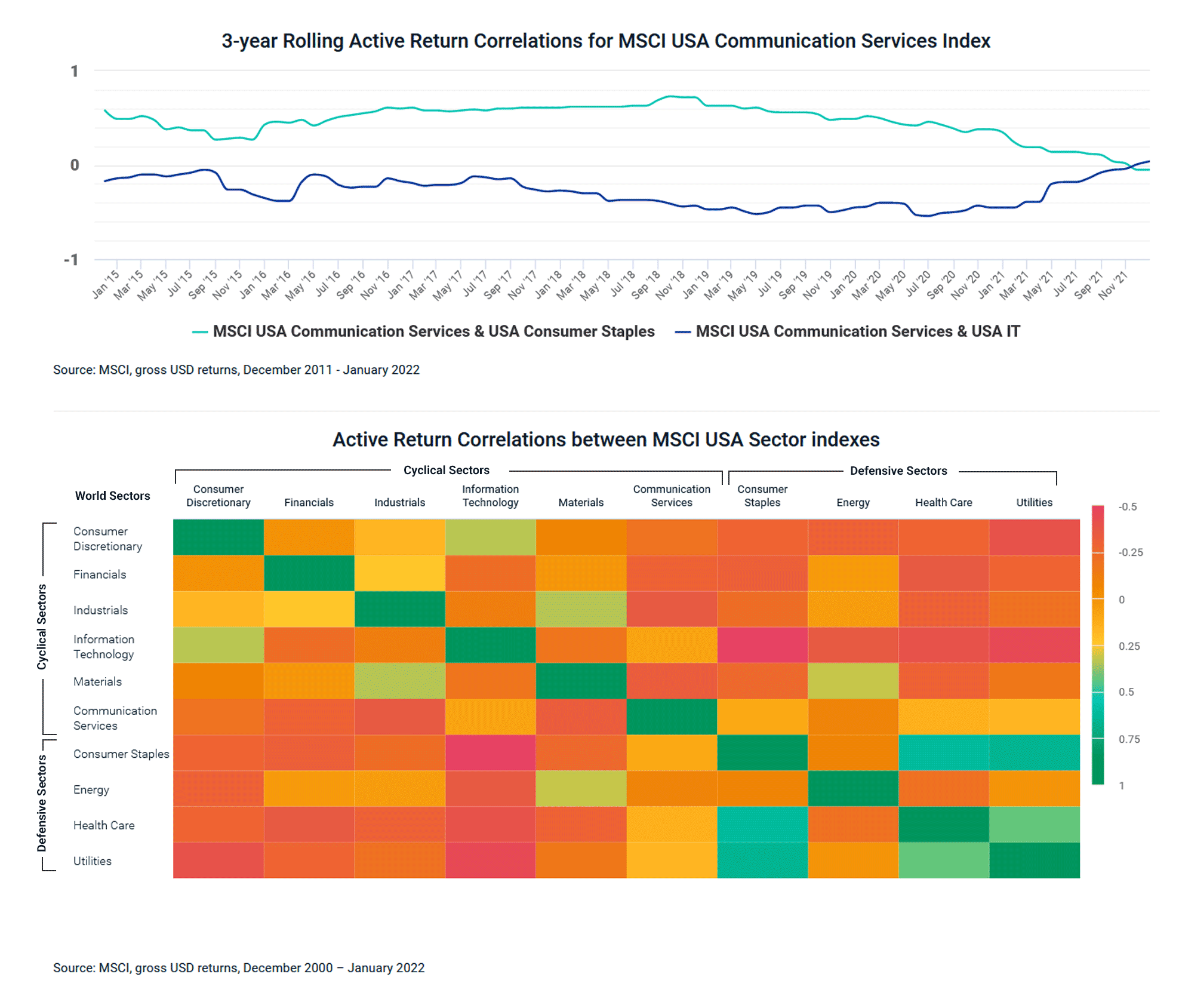
Denver, Colorado is home to a variety of job opportunities. It is home to many logistics companies, which provide a wide range of logistic services. These include freight forwarding and trucking as well as logistics and supply chain consulting.
There are several jobs you can apply for if you want to work in the industry of logistics. These include dispatch manager and transportation director. All of these positions have the responsibility of ensuring that logistics are run smoothly in an organization.
Dispatch manager
A dispatch manager coordinates and directs the activities of an entire team in a warehouse, call center or other workplace. This includes training new employees, delegating tasks, coordinating the workload of other team members, documenting productivity, and overseeing incoming and outgoing shipments. Most dispatch managers have a Bachelor's Degree in Business Management or Logistics and are experienced with workflow organization.
Transportation Director
A transportation director is in charge of logistics for a company, government department, or school. This includes setting up distribution channels and arranging for transport methods such as trucks or buses to move products from one location.
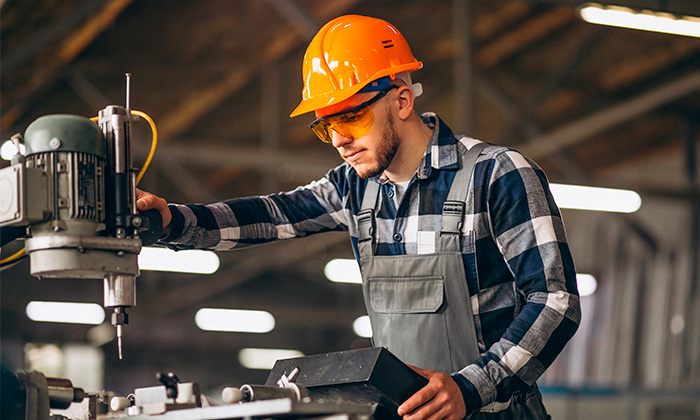
This career suits those who would like to work for an organization or government agency. You should be able to organize yourself well and work long days.
