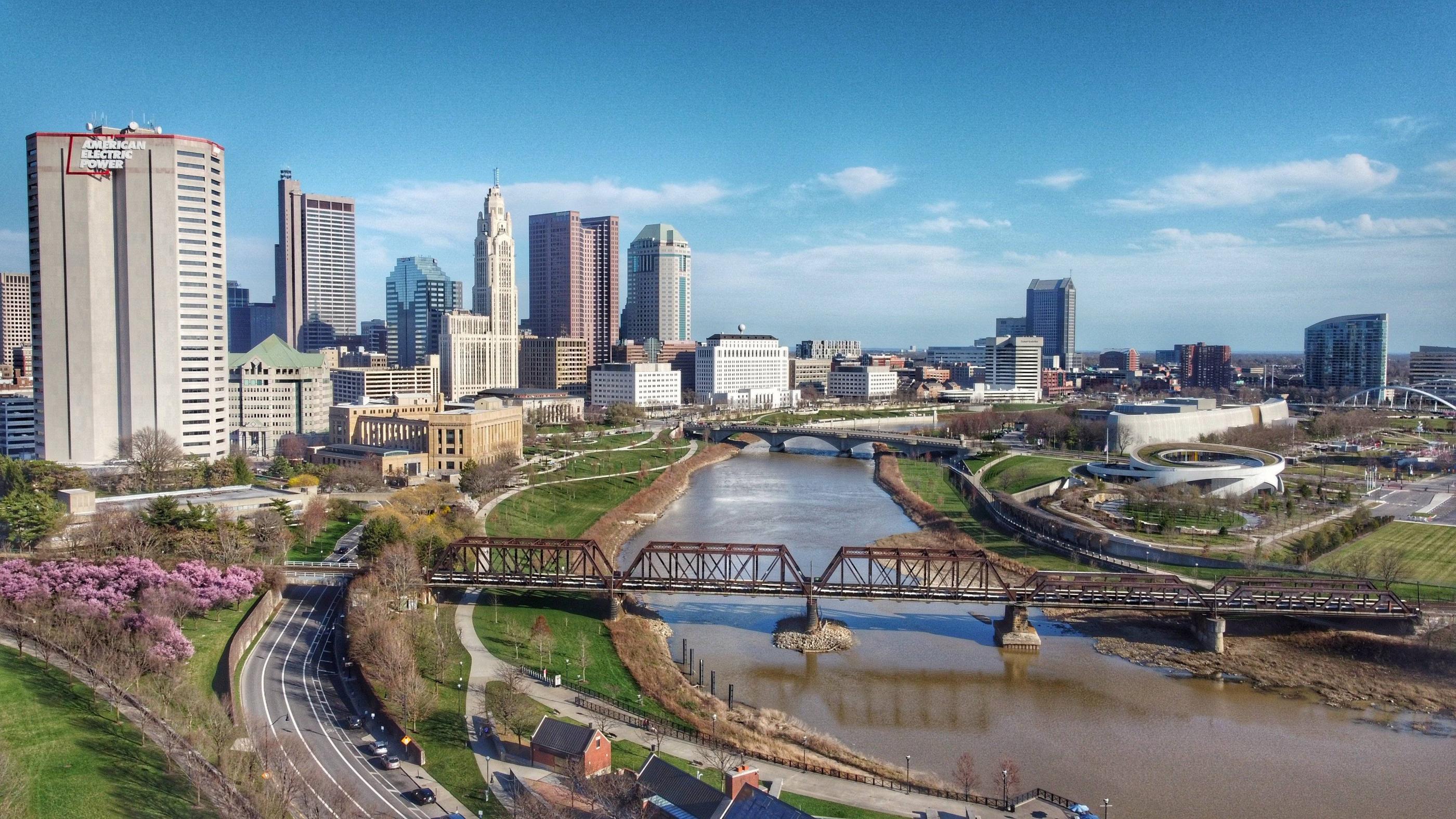
The best books about lean manufacturing are easy to read and communicate in simple language. This is essential information for industry managers. This bestselling book covers many concepts, including how to improve business processes and reduce costs while improving quality. Implementation is simple thanks to the detailed drawings and step by step instructions. The book also includes information about the many different tools available for lean manufacturing.
It also gives an overview of Toyota's production system and its global success. It also discusses Toyota's management style, motivation, and problem-solving skills. It also provides information about the success of Toyota's Lean strategy and explains the 14 management principles that form the foundation of Toyota's business practices. The book also contains a chapter about the automotive industry that includes a section on Toyota's use of lean principles in this sector.
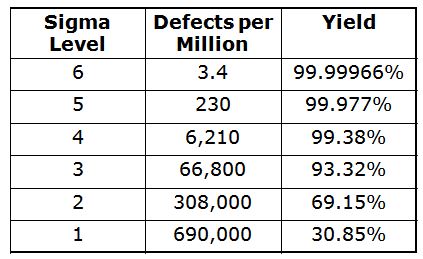
Lean manufacturing refers to a manufacturing process that improves the quality of products and services. It aims to eliminate waste, making the process more efficient and error-free. The most successful manufacturing processes involve the interactions of highly skilled people and machines. These interactions are the main reason for a company's high-quality manufacturing processes.
