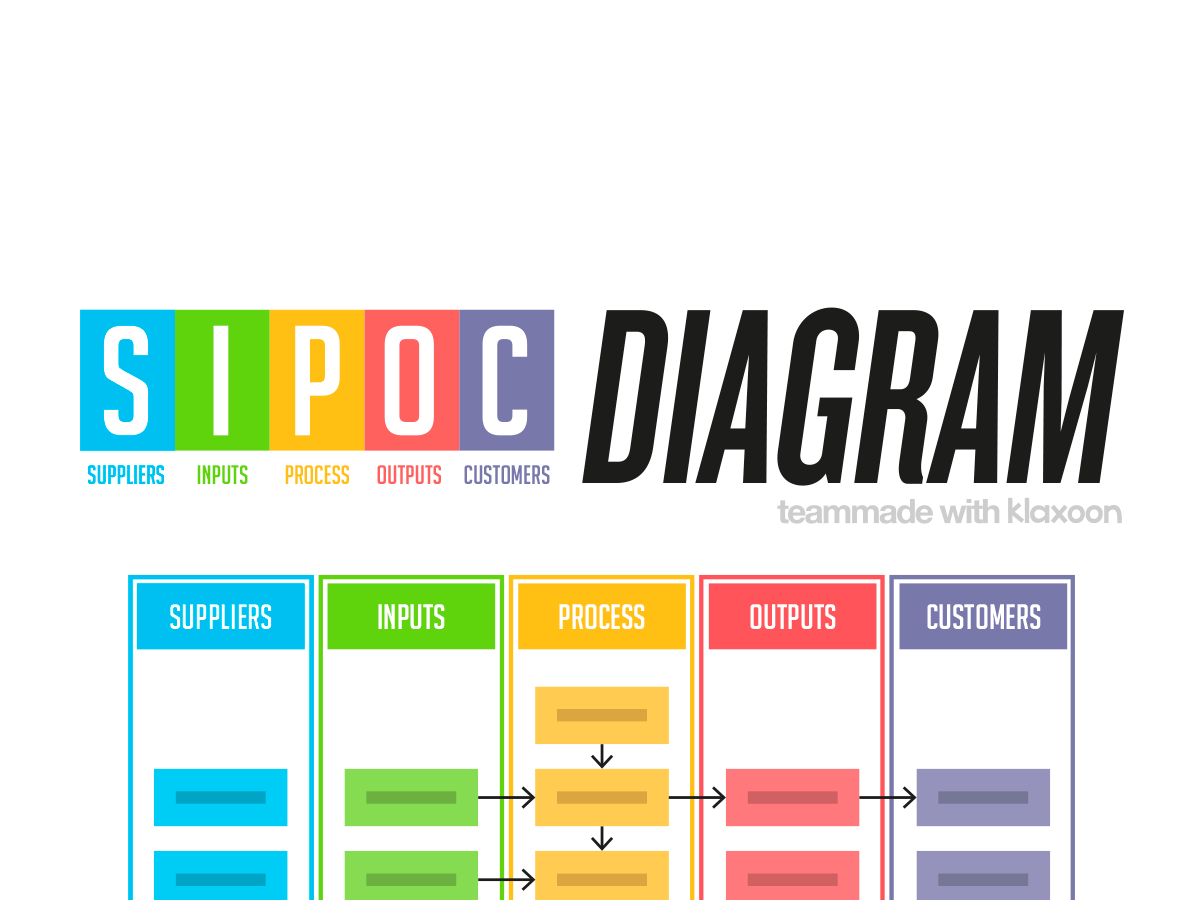
Wichita is just a few minutes from Topeka, Salina and many other great places to visit. You can also do business in Wichita if your company is looking for a new home. CTDI may be the right place for you if you're looking for logistics services.
CTDI can offer you logistics services. While there are many companies available, it stands out. CTDI is a full-service engineering and logistics company that provides a variety of services to cable companies and customers. CTDI offers the most cost-effective solutions in the communications industry and helps to improve their logistics operations. CTDI ensures that customers receive their goods in a timely manner and in excellent condition.
