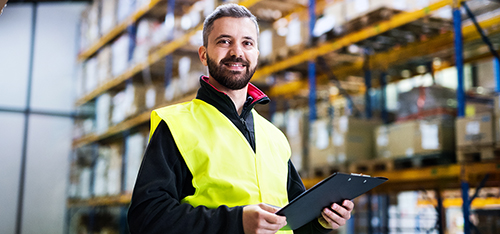
Lean training is a powerful tool for reducing waste and streamlining processes. It helps teams to work more efficiently and produces more product with less effort. But it is crucial that every person in an organization understands lean. This can be done with a training program that is tailored to the needs of each team member.
Lean training is often delivered in classrooms with a hands-on approach, combining classroom instruction and intensive hands-on experience. An average course will require trainees to be involved for between 4 and 8 hours per week. Participants are expected to be able to suggest improvements. Participants can improve the performance within their organizations by using tools like value stream mapping (PDCA) and Plan-Do-Check-Act(PDCA).
Many companies prefer to use professional or in-house lean training services. For example, Clemson University offers four different programs for their employees.
Lean training will help you and your company succeed. In fact, more companies are adopting the methodology. Look for a program that covers all the essential elements of lean.
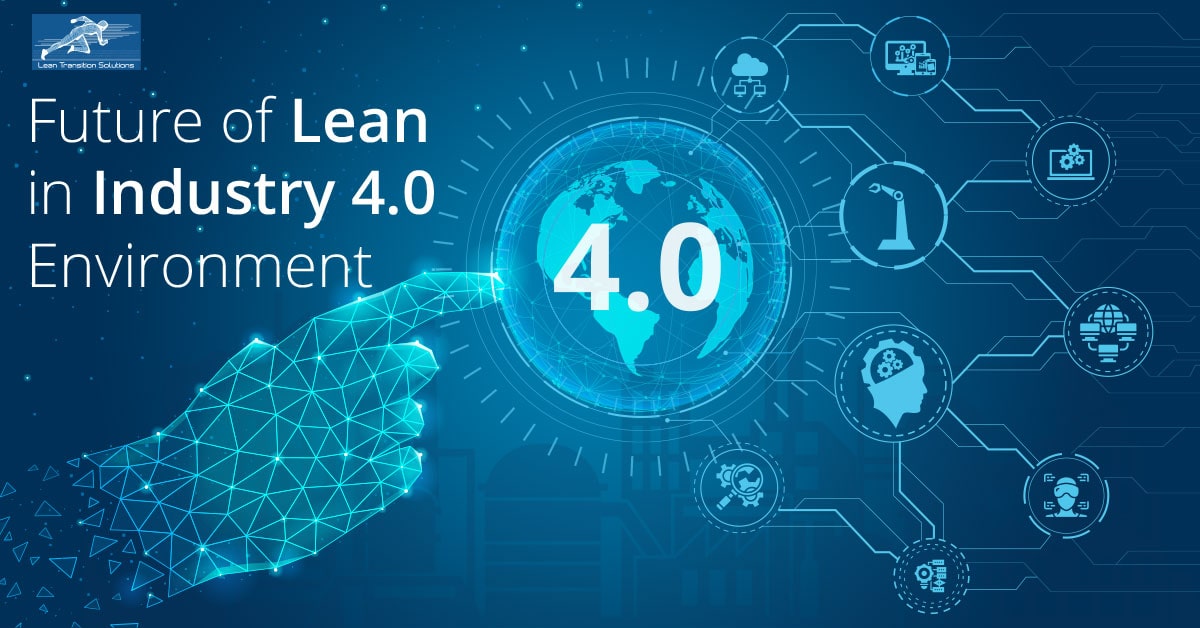
Training should begin with an introduction into lean. This workshop is two hours long and covers the history and the principles behind lean. Additionally, you will learn lean tools like value stream maps and kanban. Furthermore, you will learn how to improve the customer experience.
Once you're comfortable with the basics, the Lean Thinking unit can be completed. This unit will cover value stream mapping as well as error-proofing and continuous flow. These methods are vital to identifying and reducing waste within your business.
Afterwards, you will be introduced to Plan-Do-Check-Act. PDCA is a Lean improvement cycle that most practitioners use. During the course, you'll also study the root causes of problems.
You'll also learn how to create a lean plan. This will outline your current situation and the improvements you want to make. You'll be presented with a certificate upon completion. To obtain your certification, you must pass a multi-choice exam using the Lean Management Courseware.
You will be able apply the knowledge you have gained to your job after you have completed the program. Whether you're a manager, supervisor, or technician, you'll be able to effectively manage change and lead other team members through the process. Ultimately, you'll be able to see positive results.
