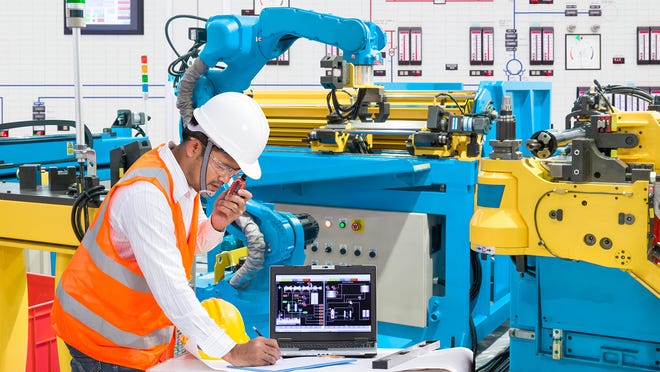
Manufacturing engineers must convert raw materials and create new, updated products. They are also responsible for creating systems that integrate the production process and supervising those who are involved in its manufacture. It is a rewarding career with high job satisfaction, and a good balance between work and life.
The average manufacturing engineer salary in the US is $77,500. This figure is based off data from TurboTax Users who declared their occupation as manufacturing engineering. It includes tips, bonuses, taxable wages, and other factors.
What is the Manufacturing Engineering Salary?
Manufacturing engineering salaries range from $28,500 up to $178.500, depending on education, skills, work experience, employer and location. Those who have experience in the industry tend to make more than those without it, whereas those who are just starting out typically earn less.
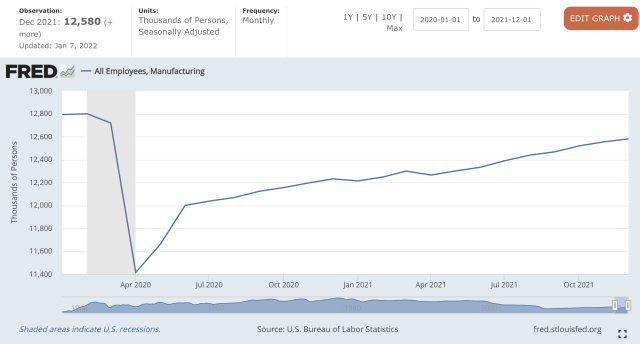
Entry Level Manufacturing Engineer Salaries: The average annual salary for an entry-level manufacturing engineering is $52,000. This amount can vary from state to state, so it's important to find out what the average pay is in your area before applying for a job.
What qualifications are required to be a manufacturing engineers?
You'll generally need a bachelor's in a relevant field. This can be in any one of the many engineering specialties or a more general subject such as computer science or electrical engineering. A graduate degree is recommended if you plan to pursue research in your chosen field or want to advance.
What does the average manufacturing engineer do?
The majority of engineers develop and design systems to improve workplace productivity. They are the experts that create processes for converting raw materials to finished products while focusing their efforts on eliminating wastefulness. The engineers have excellent problem-solving capabilities that help them identify and solve issues quickly, whether they are developing new products for the market or upgrading current ones.
What is the day-to-day work of manufacturing engineers?
The main responsibilities of a manufacturing engineer include keeping projects on track and on budget, ensuring that production is efficient and maintaining high quality. It is important that they are able to communicate well with design engineers as well as technicians and management. They should also be able to communicate effectively with design engineers, technicians and management.
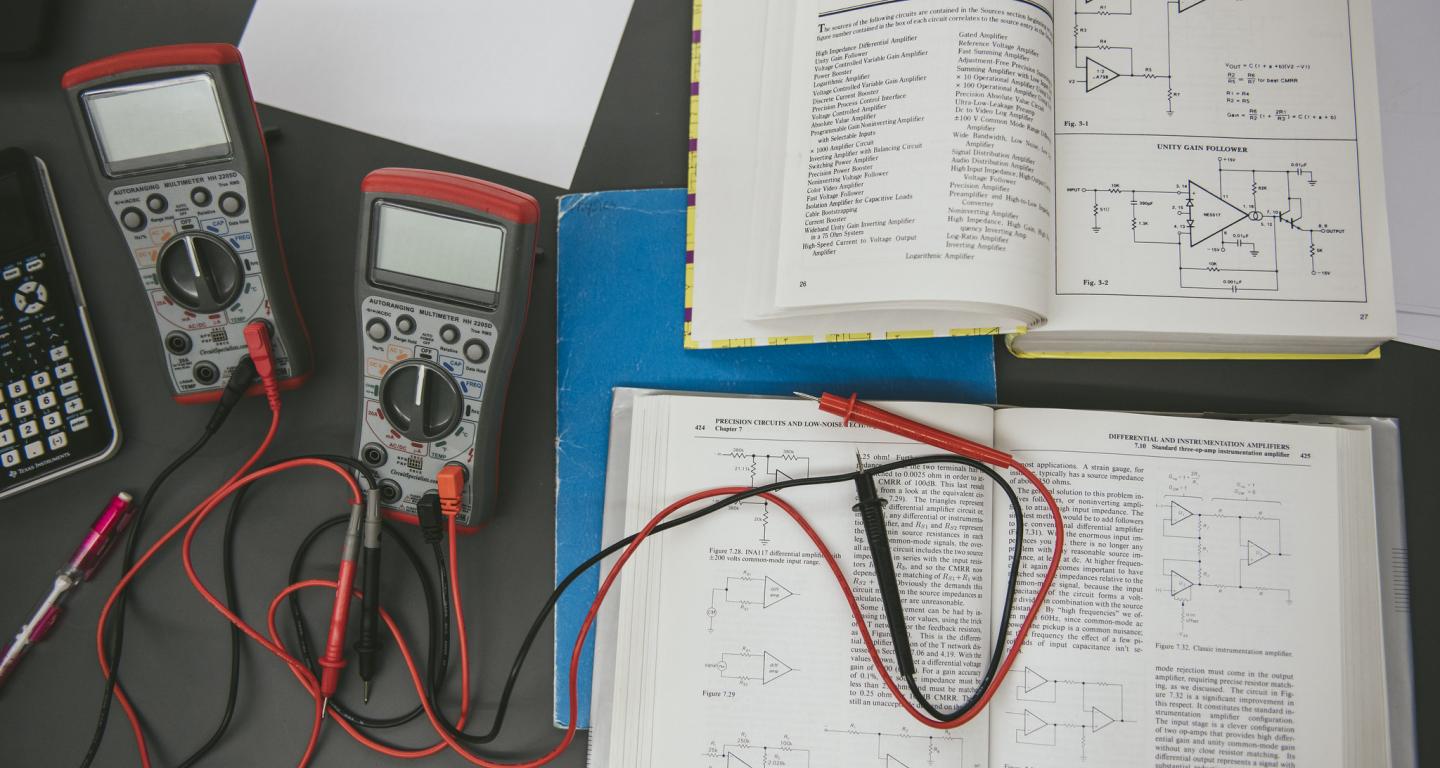
What are the qualifications to become an Industrial and Manufacturing Engineer?
Manufacturing engineers are needed in almost all companies that have their own manufacturing. Large multinational corporations, smaller companies, R&D labs, or local companies can all be included. These companies produce products ranging from pharmaceuticals to foods and drinks.
