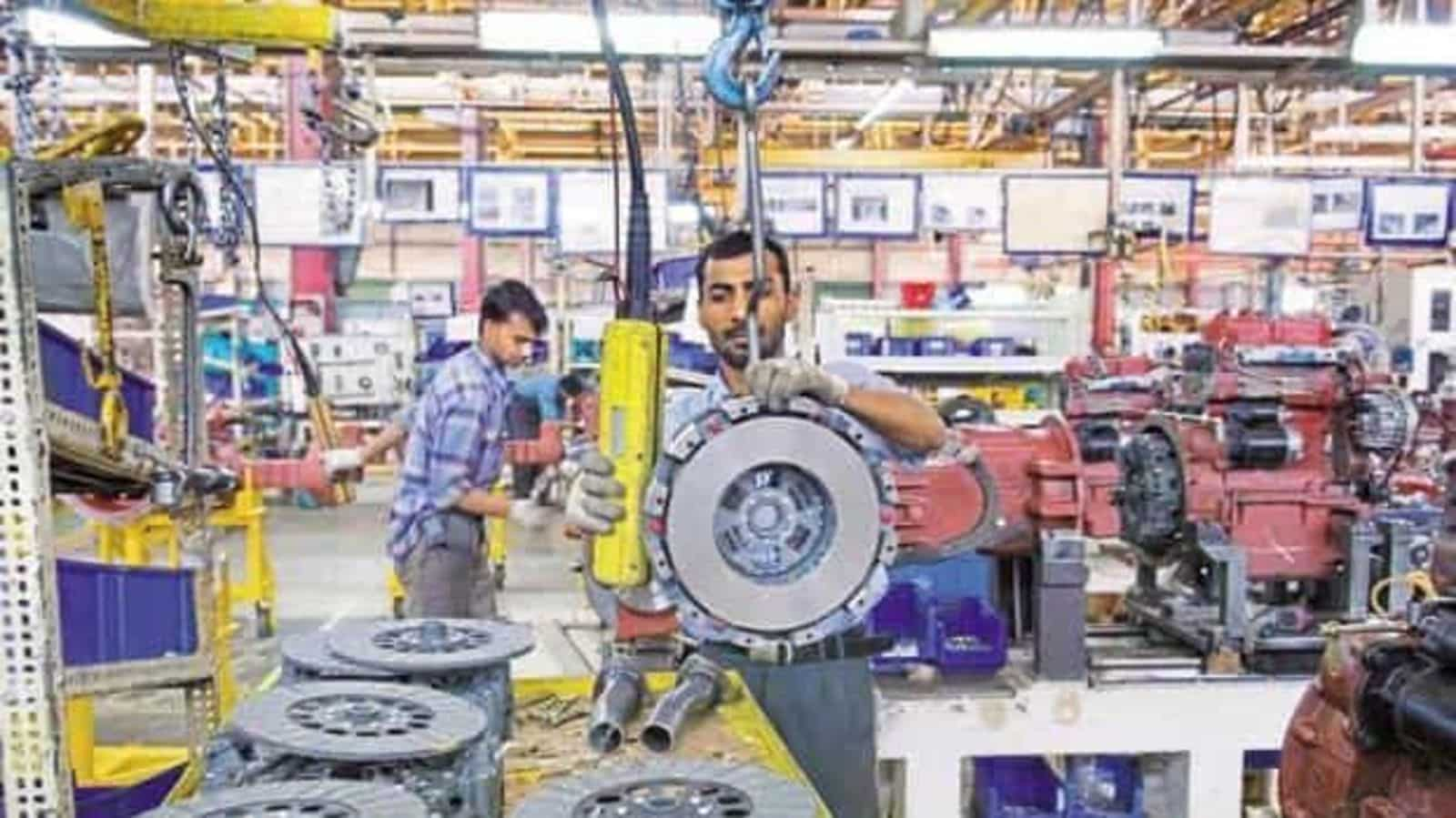
If you're looking to cut costs and improve lead times while minimizing set-up and turnaround time, consider using lean manufacturing. Lean manufacturing has clear benefits. They reduce lead times and costs while improving customer service. These improvements make Lean Manufacturing the best way for your business to grow. You might still be skeptical, but here are three reasons it is the best way to produce products and reduce costs.