Warehouse Associate
A warehouse associate is a good option if you want a job with a flexible schedule and a lower level of competition. A warehouse associate is typically responsible for handling smaller projects, such as picking shipments and packing products. They may also be in charge of moving merchandise from one location to another.
Set up a Monster profile to begin your job search in the logistics sector. You will be notified of all the logistics jobs available in your area.
In addition, we will provide you with expert advice regarding how to get the best out of your application for a job, how to bargain your salary and much more.
Logistic Manager
A bachelor's in supply management or business administration is required to become a manager of logistics. It is necessary to have a minimum of a year's professional experience in warehouse environments, and strong organization skills. For a career as a senior logistics director, you may also need a master's in supply chain or a related field.

Logistik Analyst
A logistician monitors and changes the logistics within a business to better help them achieve their goals. This includes evaluating the inventory levels, scheduling deliveries, and determining budget restrictions. A logistics expert must have a degree in business, engineering, or both. They also need to be familiar with the specific logistics of their industry.
Logistics is a growing industry and there are a lot of jobs available. Create your free Monster account if you want to pursue a career in logistics. You'll have the best chances to find the logistics jobs that are right for you if you create a free account on Monster.
FAQ
What does "warehouse" mean?
Warehouses and storage facilities are where goods are kept before being sold. It can be an outdoor or indoor area. In some cases, it may be a combination of both.
What skills are required to be a production manager?
You must be flexible and organized to become a productive production planner. It is also important to be able communicate with colleagues and clients.
How can manufacturing avoid production bottlenecks
To avoid production bottlenecks, ensure that all processes run smoothly from the moment you receive your order to the time the product ships.
This includes both planning for capacity and quality control.
Continuous improvement techniques such Six Sigma can help you achieve this.
Six Sigma can be used to improve the quality and decrease waste in all areas of your company.
It is focused on creating consistency and eliminating variation in your work.
Statistics
- It's estimated that 10.8% of the U.S. GDP in 2020 was contributed to manufacturing. (investopedia.com)
- (2:04) MTO is a production technique wherein products are customized according to customer specifications, and production only starts after an order is received. (oracle.com)
- According to a Statista study, U.S. businesses spent $1.63 trillion on logistics in 2019, moving goods from origin to end user through various supply chain network segments. (netsuite.com)
- According to the United Nations Industrial Development Organization (UNIDO), China is the top manufacturer worldwide by 2019 output, producing 28.7% of the total global manufacturing output, followed by the United States, Japan, Germany, and India.[52][53] (en.wikipedia.org)
- In the United States, for example, manufacturing makes up 15% of the economic output. (twi-global.com)
External Links
How To
How to use the Just In-Time Production Method
Just-in time (JIT), is a process that reduces costs and increases efficiency in business operations. It's the process of obtaining the right amount and timing of resources when you need them. This means that your only pay for the resources you actually use. Frederick Taylor was the first to coin this term. He developed it while working as a foreman during the early 1900s. He noticed that workers were often paid overtime when they had to work late. He then concluded that if he could ensure that workers had enough time to do their job before starting to work, this would improve productivity.
JIT is about planning ahead. You should have all the necessary resources ready to go so that you don’t waste money. The entire project should be looked at from start to finish. You need to ensure you have enough resources to tackle any issues that might arise. You will have the resources and people to solve any problems you anticipate. This will prevent you from spending extra money on unnecessary things.
There are many types of JIT methods.
-
Demand-driven: This type of JIT allows you to order the parts/materials required for your project on a regular basis. This will let you track the amount of material left over after you've used it. This will allow to you estimate the time it will take for more to be produced.
-
Inventory-based: You stock materials in advance to make your projects easier. This allows for you to anticipate how much you can sell.
-
Project-driven: This is an approach where you set aside enough funds to cover the cost of your project. Knowing how much money you have available will help you purchase the correct amount of materials.
-
Resource-based JIT: This is the most popular form of JIT. You assign certain resources based off demand. You might assign more people to help with orders if there are many. If you don't receive many orders, then you'll assign fewer employees to handle the load.
-
Cost-based : This is similar in concept to resource-based. But here, you aren't concerned about how many people your company has but how much each individual costs.
-
Price-based pricing: This is similar in concept to cost-based but instead you look at how much each worker costs, it looks at the overall company's price.
-
Material-based: This is very similar to cost-based but instead of looking at total costs of the company you are concerned with how many raw materials you use on an average.
-
Time-based JIT is another form of resource-based JIT. Instead of focusing solely on the amount each employee costs, focus on how long it takes for the project to be completed.
-
Quality-based: This is yet another variation of resource-based JIT. Instead of focusing on the cost of each worker or how long it takes, think about how high quality your product is.
-
Value-based JIT: One of the most recent forms of JIT. This is where you don't care about how the products perform or whether they meet customers' expectations. Instead, your focus is on the value you bring to the market.
-
Stock-based is an inventory-based system that measures the number of items produced at any given moment. It's useful when you want maximum production and minimal inventory.
-
Just-in-time (JIT) planning: This is a combination of JIT and supply chain management. It is the process of scheduling components' delivery as soon as they have been ordered. It is essential because it reduces lead-times and increases throughput.