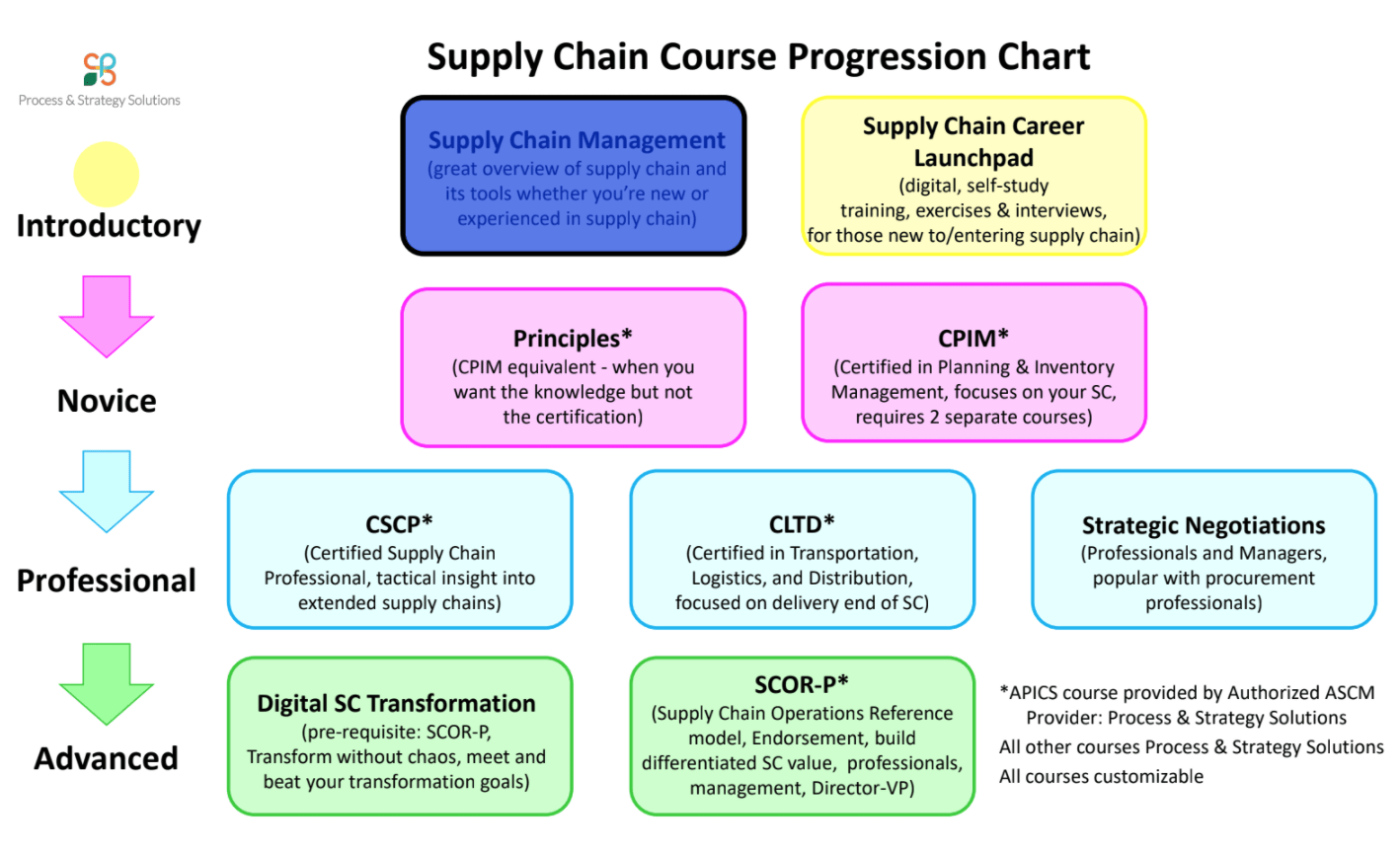
Supply chain management software is a great tool to streamline your business processes and increase efficiency, regardless of whether you run a large company or a small one. These systems give you a single view of all your supply chains, which allows you to plan production and shipment planning. They can help automate and streamline processes, so your employees can concentrate on other areas. Supply chain management software is important to every organization that controls shipping and manufacturing.