Manufacturing engineers are employed in a wide range of industries, including aerospace, defence, software and hardware, robotics, and assembly line automation. The manufacturing engineer may work in a laboratory, office or factory.
What is a typical manufacturing engineer's salary?
The US manufacturing engineer salary ranges between $57,839 and $96,809 annually. This figure was derived from data collected by 655 TurboTax customers who identified themselves as manufacturing engineers. The figures include taxable earnings, tips, bonuses, and other items.
FAQ
What is the importance of logistics in manufacturing?
Logistics are an integral part any business. They enable you to achieve outstanding results by helping manage product flow from raw materials through to finished goods.
Logistics are also important in reducing costs and improving efficiency.
What does it mean to be a manufacturer?
Manufacturing Industries are businesses that produce products for sale. These products are sold to consumers. These companies use various processes such as production, distribution, retailing, management, etc., to fulfill this purpose. They create goods from raw materials, using machines and various other equipment. This includes all types and varieties of manufactured goods, such as food items, clothings, building supplies, furnitures, toys, electronics tools, machinery vehicles, pharmaceuticals medical devices, chemicals, among others.
What are the goods of logistics?
Logistics refers to the movement of goods from one place to another.
These include all aspects related to transport such as packaging, loading and transporting, storing, transporting, unloading and warehousing inventory management, customer service. Distribution, returns, recycling are some of the options.
Logisticians ensure that products reach the right destination at the right moment and under safe conditions. They assist companies with their supply chain efficiency through information on demand forecasts. Stock levels, production times, and availability.
They can also track shipments in transit and monitor quality standards.
How can manufacturing overproduction be reduced?
It is essential to find better ways to manage inventory to reduce overproduction. This would reduce the time spent on unproductive activities like purchasing, storing and maintaining excess stock. This would allow us to use our resources for more productive tasks.
You can do this by adopting a Kanban method. A Kanban board is a visual display used to track work in progress. In a Kanban system, work items move through a sequence of states until they reach their final destination. Each state represents a different priority level.
If work is moving from one stage to the other, then the current task can be completed and moved on to the next. But if a task remains in the beginning stages it will stay that way until it reaches its end.
This allows for work to continue moving forward, while also ensuring that there is no work left behind. Managers can view the Kanban board to see how much work they have done. This allows them the ability to adjust their workflow using real-time data.
