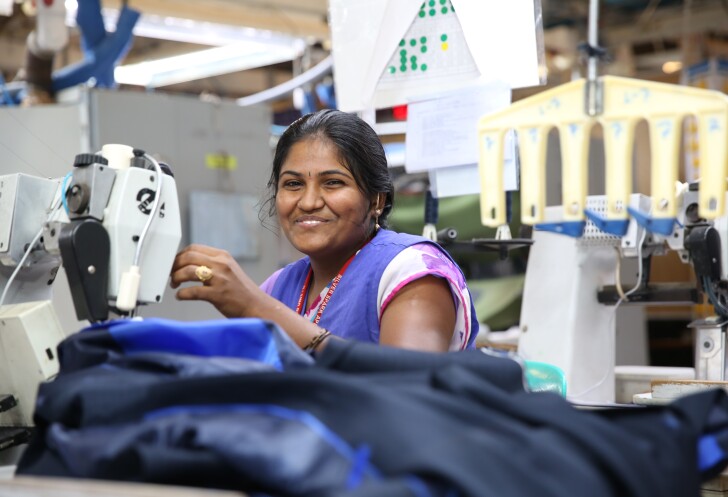
Whether you're looking for a job or interested in pursuing a degree in industrial engineering, you should know how much you can expect to earn. The salary for industrial engineers varies depending on the type of degree you earn, your industry, and your experience. An industrial engineer average salary is approximately $95,300. The salaries of industrial engineers are usually higher in the highest paid metropolitan areas.
Industrial engineers are responsible for designing, developing and installing systems that increase the productivity of the production process. They also develop ways to keep workplaces safer. Industrial engineers may also design equipment, plan facilities and analyze the specifications of products. This can be done by evaluating how changes in design affect the costs of producing the product.
An industrial engineer can earn a very high salary if he or she has experience. If they hold a master's in industrial engineering, they can earn a higher salary. This degree is highly sought-after by international students. It can lead to a career within manufacturing, engineering services, and healthcare.
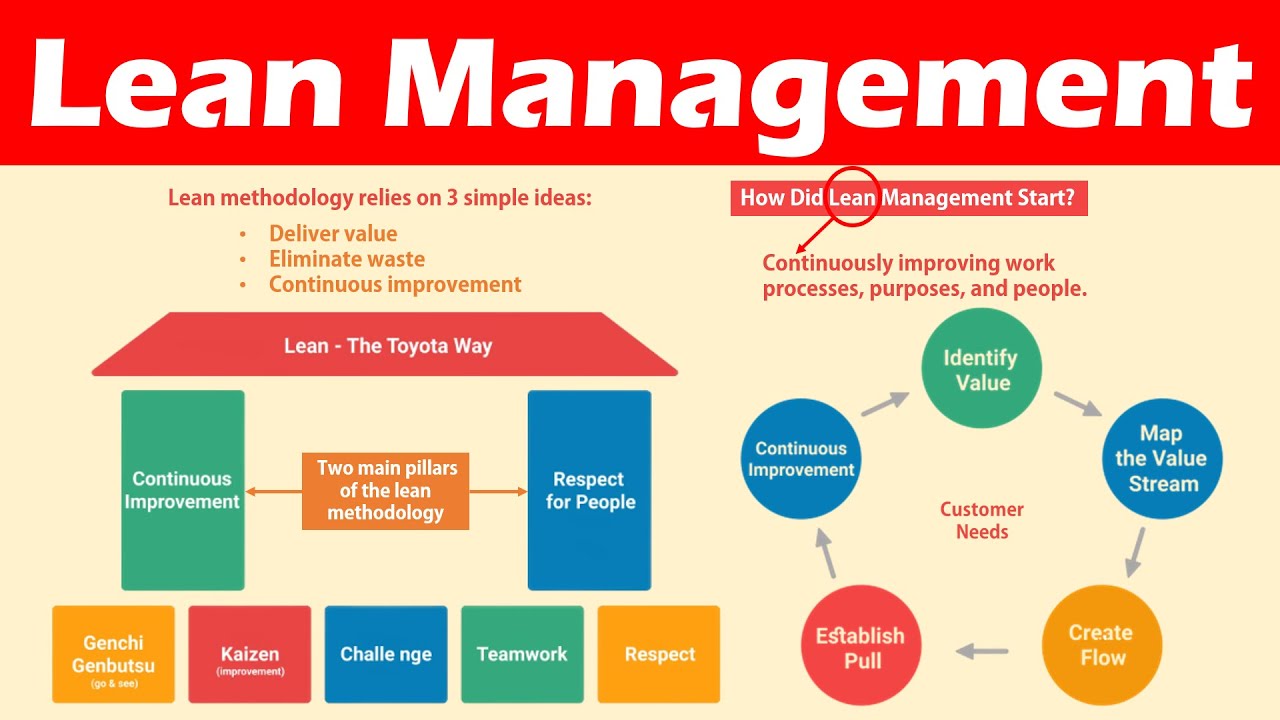
The next decade will see a rapid increase in the number of industrial engineers. Employment of industrial engineers is projected to grow 10 percent from 2021 to 2031. This is more than the average for all occupations. The top 10% of industrial engineering professionals earn more that $85,000 a year. If they have managerial experience, they can expect to make more. Industrial engineers with advanced degrees do cost-benefit assessments, look at cost distribution in operating processes, and negotiate purchasing decisions.
Industrial engineers have the ability to think outside of the box and find creative ways to make processes more efficient. Many industrial engineers work in offices. They may also interact with production workers. Industrial engineers can also handle telephone calls, emails and face-to–face conversations. They can also present their plans orally or in written reports.
