank.[56] (en.wikipedia.org)
- Many factories witnessed a 30% increase in output due to the shift to electric motors. (en.wikipedia.org)
- (2:04) MTO is a production technique wherein products are customized according to customer specifications, and production only starts after an order is received. (oracle.com)
External Links
How To
How to use 5S to increase Productivity in Manufacturing
5S stands as "Sort", Set In Order", Standardize", Separate" and "Store". Toyota Motor Corporation invented the 5S strategy in 1954. It assists companies in improving their work environments and achieving higher efficiency.
The idea behind standardizing production processes is to make them repeatable and measurable. This means that every day tasks such cleaning, sorting/storing, packing, and labeling can be performed. Because workers know what they can expect, this helps them perform their jobs more efficiently.
Five steps are required to implement 5S: Sort, Set In Order, Standardize. Separate. Each step has a different action and leads to higher efficiency. You can make it easy for people to find things later by sorting them. When you arrange items, you place them together. Then, after you separate your inventory into groups, you store those groups in containers that are easy to access. Finally, when you label your containers, you ensure everything is labeled correctly.
Employees will need to be more critical about their work. Employees need to be able understand their motivations and discover alternative ways to do them. To implement the 5S system, employees must acquire new skills and techniques.
In addition to improving efficiency, the 5S system also increases morale and teamwork among employees. They are more motivated to achieve higher efficiency levels as they start to see improvement.