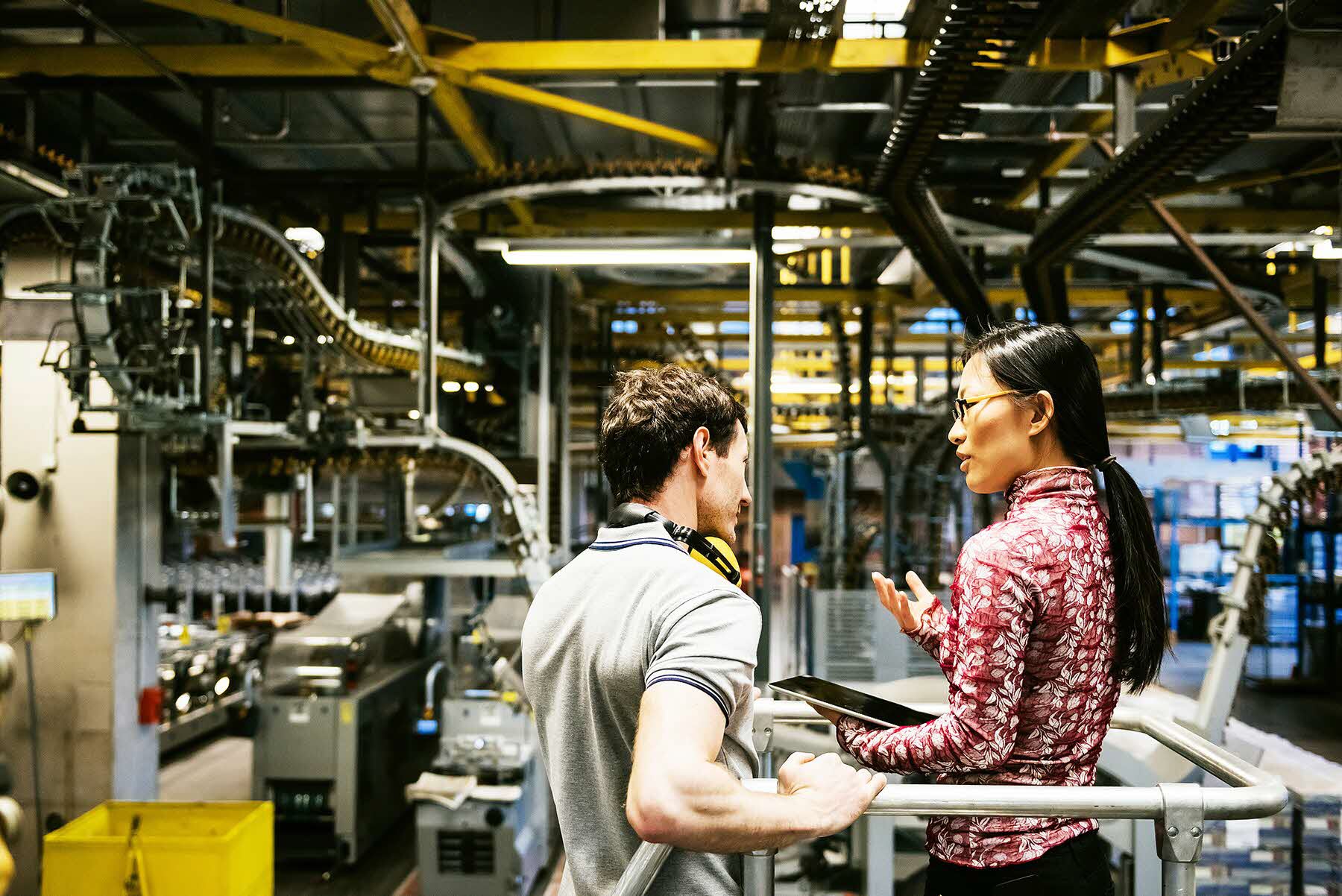
It may be more difficult than you think to introduce kaizen to manufacturing processes. It takes time to obtain inventory and ensure everyone is present. The length of this improvement project depends on the type of company and participation level. Be sure to follow the right methods of implementation and gather the necessary resources in order to make your manufacturing improvement initiative a success. You must create a company culture that encourages continual improvement in order to make this strategy a success.
Creating a culture in the company that is focused on improving
Gallup polls found that 32% of Americans are not engaged in their work. 17.2% of these employees were actively disengaged. Kaizen culture can be implemented to encourage employee engagement. This will lead to improved processes, lower turnover, and more innovation. In addition, engaged employees are more likely to contribute ideas and innovate, leading to higher productivity and customer satisfaction. Kaizen culture offers more benefits than reducing waste, increasing productivity, and increasing customer satisfaction.
