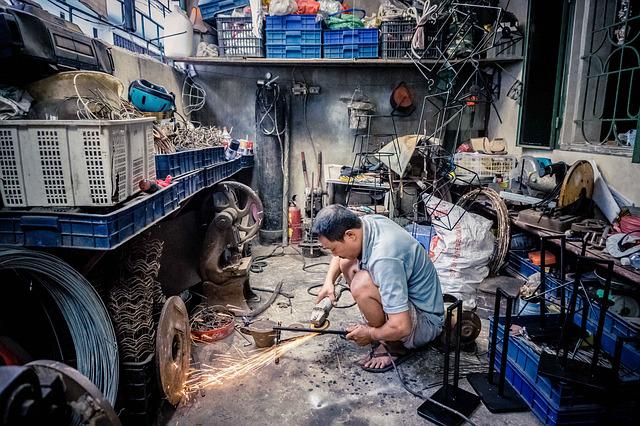
During the industrial revolution, manufacturing engineers have been in demand. They are responsible in designing manufacturing processes that increase productivity. Manufacturing engineers have to be able to think commercially in addition to their technical skills. They must also have a strong foundation in science and math. Additionally, they must have leadership abilities.
Their education, skills, experience, as well as their salary, will all affect the wage of a manufacturing engineer. In the United States, they can earn between $70,960 and $126,000 per year. A master's degree is available for those who are keen to further their careers. A master's degree can help them earn a better income. A master's can allow them to learn new technologies, and improve their skills.
A PhD is also possible to make a contribution as a researcher. They may also work for the local and central government. They could also work as consultants. They could work in different areas.
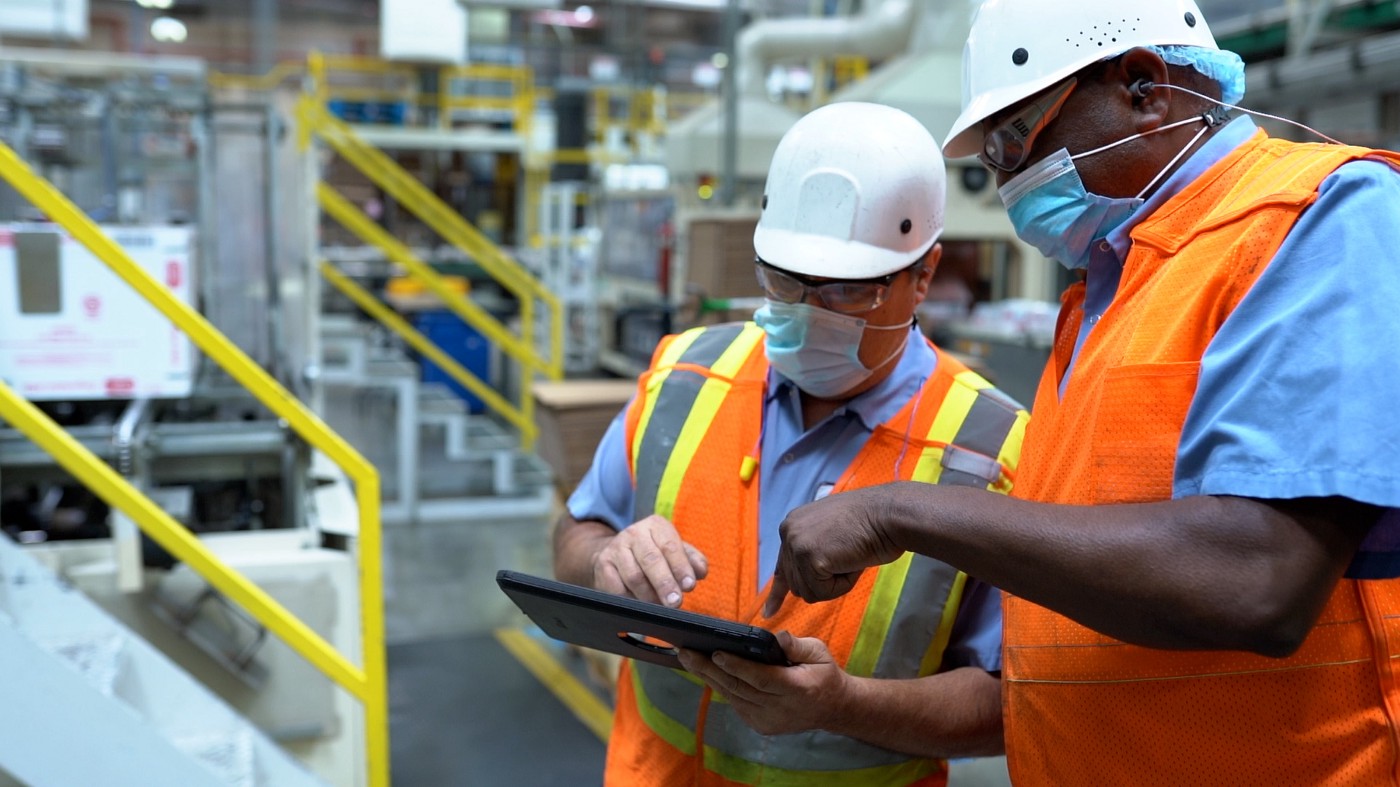
Manufacturing engineers are paid a higher salary if they have more experience. As they gain experience they will be able move up to managerial positions. This position allows them to design and implement manufacturing processes. They will also oversee the daily operations of the factory. They might be required to work evenings and weekends.
Many manufacturing engineers begin as interns or apprentices. They can work in a variety of fields, including food manufacturing, aerospace engineering or pharmaceutical manufacturing. They are also able to work in commercial or industrial design. After a few years, they may be eligible to become consultants. They will have the ability to oversee the factory floor, as well as assist engineers. They will also be responsible maintaining company best practices. They will also need to find and correct any manufacturing mistakes.