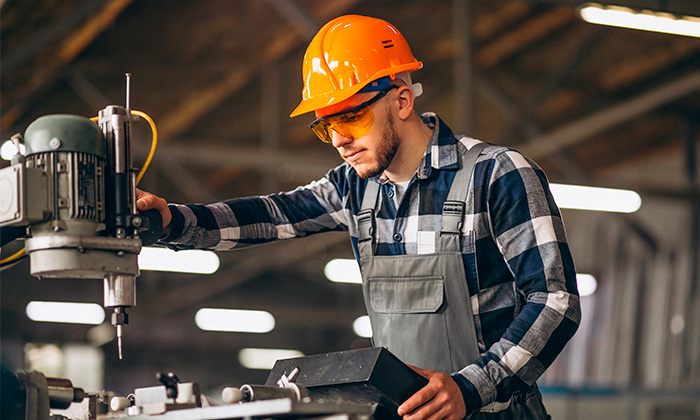
Finally, you will be able earn your Green Belt certification. The Lean training program at Virginia University Medical Center (VUMC) is managed by April Saunders. April Saunders has more than 12 years experience in the manufacturing sector and she teaches Lean.
Lean Fundamentals is available in several languages. Participants will learn how to implement Lean principles in their workplaces quickly. There is a high likelihood that this class will have an immediate effect on your organization.
This workshop is a great place to start, whether you are interested in implementing lean within your company or simply looking to improve your skills.
FAQ
What are the 7 Rs of logistics management?
The acronym 7R's of Logistic is an acronym that stands for seven fundamental principles of logistics management. It was developed and published by the International Association of Business Logisticians in 2004 as part of the "Seven Principles of Logistics Management".
The following letters form the acronym:
-
Responsible – ensure that all actions are legal and don't cause harm to anyone else.
-
Reliable - have confidence in the ability to deliver on commitments made.
-
Use resources effectively and sparingly.
-
Realistic – Consider all aspects, including cost-effectiveness as well as environmental impact.
-
Respectful - Treat people fairly and equitably
-
You are resourceful and look for ways to save money while increasing productivity.
-
Recognizable - Provide value-added services to customers
What is the role and responsibility of a Production Planner?
Production planners ensure that all project aspects are completed on time, within budget and within the scope. They ensure that the product or service is of high quality and meets client requirements.
What types of jobs can you find in logistics
There are different kinds of jobs available in logistics. Some examples are:
-
Warehouse workers: They load and unload trucks, pallets, and other cargo.
-
Transportation drivers – They drive trucks or trailers to transport goods and perform pick-ups.
-
Freight handlers: They sort and package freight in warehouses.
-
Inventory managers: They are responsible for the inventory and management of warehouses.
-
Sales reps are people who sell products to customers.
-
Logistics coordinators – They plan and coordinate logistics operations.
-
Purchasing agents are those who purchase goods and services for the company.
-
Customer service representatives – They answer emails and phone calls from customers.
-
Ship clerks - They issue bills and process shipping orders.
-
Order fillers are people who fill orders based only on what was ordered.
-
Quality control inspectors – They inspect incoming and outgoing products to ensure that there are no defects.
-
Others – There are many other types available in logistics. They include transport supervisors, cargo specialists and others.
Statistics
- Many factories witnessed a 30% increase in output due to the shift to electric motors. (en.wikipedia.org)
- According to a Statista study, U.S. businesses spent $1.63 trillion on logistics in 2019, moving goods from origin to end user through various supply chain network segments. (netsuite.com)
- In 2021, an estimated 12.1 million Americans work in the manufacturing sector.6 (investopedia.com)
- According to the United Nations Industrial Development Organization (UNIDO), China is the top manufacturer worldwide by 2019 output, producing 28.7% of the total global manufacturing output, followed by the United States, Japan, Germany, and India.[52][53] (en.wikipedia.org)
- (2:04) MTO is a production technique wherein products are customized according to customer specifications, and production only starts after an order is received. (oracle.com)
External Links
How To
Six Sigma in Manufacturing:
Six Sigma is "the application statistical process control (SPC), techniques for continuous improvement." Motorola's Quality Improvement Department created Six Sigma at their Tokyo plant, Japan in 1986. Six Sigma's basic concept is to improve quality and eliminate defects through standardization. In recent years, many companies have adopted this method because they believe there is no such thing as perfect products or services. Six Sigma's primary goal is to reduce variation from the average value of production. You can calculate the percentage of deviation from the norm by taking a sample of your product and comparing it to the average. If this deviation is too big, you know something needs fixing.
Understanding how variability works in your company is the first step to Six Sigma. Once you've understood that, you'll want to identify sources of variation. This will allow you to decide if these variations are random and systematic. Random variations occur when people do mistakes. Symmetrical variations are caused due to factors beyond the process. Random variations would include, for example, the failure of some widgets to fall from the assembly line. However, if you notice that every time you assemble a widget, it always falls apart at exactly the same place, then that would be a systematic problem.
Once you've identified where the problems lie, you'll want to design solutions to eliminate those problems. You might need to change the way you work or completely redesign the process. To verify that the changes have worked, you need to test them again. If they don't work, you will need to go back to the drawing boards and create a new plan.