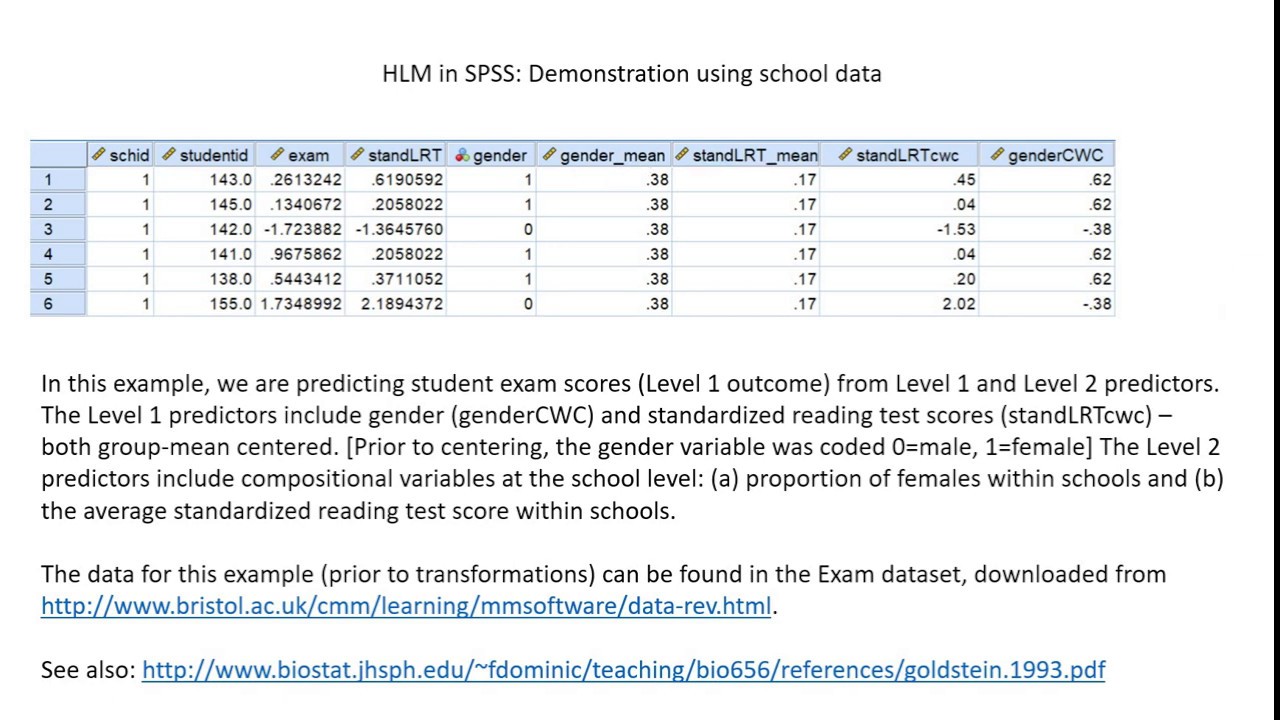
A variety of factors can cause supply chain disruptions. Some examples include natural disasters, product recalls, and transportation delays. These disruptions can cause margin shrinking and price increases. To continue production, some companies may need a change in their sourcing strategies. In many cases, companies will need to re-evaluate their supply networks, diversify their production, and audit their current inventories to prepare for the next disruption.
Many industries have experienced disruptions in their supply chains, including transportation, electronics, as well as pharmaceuticals. Sometimes the disruptions were caused by an internal problem at a company. In other cases, they were due to global events. A pandemic in one example caused widespread disruptions to the health systems of several countries. It also had an impact on the retail industry. It forced governments to implement policies to stop the spread.
Pandemics can have a devastating effect on a company's workforce and distribution systems, as well as their manufacturing processes. This can affect the production of essential products, which means companies will need to re-evaluate and adjust their production and supply chains. Depending on the severity of the disruption, the impact can range from a few weeks to months. Businesses will need time to assess their inventory and reallocate capital in case of a pandemic.