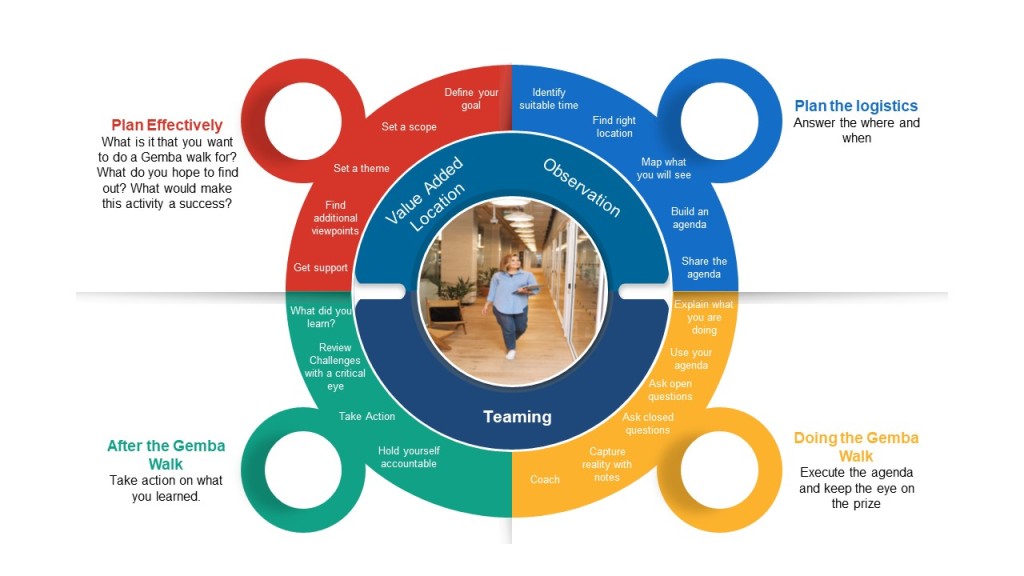
CTDI’s Wichita, Kansas office is located at North Comotara Street. The company has a number of other facilities throughout the United States, as well as 47 locations in Canada and China. Although the company employs a few people, the company is growing as it begins to serve the markets in Wichita and Oklahoma City.
CTDI has been operating for many years and offers services to some the biggest cable providers in the United States. For Cisco, for example, they have a Cisco-certified repair facility. They also have impressive facilities in Canada, China and Europe. Their inventory includes a variety of telecommunications products including wireline and wireless telephones as well as cable television sets. Many cable companies use their products including Spectrum Cable, AT&T Time Warner, Verizon, Comcast and Spectrum.
CTDI's recent acquisition of a state-of-the-art distribution center for Cox Communications is one of their most notable accomplishments. This Cox distribution center will be the biggest in Kansas. The company plans to expand this facility to include a service center. CTDI will be adding more staff to Wichita as the center expands.
The company also operates a telecommunications hub in West Chester. The facility was awarded a number of awards by the Transportation Research Board, such as being the cheapest carrier for its class and the lowest carrier for its state class by the Society for Logistics Management. The company has also provided engineering services to the cable sector, which is another impressive achievement. The most remarkable feat of the company was its ability provide services to the biggest telecommunications firms in the world.
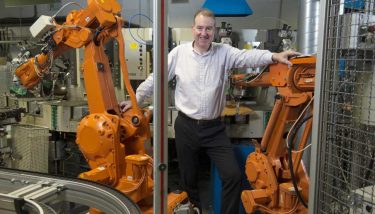
CTDI's most notable achievement is its use the latest technology to offer the best logistics solutions to its customers. They also offer equal opportunities to all employees, including those of different races and genders. The company also offers many other fun and interesting benefits such as a health club or a free gym.
FAQ
What are the 7 R's of logistics?
The acronym 7R's for Logistics stands to represent the seven basic principles in logistics management. It was developed and published by the International Association of Business Logisticians in 2004 as part of the "Seven Principles of Logistics Management".