Manufacturing engineers need to be up-to-date with the latest manufacturing trends. They need to be able work in a fast-paced environment, and solve any problems that might arise. They should also be able to lead and use IT skills. During their first few years in the industry, they will earn a standard salary. They may be able to earn slightly more after that.
Typically, manufacturing engineers can earn a salary of $28,500 to $126,000 per year. This salary range includes bonuses, taxable wages, and other benefits. The state where the job is situated can affect the salary. In some states, Manufacturing Engineers can earn up to $34 per hour.
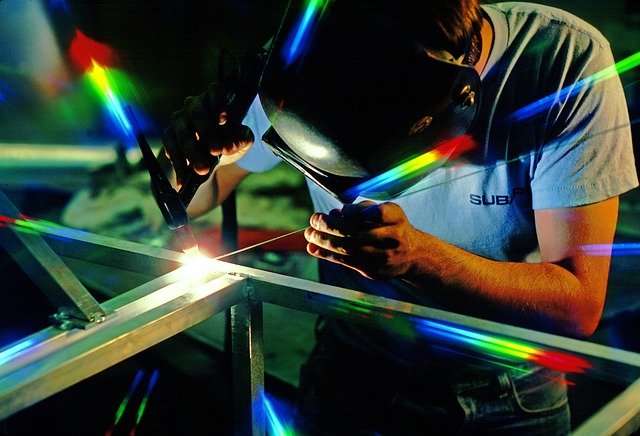
A manufacturing engineer can work for many different manufacturing industries, including aerospace, food manufacturing, pharmaceutical manufacturing, and paper manufacturing. They can either work for multinational companies or smaller local operations. They can also work in central or local government.
They are also eligible to work in new industrial areas. General Motors, Tesla, and Boeing are just a few of the top American manufacturing companies. A graduate degree can also help an engineer learn more about new technologies.
FAQ
What is manufacturing and logistics?
Manufacturing refers the process of producing goods from raw materials through machines and processes. Logistics covers all aspects involved in managing supply chains, including procurement and production planning. As a broad term, manufacturing and logistics often refer to both the creation and delivery of products.
What skills is required for a production planner?
To become a successful production planner, you need to be organized, flexible, and able to multitask. You must also be able to communicate effectively with clients and colleagues.
How can excess manufacturing production be reduced?
In order to reduce excess production, you need to develop better inventory management methods. This would reduce the time needed to manage inventory. This will allow us to free up resources for more productive tasks.