To choose the best supply-chain management software, consider several features and capabilities. These features include integration with other applications, scalability, usability, and ease-of-use. It is important to assess the reputation of your provider and the features you are offered. You should also consider your budget when choosing a solution. You can adjust to your business's needs, regardless of whether you go for a SaaS or full-scale solution.
E2open, one of the most trusted supply chain management software companies, specializes in cloud-based solution that improves demand forecasting and operations management. The company also offers advanced features and a technology platform. The software can be used by businesses in all industries, such as manufacturing, transport, and retail.
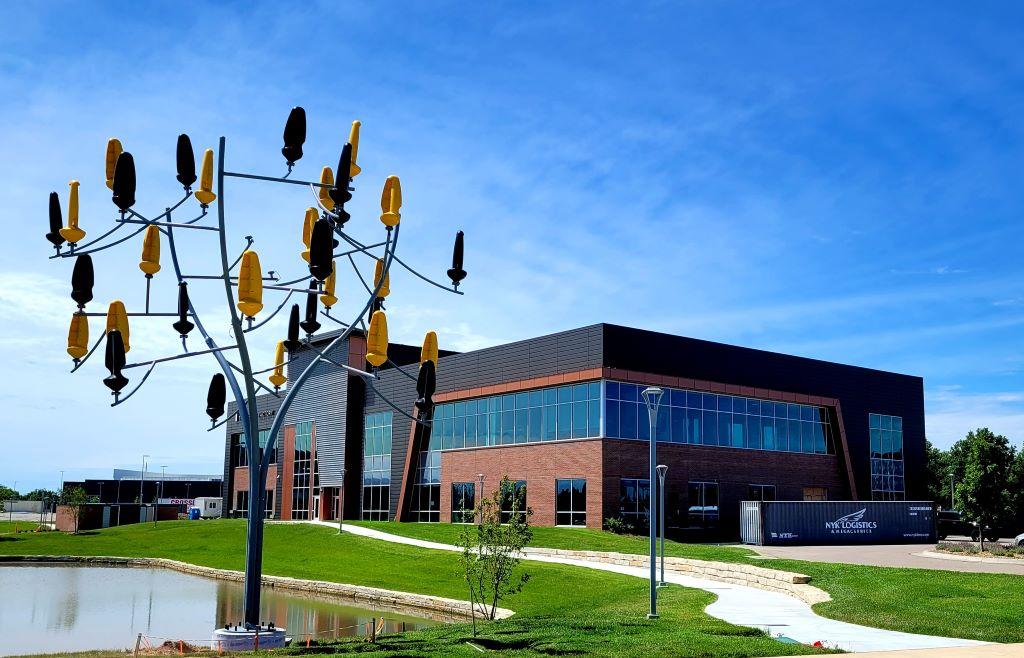
Supply chain management software has a key feature: real-time visibility. This software helps you keep track of your inventory and shipments. It ensures that customers receive what they require when they are needed. It helps you to develop long-term strategies that manage demand-supply balancing.
Kinaxis is a complete supply chain management solution that eliminates silos and streamlines processes. It combines human-machine intelligence to enable you to make better decision. It can also help you plan inventory and capacity, so you can better respond to opportunities.
Sales forecasting software allows you to better understand historical sales, sales cycles, and seasonality. It also uses machine learning to help you anticipate sales. This software allows you to predict sales and also helps prepare your sales team. You also have access to data from multiple sources so you can see the whole picture of your business.
Descartes Systems Group, the biggest competitor to supply-chain management software, is their main competitor. Many organizations consider them the best vendor. This company is home to over 13,000 active users. Its products are competitive with SAP SCM (SAP Megaventory), JDA, Logility, and JDA.

