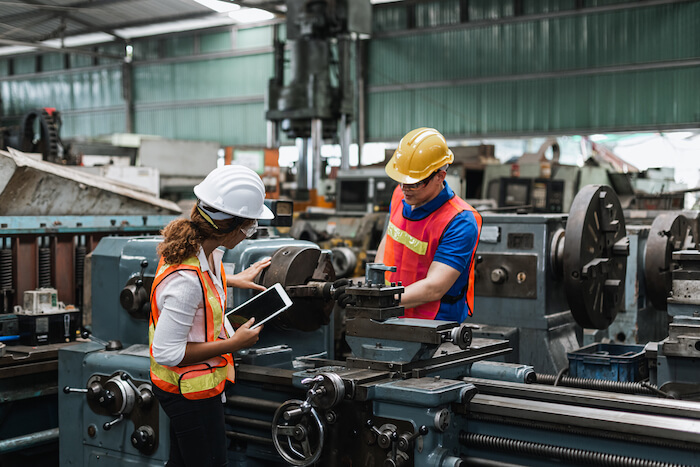
Industrial engineers are responsible for designing efficient systems that integrate people, machines, materials and information to create a product, or provide a particular service. They may work in an office or in a production setting, such as a manufacturing facility or warehouse.
Industrial Engineer Entry Level in Texas
As an industrial engineer you are responsible for the smooth running of production processes. As an industrial engineer, you will be responsible for analysing problems, troubleshooting concerns and implementing new changes to improve efficiency. You may also be responsible for training and supporting technicians who use systems and equipment that you designed.
Your duties will differ depending on your company and the needs of that particular organization. For example, some manufacturers need you to develop a process for handling hazardous waste. Some require you to design a system of monitoring and controlling raw materials.
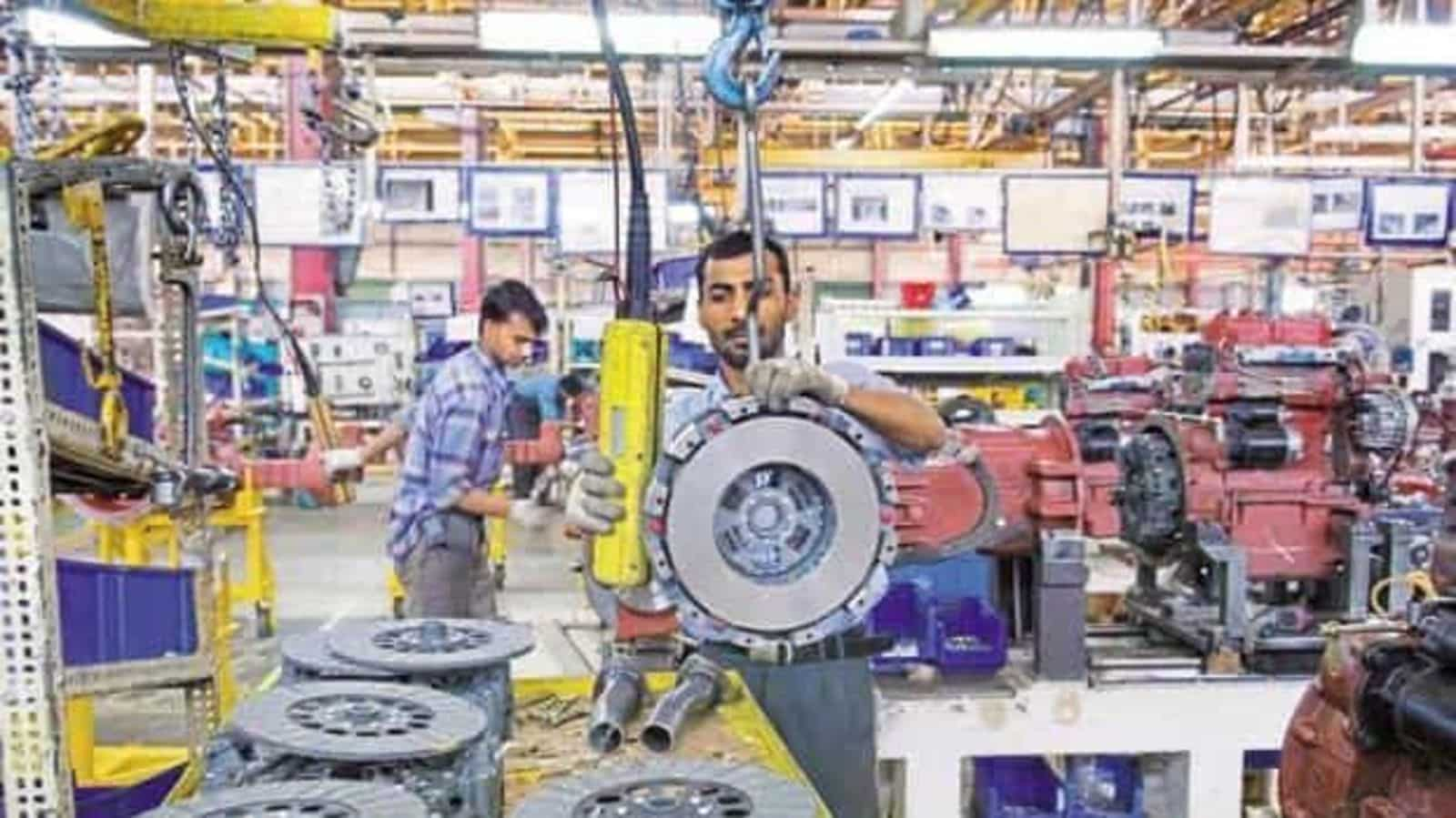
Manufacturers are always looking for ways to cut costs and increase efficiency, so you could find yourself working on projects to reduce waste in production processes. This could involve reducing the amount of inventory in a warehouse, improving the efficiency of machinery or identifying and eliminating any wasteful practices.