You can do this by adopting a Kanban method. A Kanban board can be used to monitor work progress. A Kanban system allows work items to move through several states before reaching their final destination. Each state represents an individual priority level.
When work is completed, it can be transferred to the next stage. But if a task remains in the beginning stages it will stay that way until it reaches its end.
This allows work to move forward and ensures that no work is missed. Managers can view the Kanban board to see how much work they have done. This information allows managers to adjust their workflow based off real-time data.
Lean manufacturing is another option to control inventory levels. Lean manufacturing works to eliminate waste throughout every stage of the production chain. Any product that isn't adding value can be considered waste. There are several types of waste that you might encounter:
-
Overproduction
-
Inventory
-
Unnecessary packaging
-
Materials in excess
These ideas will help manufacturers increase efficiency and lower costs.
Statistics
- You can multiply the result by 100 to get the total percent of monthly overhead. (investopedia.com)
- In 2021, an estimated 12.1 million Americans work in the manufacturing sector.6 (investopedia.com)
- According to a Statista study, U.S. businesses spent $1.63 trillion on logistics in 2019, moving goods from origin to end user through various supply chain network segments. (netsuite.com)
- (2:04) MTO is a production technique wherein products are customized according to customer specifications, and production only starts after an order is received. (oracle.com)
- In the United States, for example, manufacturing makes up 15% of the economic output. (twi-global.com)
External Links
How To
How to Use lean manufacturing in the Production of Goods
Lean manufacturing is a management system that aims at increasing efficiency and reducing waste. It was developed in Japan between 1970 and 1980 by Taiichi Ohno. TPS founder Kanji Tyoda gave him the Toyota Production System, or TPS award. Michael L. Watkins published the first book on lean manufacturing in 1990.
Lean manufacturing refers to a set of principles that improve the quality, speed and costs of products and services. It emphasizes reducing defects and eliminating waste throughout the value chain. Lean manufacturing is also known as just in time (JIT), zero defect total productive maintenance(TPM), and five-star (S). Lean manufacturing seeks to eliminate non-value added activities, such as inspection, work, waiting, and rework.
Lean manufacturing improves product quality and costs. It also helps companies reach their goals quicker and decreases employee turnover. Lean manufacturing has been deemed one of the best ways to manage the entire value-chain, including customers, distributors as well retailers and employees. Lean manufacturing can be found in many industries. Toyota's philosophy is a great example of this. It has helped to create success in automobiles as well electronics, appliances and healthcare.
Lean manufacturing includes five basic principles:
-
Define Value - Identify the value your business adds to society and what makes you different from competitors.
-
Reduce Waste - Eliminate any activity that doesn't add value along the supply chain.
-
Create Flow – Ensure that work flows smoothly throughout the process.
-
Standardize & simplify - Make processes consistent and repeatable.
-
Build Relationships- Develop personal relationships with both internal as well as external stakeholders.
Lean manufacturing isn’t new, but it has seen a renewed interest since 2008 due to the global financial crisis. Many companies have adopted lean manufacturing methods to increase their marketability. Some economists even believe that lean manufacturing can be a key factor in economic recovery.
Lean manufacturing has many benefits in the automotive sector. These include better customer satisfaction and lower inventory levels. They also result in lower operating costs.
The principles of lean manufacturing can be applied in almost any area of an organization. Because it makes sure that all value chains are efficient and effectively managed, Lean Manufacturing is particularly helpful for organizations.
There are three main types:
-
Just-in Time Manufacturing (JIT), also known as "pull system": This form of lean manufacturing is often referred to simply as "pull". JIT is a method in which components are assembled right at the moment of use, rather than being manufactured ahead of time. This method reduces lead times, increases availability, and decreases inventory.
-
Zero Defects Manufacturing (ZDM),: ZDM is a system that ensures no defective units are left the manufacturing facility. You should repair any part that needs to be repaired during an assembly line. This is also true for finished products that require minor repairs before shipping.
-
Continuous Improvement: Continuous Improvement aims to improve efficiency by continually identifying problems and making adjustments to eliminate or minimize waste. Continuous Improvement (CI) involves continuous improvement in processes, people, tools, and infrastructure.