The following letters make up the acronym:
-
Responsible – ensure that all actions are legal and don't cause harm to anyone else.
-
Reliable - You can have confidence that you will fulfill your promises.
-
Reasonable - make sure you use your resources well and don't waste them.
-
Realistic – consider all aspects of operations, from cost-effectiveness to environmental impact.
-
Respectful – Treat others fairly and equitably.
-
Resourceful - look for opportunities to save money and increase productivity.
-
Recognizable provides value-added products and services to customers
How can manufacturing reduce production bottlenecks?
You can avoid bottlenecks in production by making sure that everything runs smoothly throughout the production cycle, from the moment you receive an order to the moment the product is shipped.
This includes planning for capacity requirements as well as quality control measures.
Continuous improvement techniques such Six Sigma can help you achieve this.
Six Sigma management is a system that improves quality and reduces waste within your organization.
It focuses on eliminating variation and creating consistency in your work.
What does it take for a logistics enterprise to succeed?
To run a successful logistics company, you need a lot knowledge and skills. For clients and suppliers to be successful, you need to have excellent communication skills. You should be able analyse data and draw inferences. You will need to be able handle pressure well and work in stressful situations. You need to be innovative and creative to come up with new ways to increase efficiency. To motivate and guide your team towards reaching organizational goals, you must have strong leadership skills.
It is also important to be efficient and well organized in order meet deadlines.
How can I learn about manufacturing?
Hands-on experience is the best way to learn more about manufacturing. If that is not possible, you could always read books or view educational videos.
What is the difference between Production Planning and Scheduling?
Production Planning (PP), is the process of deciding what production needs to take place at any given time. This is accomplished by forecasting the demand and identifying production resources.
Scheduling refers to the process of allocating specific dates to tasks in order that they can be completed within a specified timeframe.
What does warehouse refer to?
A warehouse or storage facility is where goods are stored before they are sold. It can be an outdoor or indoor area. It may also be an indoor space or an outdoor area.
What is the role and responsibility of a Production Planner?
A production planner makes sure all project elements are delivered on schedule, within budget, as well as within the agreed scope. They ensure that the product or service is of high quality and meets client requirements.
Statistics
- According to the United Nations Industrial Development Organization (UNIDO), China is the top manufacturer worldwide by 2019 output, producing 28.7% of the total global manufacturing output, followed by the United States, Japan, Germany, and India.[52][53] (en.wikipedia.org)
- In 2021, an estimated 12.1 million Americans work in the manufacturing sector.6 (investopedia.com)
- You can multiply the result by 100 to get the total percent of monthly overhead. (investopedia.com)
- Job #1 is delivering the ordered product according to specifications: color, size, brand, and quantity. (netsuite.com)
- [54][55] These are the top 50 countries by the total value of manufacturing output in US dollars for its noted year according to World Bank.[56] (en.wikipedia.org)
External Links
How To
Six Sigma and Manufacturing
Six Sigma refers to "the application and control of statistical processes (SPC) techniques in order to achieve continuous improvement." Motorola's Quality Improvement Department developed it at their Tokyo plant in Japan in 1986. The basic idea behind Six Sigma is to improve quality by improving processes through standardization and eliminating defects. In recent years, many companies have adopted this method because they believe there is no such thing as perfect products or services. Six Sigma's main objective is to reduce variations from the production average. It is possible to measure the performance of your product against an average and find the percentage of time that it differs from the norm. If there is a significant deviation from the norm, you will know that something needs to change.
Understanding how your business' variability is a key step towards Six Sigma implementation is the first. Once you understand this, you can then identify the causes of variation. It is important to identify whether the variations are random or systemic. Random variations occur when people do mistakes. Symmetrical variations are caused due to factors beyond the process. If you make widgets and some of them end up on the assembly line, then those are considered random variations. It would be considered a systematic problem if every widget that you build falls apart at the same location each time.
Once you have identified the problem, you can design solutions. This could mean changing your approach or redesigning the entire process. You should then test the changes again after they have been implemented. If they don't work you need to rework them and come up a better plan.