A variety of industries are where industrial engineers can find work, including construction, pharmaceuticals manufacturing, transportation energy, energy, and utilities. Depending on which industry they work for, they might develop systems to reduce production waste.
An industrial engineer typically needs a bachelor's in engineering. A master's degree can be obtained in industrial engineering for a career as an engineer consultant or manufacturer. Many programs provide courses in general engineering, mathematics, science and general engineering. The program can take two to seven years to complete.
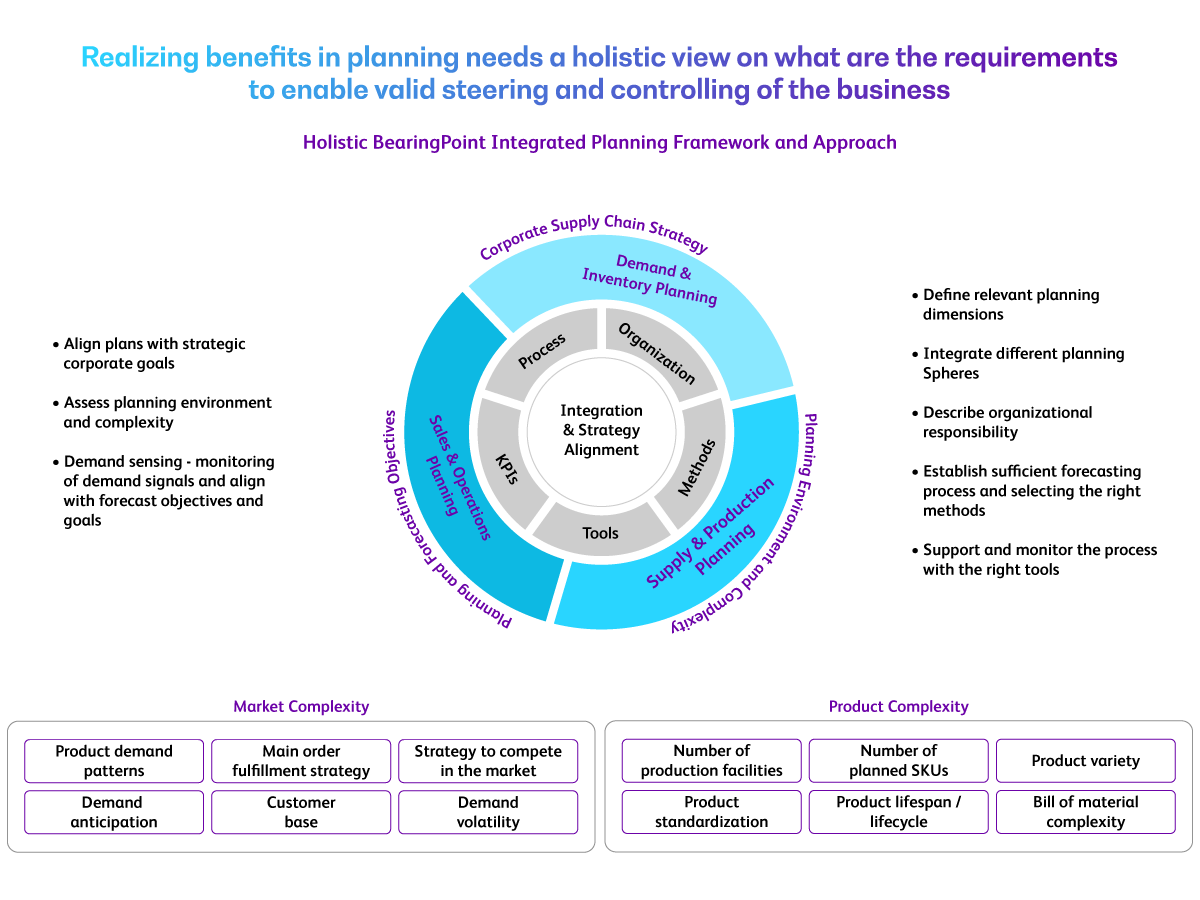
An entry-level industrial engineer's salary range is $65,000 to $75,000. However, the range increases as you get more experience. The salary for an experienced industrial engineer is $86,809 a year. If an industrial engineer has a master's in engineering or doctorate, their salary may be higher.
Good communication skills are essential for industrial engineers. They also need technical knowledge. They need to be able to think outside the box to solve problems. They should know how to connect workers, equipment, and materials to create efficient system. They must have strong interpersonal skills. The job is challenging and can be rewarding.
FAQ
Why is logistics important in manufacturing
Logistics are an integral part any business. They help you achieve great results by helping you manage all aspects of product flow, from raw materials to finished goods.
Logistics play an important role in reducing costs as well as increasing efficiency.
Is automation important in manufacturing?
Automating is not just important for manufacturers, but also for service providers. Automation allows them to deliver services quicker and more efficiently. It reduces human errors and improves productivity, which in turn helps them lower their costs.
How can overproduction in manufacturing be reduced?