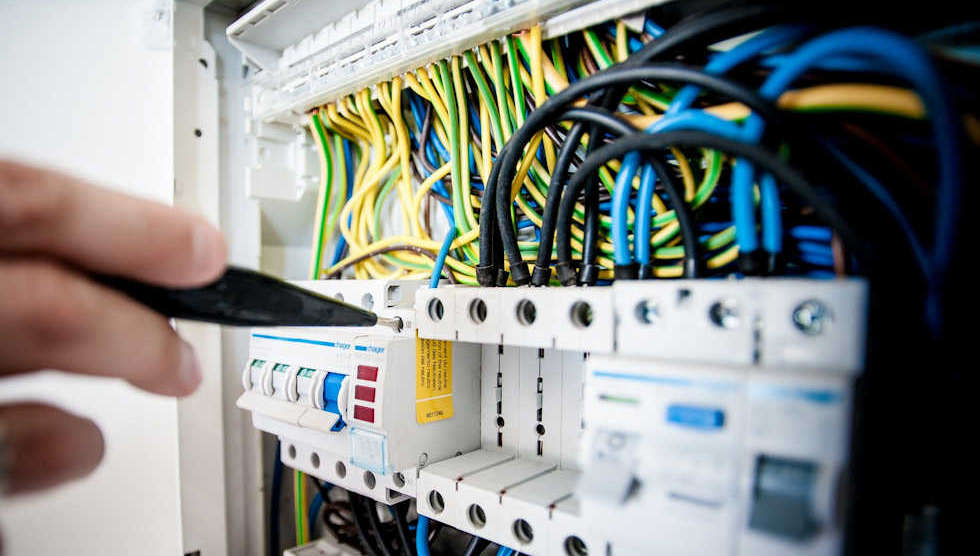
Kaizen is a philosophy that encourages continuous improvement in every area of a business. Kaizen is not about making drastic changes that will have little or no impact on the business. Instead, it's about incremental improvement. Kaizen can help reduce costs, increase productivity, improve quality, and improve customer satisfaction when implemented properly. It is also a great way to increase employee morale.
Obstacles to implementing kaizen in manufacturing
Even though there are many benefits to kaizen, they have their drawbacks. First, the implementation of kaizen can require major changes to a business's managerial system. It can be difficult to reverse any changes made once the changes have been made. Second, it is often difficult for businesses to make changes to their work processes, which could be a barrier to kaizen implementation.
Another common problem is that many manufacturing companies operate on a cycle of "feast and famine". If there is not enough demand for their products, a machine shop can run into problems. In such a scenario, they will have to layoff employees and close their doors. But implementing kaizen, or continuous improvement, will help steer these machine shops away from the "feast or famine" cycle. Implementing kaizen will increase a shop's efficiency and allow it to produce more products.
Kaizen implementation in manufacturing is a success rate
Statistics show that Kaizen implementation in the manufacturing industry is very low. Only 10% percent of manufacturing companies have reported positive Kaizen outcomes. The implementation process does not have to be boring. Implementing Kaizen is an integral part of lean manufacturing. Here are some tips that will help you increase the success of your manufacturing business.
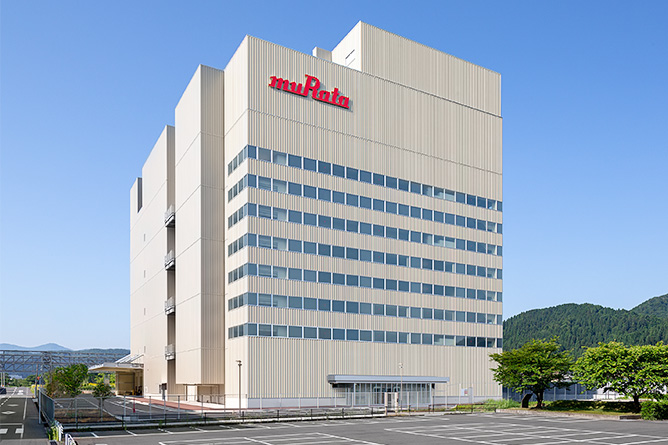
Understanding the state of the world is essential to kaizen. During the first step, data is collected and analyzed to identify the highest priorities. The next step is to test and verify improvements by performing a comparison of the before-and-after. Benefit-to-cost analysis can also be used to understand the impact of a specific improvement or the whole kaizen process. To assess the program's effectiveness, it is crucial to monitor the results for 60 to 90 days.
FAQ
What is the importance of automation in manufacturing?
Not only is automation important for manufacturers, but it's also vital for service providers. It allows them provide faster and more efficient services. It helps them to lower costs by reducing human errors, and improving productivity.
What are the products of logistics?
Logistics refers to all activities that involve moving goods from A to B.