The best books on lean manufacturing include the Lean Manufacturing Tool Book, The Toyota Way: 14 Management Principles for Improving Quality and Productivity, and The Machine that Changed the World: How Toyota Built a Competitive Advantage. These books offer a thorough explanation of Toyota's manufacturing system as well as practical tips, and detailed instructions for how to apply Lean techniques to any type of manufacturing environment. The Lean Manufacturing Tool Book provides a comprehensive guide to all the tools that are used in Lean manufacturing. The book lists all the tools that are available and offers expert advice on how to choose the best tool. The book also explains Lean manufacturing concepts like Six Sigma and Lean Problem Solving.
The Toyota Way is one of the first books to introduce Lean manufacturing. It is a guide to Toyota's management principles. You will also learn how to implement these principles within your own company. It includes profiles of organizations and philosophies that are the basis for Toyota's success. A new afterword discusses Lean's impact on the manufacturing sector since the book was published. It provides new frameworks to improve quality and reduce costs, as well as updated production processes.
The Machine that Changed the World - How Lean Changed the World - This book was the first to fully explain the Toyota Production System, and the impact it had on the manufacturing industry. This book was published in 1990. It provides an overview and context of the system. This book contains a new afterword, and a revised foreword. They provide an improved understanding of the Toyota Production System's impact on the global manufacturing sector. It also explains what the fundamental ideas are that underpin Lean today.
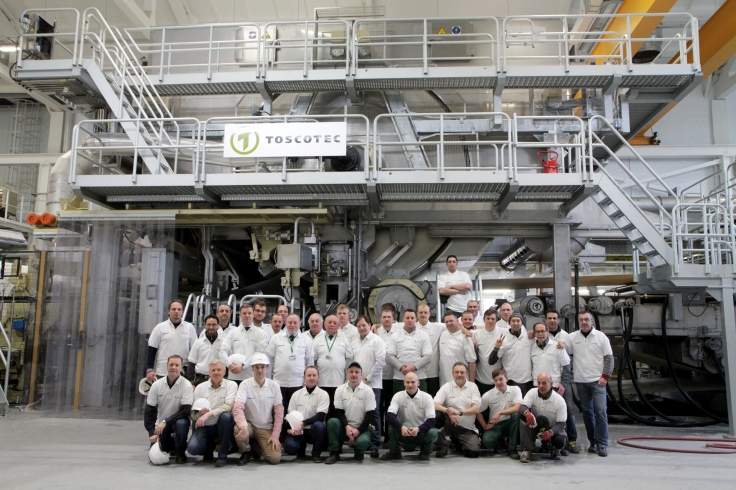
The Toyota Kata: Flow-Focused Manufacturing Methodology is another important book. It explains how Toyota works together with their customers to offer quality products. It explains how Toyota is committed to quality, problem-solving and speeding up business processes. It also explains Toyota's process for selecting and hiring employees and their motivation to deliver high quality products.
FAQ
What does warehouse mean?
A warehouse is a place where goods are stored until they are sold. It can be an indoor space or an outdoor area. Sometimes, it can be both an indoor and outdoor space.
What are my options for learning more about manufacturing
The best way to learn about manufacturing is through hands-on experience. You can also read educational videos or take classes if this isn't possible.
What is the job of a manufacturer manager?
A manufacturing manager has to ensure that all manufacturing processes work efficiently and effectively. They should be aware of any issues within the company and respond accordingly.
They should also be able and comfortable communicating with other departments like sales and marketing.
They should be up to date on the latest trends and be able apply this knowledge to increase productivity and efficiency.
Statistics
- Many factories witnessed a 30% increase in output due to the shift to electric motors. (en.wikipedia.org)
- According to the United Nations Industrial Development Organization (UNIDO), China is the top manufacturer worldwide by 2019 output, producing 28.7% of the total global manufacturing output, followed by the United States, Japan, Germany, and India.[52][53] (en.wikipedia.org)
- You can multiply the result by 100 to get the total percent of monthly overhead. (investopedia.com)
- In the United States, for example, manufacturing makes up 15% of the economic output. (twi-global.com)
- Job #1 is delivering the ordered product according to specifications: color, size, brand, and quantity. (netsuite.com)
External Links
How To
How to use 5S to increase Productivity in Manufacturing
5S stands as "Sort", Set In Order", Standardize", Separate" and "Store". Toyota Motor Corporation invented the 5S strategy in 1954. It improves the work environment and helps companies to achieve greater efficiency.
The idea behind standardizing production processes is to make them repeatable and measurable. This means that every day tasks such cleaning, sorting/storing, packing, and labeling can be performed. This knowledge allows workers to be more efficient in their work because they are aware of what to expect.
There are five steps that you need to follow in order to implement 5S. Each step requires a different action to increase efficiency. By sorting, for example, you make it easy to find the items later. When items are ordered, they are put together. Then, after you separate your inventory into groups, you store those groups in containers that are easy to access. Make sure everything is correctly labeled when you label your containers.
This process requires employees to think critically about how they do their job. Employees must be able to see why they do what they do and find a way to achieve them without having to rely on their old methods. They must learn new skills and techniques in order to implement the 5S system.
The 5S Method not only improves efficiency, but it also helps employees to be more productive and happier. Once they start to notice improvements, they are motivated to keep working towards their goal of increasing efficiency.