Another major competitor to supply chain management software is Manhattan Associates. This software company boasts thousands of users and a revenue of approximately $617.5million. Eddie Capel runs the company. This company competes with JDA Logility and Infor SCM.
Infor SCM has been voted one of the top supply chain management platforms. It is a perfect solution for businesses of any size and one of the most widely-used supply chain management platforms. It is a cloud-based software that unifies enterprise processes from end to end. It also includes analytics at the core, which can help you optimize your end-to-end supply chain.
FAQ
What are the products and services of logistics?
Logistics involves the transportation of goods from point A and point B.
They include all aspects associated with transport including packaging, loading transporting, unloading storage, warehousing inventory management customer service, distribution returns and recycling.
Logisticians ensure that the product is delivered to the correct place, at the right time, and under safe conditions. They assist companies with their supply chain efficiency through information on demand forecasts. Stock levels, production times, and availability.
They coordinate with vendors and suppliers, keep track of shipments, monitor quality standards and perform inventory and order replenishment.
What is production planning?
Production Planning refers to the development of a plan for every aspect of production. This document aims to ensure that everything is planned and ready when you are ready to shoot. It should also contain information on achieving the best results on set. This includes shooting schedules, locations, cast lists, crew details, and equipment requirements.
The first step is to decide what you want. You might have an idea of where you want to film, or you may have specific locations or sets in mind. Once you have identified your locations and scenes, you can start working out which elements you require for each scene. If you decide you need a car and don't know what model to choose, this could be an example. You could look online for cars to see what options are available, and then narrow down your choices by selecting between different makes or models.
After you have selected the car you want, you can begin to think about additional features. What about additional seating? Or perhaps you need someone walking around the back of the car? Maybe you want to change the interior color from black to white? These questions will help guide you in determining the ideal look and feel for your car. Also, think about what kind of shots you would like to capture. Are you going to be shooting close-ups? Or wide angles? Perhaps you want to show the engine or the steering wheel? This will allow you to determine the type of car you want.
Once you've determined the above, it is time to start creating a calendar. You can create a schedule that will outline when you must start and finish your shoots. You will need to know when you have to be there, what time you have to leave and when your return home. This way, everyone knows what they need to do and when. It is possible to make arrangements in advance for additional staff if you are looking to hire. There is no point in hiring someone who won't turn up because you didn't let him know.
It is important to calculate the amount of filming days when you are creating your schedule. Some projects can be completed in a matter of days or weeks. Others may take several days. When creating your schedule, be aware of whether you need more shots per day. Multiple takes of the same location will lead to higher costs and take more time. You can't be certain if you will need multiple takes so it is better not to shoot too many.
Budgeting is another crucial aspect of production plan. It is important to set a realistic budget so you can work within your budget. You can always lower the budget if you encounter unexpected problems. But, don't underestimate how much money you'll spend. Underestimating the cost will result in less money after you have paid for other items.
Production planning can be a complex process. However, once you know how everything works together it will become easier to plan future projects.
What is the responsibility of a production planner?
Production planners ensure that all project aspects are completed on time, within budget and within the scope. A production planner ensures that the service and product meet the client's expectations.
How can overproduction in manufacturing be reduced?
It is essential to find better ways to manage inventory to reduce overproduction. This would decrease the time that is spent on inefficient activities like purchasing, storing, or maintaining excess stock. This will allow us to free up resources for more productive tasks.
You can do this by adopting a Kanban method. A Kanban Board is a visual display that tracks work progress. A Kanban system allows work items to move through several states before reaching their final destination. Each state has a different priority level.
When work is completed, it can be transferred to the next stage. If a task is still in its beginning stages, it will continue to be so until it reaches the end.
This allows work to move forward and ensures that no work is missed. Managers can see how much work has been done and the status of each task at any time with a Kanban Board. This data allows them adjust their workflow based upon real-time data.