They encompass all aspects transport, including packaging and loading, transporting, storage, unloading.
Logisticians ensure that products reach the right destination at the right moment and under safe conditions. Logisticians assist companies in managing their supply chains by providing information such as demand forecasts, stock levels and production schedules.
They also keep track of shipments in transit, monitor quality standards, perform inventories and order replenishment, coordinate with suppliers and vendors, and provide support services for sales and marketing.
How can excess manufacturing production be reduced?
Better inventory management is key to reducing excess production. This would decrease the time that is spent on inefficient activities like purchasing, storing, or maintaining excess stock. This could help us free up our time for other productive tasks.
This can be done by using a Kanban system. A Kanban board is a visual display used to track work in progress. A Kanban system allows work items to move through several states before reaching their final destination. Each state represents a different priority level.
For instance, when work moves from one stage to another, the current task is complete enough to be moved to the next stage. If a task is still in its beginning stages, it will continue to be so until it reaches the end.
This allows for work to continue moving forward, while also ensuring that there is no work left behind. Managers can view the Kanban board to see how much work they have done. This information allows them to adjust their workflow based on real-time data.
Lean manufacturing can also be used to reduce inventory levels. Lean manufacturing focuses on eliminating waste throughout the entire production chain. Any product that isn't adding value can be considered waste. These are some of the most common types.
-
Overproduction
-
Inventory
-
Unnecessary packaging
-
Excess materials
These ideas can help manufacturers improve efficiency and reduce costs.
Is it necessary to be familiar with Manufacturing Processes before we learn about Logistics.
No. It doesn't matter if you don't know anything about manufacturing before you learn about logistics. Knowing about manufacturing processes will help you understand how logistics works.
Statistics
- In 2021, an estimated 12.1 million Americans work in the manufacturing sector.6 (investopedia.com)
- (2:04) MTO is a production technique wherein products are customized according to customer specifications, and production only starts after an order is received. (oracle.com)
- According to a Statista study, U.S. businesses spent $1.63 trillion on logistics in 2019, moving goods from origin to end user through various supply chain network segments. (netsuite.com)
- You can multiply the result by 100 to get the total percent of monthly overhead. (investopedia.com)
- Many factories witnessed a 30% increase in output due to the shift to electric motors. (en.wikipedia.org)
External Links
How To
How to use the Just In-Time Production Method
Just-in time (JIT), is a process that reduces costs and increases efficiency in business operations. It is a process where you get the right amount of resources at the right moment when they are needed. This means that you only pay the amount you actually use. Frederick Taylor, a 1900s foreman, first coined the term. He noticed that workers were often paid overtime when they had to work late. He decided to ensure workers have enough time to do their jobs before starting work to improve productivity.
JIT teaches you to plan ahead and prepare everything so you don’t waste time. It is important to look at your entire project from beginning to end and ensure that you have enough resources to handle any issues that may arise. If you expect problems to arise, you will be able to provide the necessary equipment and personnel to address them. This will prevent you from spending extra money on unnecessary things.
There are several types of JIT techniques:
-
Demand-driven: This JIT is where you place regular orders for the parts/materials that are needed for your project. This will allow for you to track the material that you have left after using it. It will also allow you to predict how long it takes to produce more.
-
Inventory-based : You can stock the materials you need in advance. This allows you to predict how much you can expect to sell.
-
Project-driven: This approach involves setting aside sufficient funds to cover your project's costs. Once you have an idea of how much material you will need, you can purchase the necessary materials.
-
Resource-based JIT: This is the most popular form of JIT. You allocate resources based on the demand. You will, for example, assign more staff to deal with large orders. If you don’t have many orders you will assign less people to the work.
-
Cost-based: This approach is very similar to resource-based. However, you don't just care about the number of people you have; you also need to consider how much each person will cost.
-
Price-based: This is a variant of cost-based. However, instead of focusing on the individual workers' costs, this looks at the total price of the company.
-
Material-based: This is very similar to cost-based but instead of looking at total costs of the company you are concerned with how many raw materials you use on an average.
-
Time-based JIT: This is another variant of resource-based JIT. Instead of focusing only on how much each employee is costing, you should focus on how long it takes to complete your project.
-
Quality-based JIT - This is another form of resource-based JIT. Instead of looking at the labor costs and time it takes to make a product, think about its quality.
-
Value-based JIT : This is the newest type of JIT. You don't worry about whether the products work or if they meet customer expectations. Instead, your goal is to add value to the market.
-
Stock-based: This inventory-based approach focuses on how many items are being produced at any one time. It's useful when you want maximum production and minimal inventory.
-
Just-in time (JIT), planning: This is a combination JIT/supply chain management. It is the process that schedules the delivery of components within a short time of their order. It's important as it reduces leadtimes and increases throughput.