Reduces costs
Lean manufacturing has the potential to bring about significant efficiency. Lean manufacturing can help manufacturers save money by reducing labor costs and reducing defects. In this way, labor costs are less motivating for decision-making. Another benefit is the elimination of hazardous waste. Direct labor costs are below 15% in many industries. It is difficult to justify outsourcing manufacturing to low cost locations. This can lower overall manufacturing costs and improve customer services.
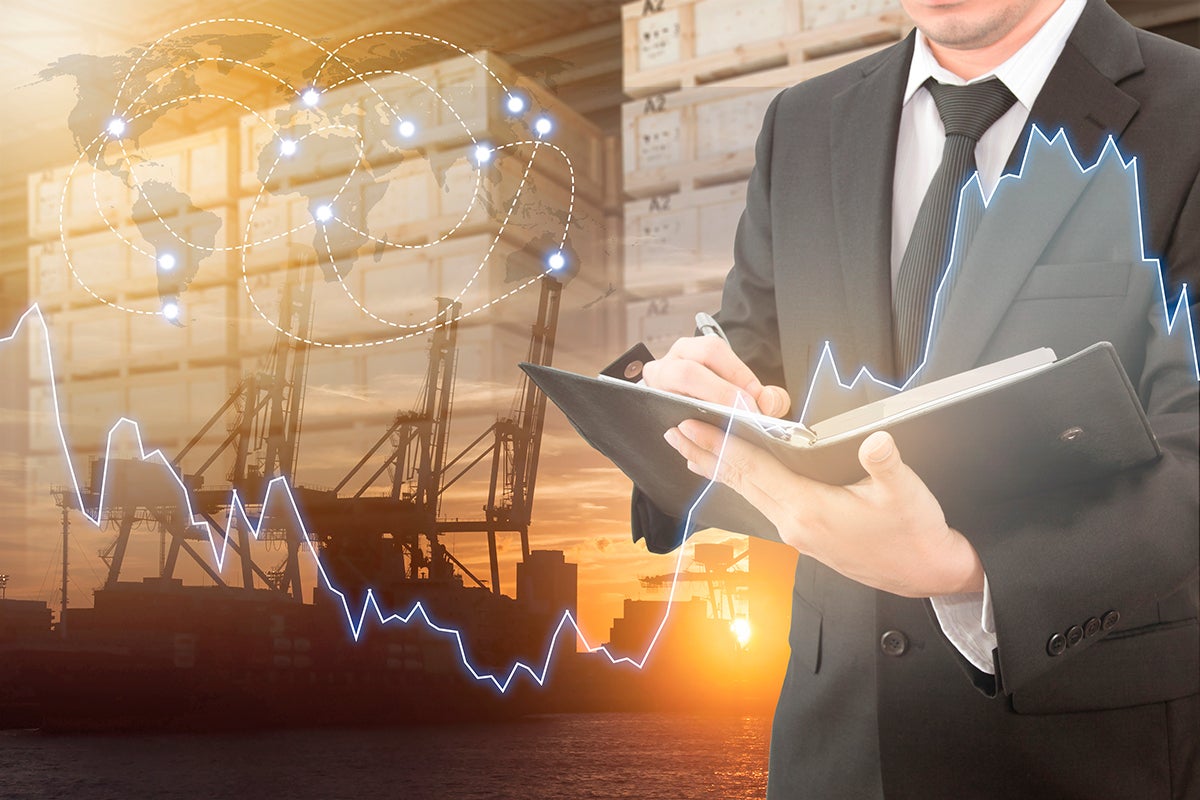
Reduces lead times
Lean manufacturing has many benefits, including the ability reduce waste and increase lead times. Lean manufacturing is a philosophy that emphasizes continuous improvement or kaizen. It is a system that combines the talents and encourages employee collaboration. It can increase lead times up to 20% Lean manufacturing's most important feature is its ability to make small, but significant improvements to product quality and efficiency.
Shortens set-up times
Reducing set-up times is one way to decrease the time needed to produce a product. The time it takes for a product to be switched from its last item to the new one is called setup time. This includes all activities related to preparation, replacement and location. These activities can be internal or external. Internal activities, like moving or positioning an item, require that the process be inactive. However, external setup activities may still be possible.
Reduces time to market
Lean manufacturing, also known as continuous improvement, was first developed in Japan in the period of rebuilding after World War II. It was intended to improve market competitiveness and shorten lead times. By shortening the time it takes for a product to reach the market, companies can meet customer demands and increase profitability. This production approach can improve the efficiency of the manufacturing process and make the facility more efficient.