Improved inventory management is the key to reducing overproduction. This would decrease the time that is spent on inefficient activities like purchasing, storing, or maintaining excess stock. This will allow us to free up resources for more productive tasks.
A Kanban system is one way to achieve this. A Kanban board is a visual display used to track work in progress. In a Kanban system, work items move through a sequence of states until they reach their final destination. Each state represents an individual priority level.
If work is moving from one stage to the other, then the current task can be completed and moved on to the next. If a task is still in its beginning stages, it will continue to be so until it reaches the end.
This helps to keep work moving forward while ensuring that no work is left behind. Managers can view the Kanban board to see how much work they have done. This information allows managers to adjust their workflow based off real-time data.
Lean manufacturing can also be used to reduce inventory levels. Lean manufacturing emphasizes eliminating waste in all phases of production. Anything that does nothing to add value to a product is waste. The following are examples of common waste types:
-
Overproduction
-
Inventory
-
Unnecessary packaging
-
Exceed materials
These ideas can help manufacturers improve efficiency and reduce costs.
What is production planning?
Production Planning includes planning for all aspects related to production. It is important to have everything ready and planned before you start shooting. It should also contain information on achieving the best results on set. This includes location information, crew details, equipment specifications, and casting lists.
The first step is to outline what you want to film. You may have decided where to shoot or even specific locations you want to use. Once you have identified your locations and scenes, you can start working out which elements you require for each scene. For example, you might decide that you need a car but don't know exactly what model you want. To narrow your options, you can search online for available models.