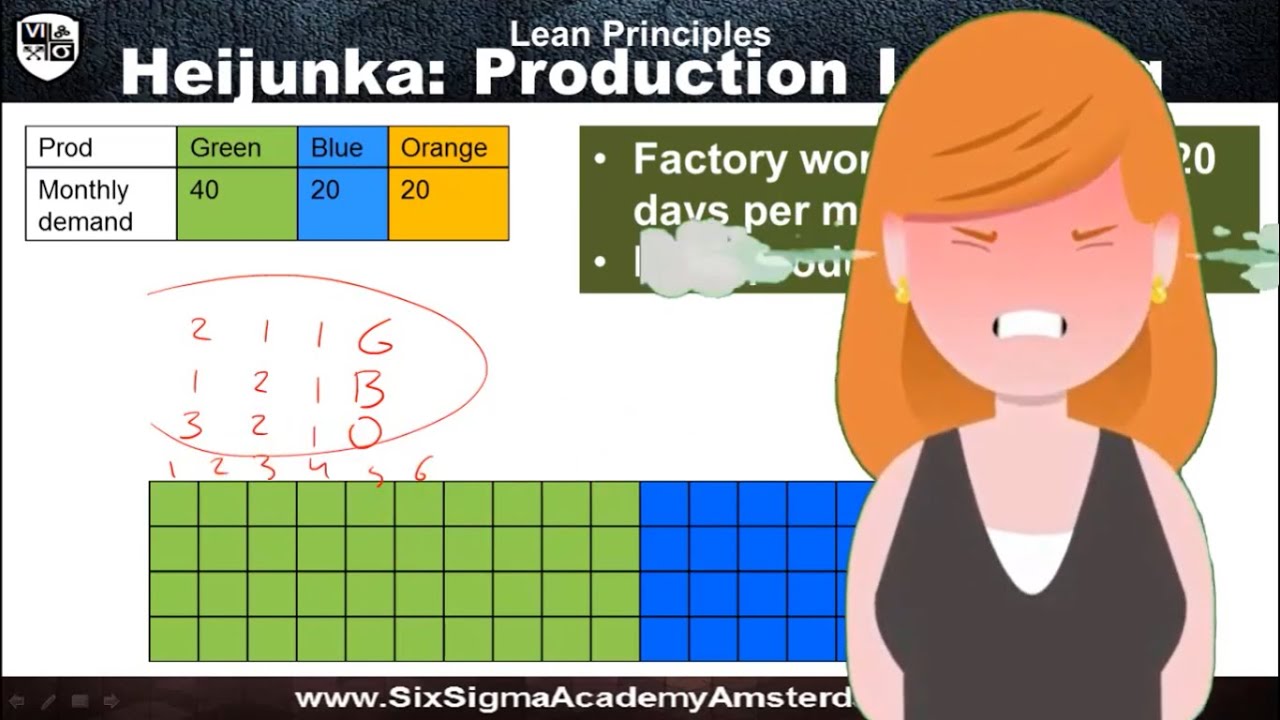
Any stage of the supply chain can be disrupted, and it can affect both supply and demand. Most often, disruptions will affect the supply side more than the demand side. However, if a pandemic strikes the supply side, it will ripple throughout the economy.
Supply chain disruptions can have a major impact on a business and are often difficult to predict. While it is easy to identify seasonal fluctuations, it is more challenging to predict a rapid shift in consumer behavior. A predictive analytics tool is a great way to avoid these problems.
A labor shortage is another common reason for supply chain disruption. Businesses can lose productivity when they cannot obtain parts and equipment from reliable suppliers. Machine failures can also cause chaos in an operation.
Natural disasters, market fluctuations and geopolitical instability are some of the most common reasons for supply chain disruptions. Natural disasters are costly and have the potential to disrupt the global supply network. A power outage, telecommunications disruption, or border closures are all possible causes of supply chain disruption. Companies may have to store large quantities of stock in order to protect their businesses.