Improves product quality
To be successful in lean manufacturing, it is important to reduce waste, improve product value, and minimize costs. It is used by both large manufacturers and smaller businesses alike. It decreases lead times, costs, and labor. You can learn more about the benefits of lean manufacturing for your business by reading this article. Here are a few of the key areas to focus on. Lean principles are a way to reduce lead times and improve product quality while lowering costs.
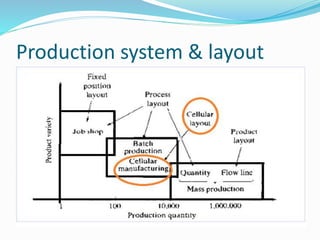
This reduces indirect labor costs
Lean manufacturing's low hanging fruit is the reduction of indirect labor cost. True lean companies do not pay too much attention to direct labor efficiency. Instead, they look for ways of reducing indirect labor costs. This means eliminating maintenance, inspection, management, and material handling jobs, as well as pushing decisions to the production floor. This is the same method used by Toyota and other lean manufacturing firms. In this article, we'll take a closer look at how lean manufacturing can lower indirect labor costs.
FAQ
What does it take to run a logistics business?
A successful logistics business requires a lot more than just knowledge. You must have good communication skills to interact effectively with your clients and suppliers. You will need to know how to interpret data and draw conclusions. You need to be able work under pressure and manage stressful situations. In order to innovate and create new ways to improve efficiency, creativity is essential. To motivate and guide your team towards reaching organizational goals, you must have strong leadership skills.
To meet tight deadlines, you must also be efficient and organized.
What is production plan?
Production planning is the process of creating a plan that covers all aspects of production. This includes scheduling, budgeting and crew, location, equipment, props, and more. It is important to have everything ready and planned before you start shooting. You should also have information to ensure the best possible results on set. This includes information on shooting times, locations, cast lists and crew details.
The first step is to decide what you want. You may already know where you want the film to be shot, or perhaps you have specific locations and sets you wish to use. Once you have determined your scenes and locations, it is time to start figuring out the elements that you will need for each scene. You might decide you need a car, but not sure what make or model. To narrow your options, you can search online for available models.
Once you have found the right vehicle, you can think about adding accessories. You might need to have people in the front seats. Perhaps you have someone who needs to be able to walk around the back of your car. Maybe you want to change the interior color from black to white? These questions will help you determine the exact look and feel of your car. The type of shots that you are looking for is another thing to consider. You will be filming close-ups and wide angles. Maybe you want the engine or the steering wheels to be shown. All of these things will help you identify the exact style of car you want to film.
Once you have established all the details, you can create a schedule. The schedule will show you when to begin shooting and when to stop. The schedule will show you when to get there, what time to leave, and when to return home. So everyone is clear about what they need to do. Book extra staff ahead of time if you need them. It's not worth paying someone to show up if you haven't told him.
You will need to factor in the days that you have to film when creating your schedule. Some projects only take one or two days, while others may last weeks. When you are creating your schedule, you should always keep in mind whether you need more than one shot per day or not. Multiple takes at the same place will result in higher costs and longer completion times. It is better to be cautious and take fewer shots than you risk losing money if you are not sure if multiple takes are necessary.
Budgeting is another crucial aspect of production plan. As it will allow you and your team to work within your financial means, setting a realistic budget is crucial. You can always lower the budget if you encounter unexpected problems. It is important to not overestimate how much you will spend. You'll end up with less money after paying for other things if the cost is underestimated.
Production planning is a detailed process. But, once you understand the workings of everything, it becomes easier for future projects to be planned.
Why automate your factory?
Modern warehouses are increasingly dependent on automation. E-commerce has increased the demand for quicker delivery times and more efficient processes.
Warehouses must be able to quickly adapt to changing demands. They must invest heavily in technology to do this. Automation of warehouses offers many benefits. These are some of the benefits that automation can bring to warehouses:
-
Increases throughput/productivity
-
Reduces errors
-
Increases accuracy
-
Safety is boosted
-
Eliminates bottlenecks
-
Allows companies to scale more easily
-
Makes workers more efficient
-
It gives visibility to everything that happens inside the warehouse
-
Enhances customer experience
-
Improves employee satisfaction
-
Reduces downtime and improves uptime
-
This ensures that quality products are delivered promptly
-
Eliminates human error
-
It helps ensure compliance with regulations
How can manufacturing excess production be decreased?
In order to reduce excess production, you need to develop better inventory management methods. This would decrease the time that is spent on inefficient activities like purchasing, storing, or maintaining excess stock. This could help us free up our time for other productive tasks.