Lean manufacturing is another option to control inventory levels. Lean manufacturing seeks to eliminate waste from every step of the production cycle. Anything that does not contribute to the product's value is considered waste. These are some of the most common types.
-
Overproduction
-
Inventory
-
Packaging not required
-
Overstock materials
These ideas can help manufacturers improve efficiency and reduce costs.
Can certain manufacturing steps be automated?
Yes! Yes. The Egyptians created the wheel thousands years ago. To help us build assembly lines, we now have robots.
Robotics is used in many manufacturing processes today. These include:
-
Automated assembly line robots
-
Robot welding
-
Robot painting
-
Robotics inspection
-
Robots that create products
There are many other examples of how manufacturing could benefit from automation. 3D printing, for example, allows us to create custom products without waiting for them to be made.
Is there anything we should know about Manufacturing Processes prior to learning about Logistics.
No. You don't have to know about manufacturing processes before learning about logistics. But, being familiar with manufacturing processes will give you a better understanding about how logistics works.
How is a production manager different from a producer planner?
The main difference between a production planner and a project manager is that a project manager is usually the person who plans and organizes the entire project, whereas a production planner is mainly involved in the planning stage of the project.
Statistics
- In 2021, an estimated 12.1 million Americans work in the manufacturing sector.6 (investopedia.com)
- According to the United Nations Industrial Development Organization (UNIDO), China is the top manufacturer worldwide by 2019 output, producing 28.7% of the total global manufacturing output, followed by the United States, Japan, Germany, and India.[52][53] (en.wikipedia.org)
- According to a Statista study, U.S. businesses spent $1.63 trillion on logistics in 2019, moving goods from origin to end user through various supply chain network segments. (netsuite.com)
- Many factories witnessed a 30% increase in output due to the shift to electric motors. (en.wikipedia.org)
- You can multiply the result by 100 to get the total percent of monthly overhead. (investopedia.com)
External Links
How To
How to use lean manufacturing in the production of goods
Lean manufacturing is a management style that aims to increase efficiency and reduce waste through continuous improvement. It was developed in Japan between 1970 and 1980 by Taiichi Ohno. TPS founder Kanji Tyoda gave him the Toyota Production System, or TPS award. Michael L. Watkins published the "The Machine That Changed the World", the first book about lean manufacturing. It was published in 1990.
Lean manufacturing can be described as a set or principles that are used to improve quality, speed and cost of products or services. It emphasizes eliminating waste and defects throughout the value stream. Lean manufacturing is called just-in-time (JIT), zero defect, total productive maintenance (TPM), or 5S. Lean manufacturing seeks to eliminate non-value added activities, such as inspection, work, waiting, and rework.
In addition to improving product quality and reducing costs, lean manufacturing helps companies achieve their goals faster and reduces employee turnover. Lean manufacturing is considered one of the most effective ways to manage the entire value chain, including suppliers, customers, distributors, retailers, and employees. Lean manufacturing can be found in many industries. For example, Toyota's philosophy underpins its success in automobiles, electronics, appliances, healthcare, chemical engineering, aerospace, paper, food, etc.
Five basic principles of Lean Manufacturing are included in lean manufacturing
-
Define Value - Identify the value your business adds to society and what makes you different from competitors.
-
Reduce Waste - Eliminate any activity that doesn't add value along the supply chain.
-
Create Flow - Make sure work runs smoothly without interruptions.
-
Standardize and simplify - Make your processes as consistent as possible.
-
Build relationships - Develop and maintain personal relationships with both your internal and external stakeholders.
Although lean manufacturing has always been around, it is gaining popularity in recent years because of a renewed interest for the economy after 2008's global financial crisis. Many businesses have adopted lean production techniques to make them more competitive. According to some economists, lean manufacturing could be a significant factor in the economic recovery.
Lean manufacturing is now becoming a common practice in the automotive industry, with many benefits. These include better customer satisfaction and lower inventory levels. They also result in lower operating costs.
Lean manufacturing can be applied to almost every aspect of an organization. Because it makes sure that all value chains are efficient and effectively managed, Lean Manufacturing is particularly helpful for organizations.
There are three types principally of lean manufacturing:
-
Just-in Time Manufacturing, (JIT): This kind of lean manufacturing is also commonly known as "pull-systems." JIT is a process in which components can be assembled at the point they are needed, instead of being made ahead of time. This method reduces lead times, increases availability, and decreases inventory.
-
Zero Defects Manufacturing (ZDM): ZDM focuses on ensuring that no defective units leave the manufacturing facility. It is better to repair a part than have it removed from the production line if it needs to be fixed. This also applies to finished products that need minor repairs before being shipped.
-
Continuous Improvement (CI: Continuous improvement aims to increase the efficiency of operations by constantly identifying and making improvements to reduce or eliminate waste. It involves continuous improvement of processes, people, and tools.