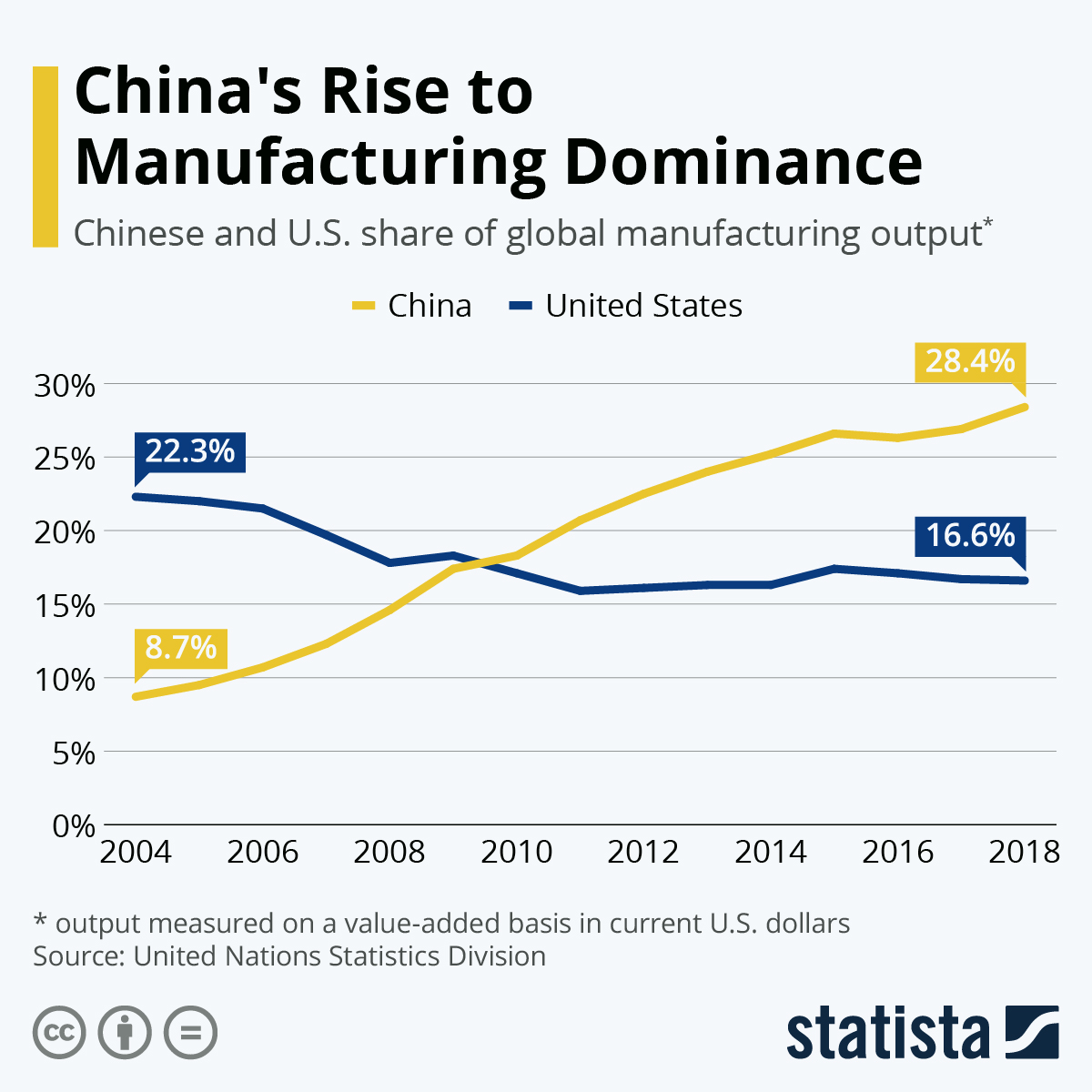
As a rule of thumb, the impact of supply chain disruptions is relatively low. Companies will need take action if they spot a disruption. The majority of companies will need to do so within a reasonable timeframe. Early detection can reduce the likelihood of conflict.
Ernest & Young LLP surveyed 72% of respondents to a survey and found that 79% had experienced disruptions at some time. 57% reported negative effects. Some of these issues can easily be solved quickly, while others require a more strategic approach.
FAQ
What are the 7 Rs of logistics?
The acronym 7R's for Logistics stands to represent the seven basic principles in logistics management. It was developed by the International Association of Business Logisticians (IABL) and published in 2004 as part of its "Seven Principles of Logistics Management" series.
The acronym consists of the following letters:
-
Responsible - ensure that actions are in compliance with legal requirements and do not cause harm to others.
-
Reliable – have faith in your ability and capability to keep promises.
-
Reasonable - use resources efficiently and don't waste them.
-
Realistic - Consider all aspects of operations, including environmental impact and cost effectiveness.
-
Respectful - Treat people fairly and equitably
-
Reliable - Find ways to save money and increase your productivity.
-
Recognizable - provide customers with value-added services.
What is the best way to learn about manufacturing?
You can learn the most about manufacturing by getting involved in it. You can read books, or watch instructional videos if you don't have the opportunity to do so.