This can be done by using a Kanban system. A Kanban board, a visual display to show the progress of work, is called a Kanban board. Work items are moved through various states to reach their destination in a Kanban system. Each state represents a different priority.
If work is moving from one stage to the other, then the current task can be completed and moved on to the next. But if a task remains in the beginning stages it will stay that way until it reaches its end.
This helps to keep work moving forward while ensuring that no work is left behind. With a Kanban board, managers can see exactly how much work is being done at any given moment. This information allows them to adjust their workflow based on real-time data.
Another way to control inventory levels is to implement lean manufacturing. Lean manufacturing emphasizes eliminating waste in all phases of production. Any product that isn't adding value can be considered waste. Some common types of waste include:
-
Overproduction
-
Inventory
-
Unnecessary packaging
-
Excess materials
These ideas will help manufacturers increase efficiency and lower costs.
What do you mean by warehouse?
A warehouse is a place where goods are stored until they are sold. It can be either an indoor or outdoor space. In some cases it could be both indoors and outdoors.
How can manufacturing efficiency improved?
First, determine which factors have the greatest impact on production time. Next, we must find ways to improve those factors. If you don't know where to start, then think about which factor(s) have the biggest impact on production time. Once you've identified them all, find solutions to each one.
Statistics
- It's estimated that 10.8% of the U.S. GDP in 2020 was contributed to manufacturing. (investopedia.com)
- According to a Statista study, U.S. businesses spent $1.63 trillion on logistics in 2019, moving goods from origin to end user through various supply chain network segments. (netsuite.com)
- (2:04) MTO is a production technique wherein products are customized according to customer specifications, and production only starts after an order is received. (oracle.com)
- Job #1 is delivering the ordered product according to specifications: color, size, brand, and quantity. (netsuite.com)
- You can multiply the result by 100 to get the total percent of monthly overhead. (investopedia.com)
External Links
How To
How to Use Just-In-Time Production
Just-in-time (JIT) is a method that is used to reduce costs and maximize efficiency in business processes. It allows you to get the right amount resources at the right time. This means that your only pay for the resources you actually use. Frederick Taylor was the first to coin this term. He developed it while working as a foreman during the early 1900s. He observed how workers were paid overtime if there were delays in their work. He concluded that if workers were given enough time before they start work, productivity would increase.
JIT teaches you to plan ahead and prepare everything so you don’t waste time. Look at your entire project, from start to end. Make sure you have enough resources in place to deal with any unexpected problems. You can anticipate problems and have enough equipment and people available to fix them. This way you won't be spending more on things that aren’t really needed.
There are many types of JIT methods.
-
Demand-driven JIT: This is a JIT that allows you to regularly order the parts/materials necessary for your project. This will allow for you to track the material that you have left after using it. This will allow to you estimate the time it will take for more to be produced.
-
Inventory-based : You can stock the materials you need in advance. This allows you to forecast how much you will sell.
-
Project-driven: This means that you have enough money to pay for your project. Once you have an idea of how much material you will need, you can purchase the necessary materials.
-
Resource-based JIT: This type of JIT is most commonly used. Here you can allocate certain resources based purely on demand. You will, for example, assign more staff to deal with large orders. If you don't receive many orders, then you'll assign fewer employees to handle the load.
-
Cost-based : This is similar in concept to resource-based. But here, you aren't concerned about how many people your company has but how much each individual costs.
-
Price-based: This is a variant of cost-based. However, instead of focusing on the individual workers' costs, this looks at the total price of the company.
-
Material-based is an alternative to cost-based. Instead of looking at the total cost in the company, this method focuses on the average amount of raw materials that you consume.
-
Time-based: This is another variation of resource-based JIT. Instead of focusing only on how much each employee is costing, you should focus on how long it takes to complete your project.
-
Quality-based JIT: This is another variation of resource based JIT. Instead of thinking about the cost of each employee or the time it takes to produce something, you focus on how good your product quality.
-
Value-based JIT is the newest form of JIT. In this scenario, you're not concerned about how products perform or whether customers expect them to meet their expectations. Instead, your goal is to add value to the market.
-
Stock-based: This stock-based method focuses on the actual quantity of products being made at any given time. It's used when you want to maximize production while minimizing inventory.
-
Just-intime planning (JIT), is a combination JIT/sales chain management. It is the process of scheduling components' delivery as soon as they have been ordered. It reduces lead times and improves throughput.