After you have chosen the right car, you will be able to begin thinking about accessories. Do you need people sitting in the front seats? Maybe you need someone to move around in the back. Maybe you'd like to change the interior from black to a white color. These questions will help to determine the style and feel of your car. You can also think about the type of shots you want to get. You will be filming close-ups and wide angles. Maybe the engine or steering wheel is what you are looking to film. This will allow you to determine the type of car you want.
Once you have made all the necessary decisions, you can start to create a schedule. A schedule will tell you when you need to start shooting and when you need to finish. A schedule for each day will detail when you should arrive at the location and when you need leave. This way, everyone knows what they need to do and when. You can also make sure to book extra staff in advance if you have to hire them. You don't want to hire someone who won't show up because he didn't know.
When creating your schedule, you will also need to consider the number of days you need to film. Some projects can be completed in a matter of days or weeks. Others may take several days. You should consider whether you will need more than one shot per week when creating your schedule. Shooting multiple takes over the same location will increase costs and take longer to complete. You can't be certain if you will need multiple takes so it is better not to shoot too many.
Another important aspect of production planning is setting budgets. It is important to set a realistic budget so you can work within your budget. Remember that you can always reduce the budget later on if you run into unforeseen problems. But, don't underestimate how much money you'll spend. If you underestimate the cost of something, you will have less money left after paying for other items.
Planning production is a tedious process. Once you have a good understanding of how everything works together, planning future projects becomes easy.
What skills does a production planner need?
You must be flexible and organized to become a productive production planner. It is also important to be able communicate with colleagues and clients.
How can manufacturing efficiency be improved?
First, we need to identify which factors are most critical in affecting production times. We then need to figure out how to improve these variables. If you aren't sure where to begin, think about the factors that have the greatest impact on production time. Once you've identified them all, find solutions to each one.
Is it possible to automate certain parts of manufacturing
Yes! Yes. The Egyptians created the wheel thousands years ago. Today, robots assist in the assembly of lines.
In fact, there are several applications of robotics in manufacturing today. These include:
-
Automation line robots
-
Robot welding
-
Robot painting
-
Robotics inspection
-
Robots create products
Automation could also be used to improve manufacturing. 3D printing is a way to make custom products quickly and without waiting weeks or months for them to be manufactured.
Statistics
- According to a Statista study, U.S. businesses spent $1.63 trillion on logistics in 2019, moving goods from origin to end user through various supply chain network segments. (netsuite.com)
- It's estimated that 10.8% of the U.S. GDP in 2020 was contributed to manufacturing. (investopedia.com)
- (2:04) MTO is a production technique wherein products are customized according to customer specifications, and production only starts after an order is received. (oracle.com)
- Many factories witnessed a 30% increase in output due to the shift to electric motors. (en.wikipedia.org)
- In 2021, an estimated 12.1 million Americans work in the manufacturing sector.6 (investopedia.com)
External Links
How To
Six Sigma in Manufacturing
Six Sigma is "the application statistical process control (SPC), techniques for continuous improvement." Motorola's Quality Improvement Department in Tokyo, Japan developed Six Sigma in 1986. Six Sigma's main goal is to improve process quality by standardizing processes and eliminating defects. This method has been adopted by many companies in recent years as they believe there are no perfect products or services. Six Sigma's primary goal is to reduce variation from the average value of production. You can calculate the percentage of deviation from the norm by taking a sample of your product and comparing it to the average. If there is a significant deviation from the norm, you will know that something needs to change.
The first step toward implementing Six Sigma is understanding how variability works in your business. Once you understand this, you can then identify the causes of variation. Also, you will need to identify the sources of variation. Random variations occur when people make mistakes; systematic ones are caused by factors outside the process itself. Random variations would include, for example, the failure of some widgets to fall from the assembly line. If however, you notice that each time you assemble a widget it falls apart in exactly the same spot, that is a problem.
Once you have identified the problem, you can design solutions. It might mean changing the way you do business or redesigning it entirely. After implementing the new changes, you should test them again to see if they worked. If they fail, you can go back to the drawing board to come up with a different plan.