Why is logistics so important in manufacturing?
Logistics are an integral part any business. They help you achieve great results by helping you manage all aspects of product flow, from raw materials to finished goods.
Logistics play an important role in reducing costs as well as increasing efficiency.
What does it take for a logistics enterprise to succeed?
To be a successful businessman in logistics, you will need many skills and knowledge. You must have good communication skills to interact effectively with your clients and suppliers. You need to understand how to analyze data and draw conclusions from it. You must be able to work well under pressure and handle stressful situations. You must be creative and innovative to develop new ideas to improve efficiency. To motivate and guide your team towards reaching organizational goals, you must have strong leadership skills.
You should also be organized and efficient to meet tight deadlines.
Statistics
- In 2021, an estimated 12.1 million Americans work in the manufacturing sector.6 (investopedia.com)
- According to the United Nations Industrial Development Organization (UNIDO), China is the top manufacturer worldwide by 2019 output, producing 28.7% of the total global manufacturing output, followed by the United States, Japan, Germany, and India.[52][53] (en.wikipedia.org)
- You can multiply the result by 100 to get the total percent of monthly overhead. (investopedia.com)
- Many factories witnessed a 30% increase in output due to the shift to electric motors. (en.wikipedia.org)
- (2:04) MTO is a production technique wherein products are customized according to customer specifications, and production only starts after an order is received. (oracle.com)
External Links
How To
How to Use Lean Manufacturing in the Production of Goods
Lean manufacturing (or lean manufacturing) is a style of management that aims to increase efficiency, reduce waste and improve performance through continuous improvement. It was developed in Japan during the 1970s and 1980s by Taiichi Ohno, who received the Toyota Production System (TPS) award from TPS founder Kanji Toyoda. Michael L. Watkins published the "The Machine That Changed the World", the first book about lean manufacturing. It was published in 1990.
Lean manufacturing is often described as a set if principles that help improve the quality and speed of products and services. It is about eliminating defects and waste from all stages of the value stream. Lean manufacturing is also known as just in time (JIT), zero defect total productive maintenance(TPM), and five-star (S). Lean manufacturing focuses on eliminating non-value-added activities such as rework, inspection, and waiting.
Lean manufacturing not only improves product quality but also reduces costs. Companies can also achieve their goals faster by reducing employee turnover. Lean manufacturing can be used to manage all aspects of the value chain. Customers, suppliers, distributors, retailers and employees are all included. Lean manufacturing is widely practiced in many industries around the world. Toyota's philosophy, for example, is what has enabled it to be successful in electronics, automobiles, medical devices, healthcare and chemical engineering as well as paper and food.
Lean manufacturing is based on five principles:
-
Define Value- Identify the added value your company brings to society. What makes you stand out from your competitors?
-
Reduce Waste – Eliminate all activities that don't add value throughout the supply chain.
-
Create Flow. Ensure that your work is uninterrupted and flows seamlessly.
-
Standardize and simplify - Make your processes as consistent as possible.
-
Building Relationships – Establish personal relationships with both external and internal stakeholders.
Lean manufacturing is not a new concept, but it has been gaining popularity over the last few years due to a renewed interest in the economy following the global financial crisis of 2008. To increase their competitiveness, many businesses have turned to lean manufacturing. In fact, some economists believe that lean manufacturing will be an important factor in economic recovery.
Lean manufacturing is becoming a popular practice in automotive. It has many advantages. These include higher customer satisfaction, lower inventory levels, lower operating expenses, greater productivity, and improved overall safety.
Lean manufacturing can be applied to almost every aspect of an organization. This is because it ensures efficiency and effectiveness in all stages of the value chain.
There are three main types:
-
Just-in Time Manufacturing, (JIT): This kind of lean manufacturing is also commonly known as "pull-systems." JIT refers to a system in which components are assembled at the point of use instead of being produced ahead of time. This strategy aims to decrease lead times, increase availability of parts and reduce inventory.
-
Zero Defects Manufacturing (ZDM): ZDM focuses on ensuring that no defective units leave the manufacturing facility. You should repair any part that needs to be repaired during an assembly line. This is also true for finished products that require minor repairs before shipping.
-
Continuous Improvement: Continuous Improvement aims to improve efficiency by continually identifying problems and making adjustments to eliminate or minimize waste. It involves continuous improvement of processes, people, and tools.