Lean manufacturing is another way to manage inventory levels. Lean manufacturing is about eliminating waste from all stages of the production process. Any product that isn't adding value can be considered waste. There are several types of waste that you might encounter:
-
Overproduction
-
Inventory
-
Packaging not required
-
Excess materials
Manufacturers can increase efficiency and decrease costs by implementing these ideas.
How can manufacturing avoid production bottlenecks
To avoid production bottlenecks, ensure that all processes run smoothly from the moment you receive your order to the time the product ships.
This includes both planning for capacity and quality control.
Continuous improvement techniques such Six Sigma can help you achieve this.
Six Sigma is a management method that helps to improve quality and reduce waste.
It is focused on creating consistency and eliminating variation in your work.
What does it mean to warehouse?
A warehouse is a place where goods are stored until they are sold. It can be indoors or out. In some cases it could be both indoors and outdoors.
Statistics
- [54][55] These are the top 50 countries by the total value of manufacturing output in US dollars for its noted year according to World Bank.[56] (en.wikipedia.org)
- You can multiply the result by 100 to get the total percent of monthly overhead. (investopedia.com)
- In 2021, an estimated 12.1 million Americans work in the manufacturing sector.6 (investopedia.com)
- In the United States, for example, manufacturing makes up 15% of the economic output. (twi-global.com)
- Many factories witnessed a 30% increase in output due to the shift to electric motors. (en.wikipedia.org)
External Links
How To
How to Use the Just In Time Method in Production
Just-intime (JIT), which is a method to minimize costs and maximize efficiency in business process, is one way. This is where you have the right resources at the right time. This means you only pay what you use. Frederick Taylor developed the concept while working as foreman in early 1900s. He saw how overtime was paid to workers for work that was delayed. He realized that workers should have enough time to complete their jobs before they begin work. This would help increase productivity.
JIT is a way to plan ahead and make sure you don't waste any money. It is important to look at your entire project from beginning to end and ensure that you have enough resources to handle any issues that may arise. You'll be prepared to handle any potential problems if you know in advance. This will prevent you from spending extra money on unnecessary things.
There are many JIT methods.
-
Demand-driven: This is a type of JIT where you order the parts/materials needed for your project regularly. This will allow for you to track the material that you have left after using it. You'll also be able to estimate how long it will take to produce more.
-
Inventory-based: This is a type where you stock the materials required for your projects in advance. This allows one to predict how much they will sell.
-
Project-driven: This method allows you to set aside enough funds for your project. You will be able to purchase the right amount of materials if you know what you need.
-
Resource-based JIT: This is the most popular form of JIT. Here you can allocate certain resources based purely on demand. If you have many orders, you will assign more people to manage them. If you don’t have many orders you will assign less people to the work.
-
Cost-based: This is similar to resource-based, except that here you're not just concerned about how many people you have but how much each person costs.
-
Price-based: This is a variant of cost-based. However, instead of focusing on the individual workers' costs, this looks at the total price of the company.
-
Material-based is an alternative to cost-based. Instead of looking at the total cost in the company, this method focuses on the average amount of raw materials that you consume.
-
Time-based: Another variation of resource-based JIT. Instead of focusing on the cost of each employee, you will focus on the time it takes to complete a project.
-
Quality-based JIT: This is another variation of resource based JIT. Instead of worrying about the costs of each employee or how long it takes for something to be made, you should think about how quality your product is.
-
Value-based JIT: One of the most recent forms of JIT. In this scenario, you're not concerned about how products perform or whether customers expect them to meet their expectations. Instead, you are focused on adding value to the marketplace.
-
Stock-based: This stock-based method focuses on the actual quantity of products being made at any given time. It is used when production goals are met while inventory is kept to a minimum.
-
Just-in time (JIT), planning: This is a combination JIT/supply chain management. It refers to the process of scheduling the delivery of components as soon as they are ordered. It's important because it reduces lead times and increases throughput.