You could work for a manufacturer of transportation equipment, or an electronics and computer firm. These are usually full-time jobs, and employment growth is expected to be 10% in the next decade.
Manufacturing Engineering Jobs Texas
Start your career in industrial engineering by taking a job at a company that makes heavy machinery, or energy equipment. It's a great opportunity to learn more about industrial engineering. Plant managers often look for candidates who already have experience.
While working at the facility, you are expected to attend seminars and participate in training. These training opportunities are designed to help you become more productive as a member of your team. You may be required to perform research or specialized tasks that will improve your skills and knowledge as an industrial engineering.
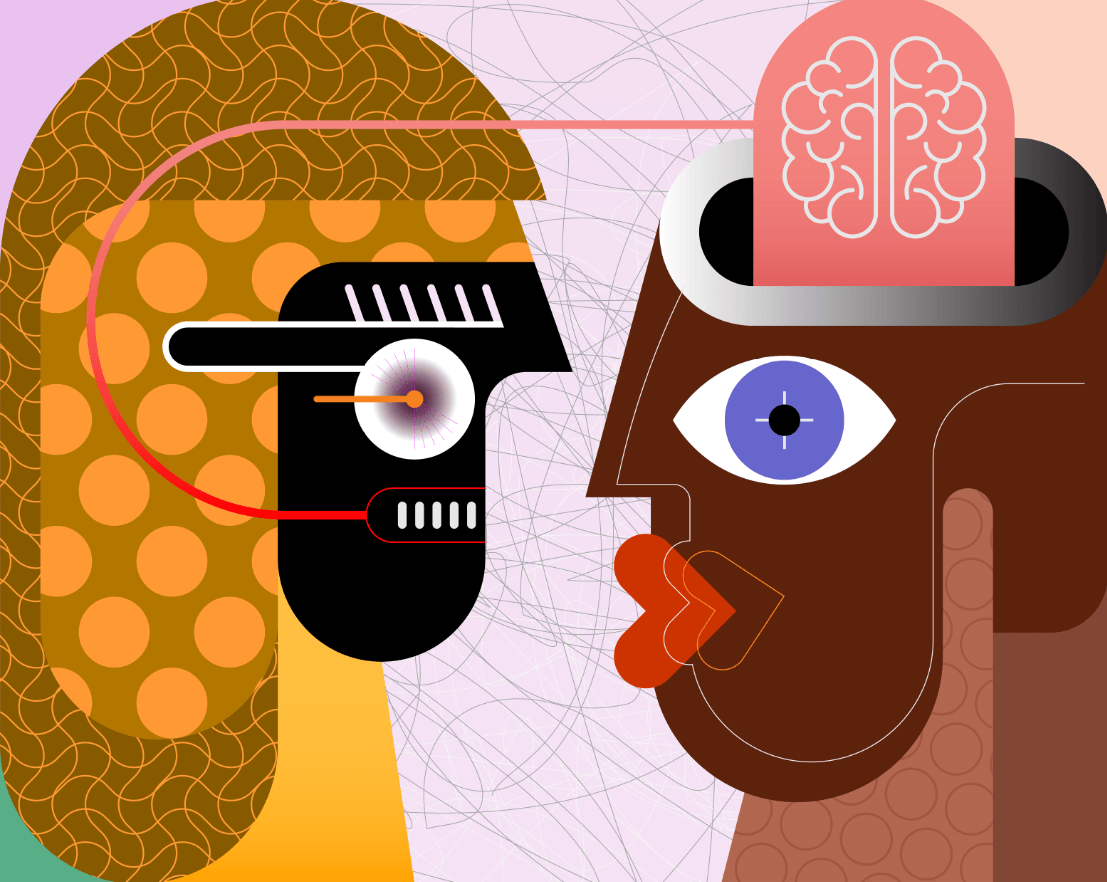
Eastman Manufacturing Engineer
If you have the right skills, Eastman Chemical could offer you a position as a industrial engineer in Mcallen. This is a rewarding and fast-paced job that gives you the chance to join a leading company in technology and energy.
As an Industrial Engineer, you are responsible for implementing the engineered standards of labor in all distribution centers. As a member of an industrial engineering team, you will be responsible for providing engineering labor standard to associates in these facilities.
FAQ
What is the role of a logistics manager
Logistics managers ensure that goods arrive on time and are unharmed. This is done by using his/her experience and knowledge of the company's products. He/she should make sure that enough stock is on hand to meet the demands.
What is the difference between Production Planning and Scheduling?
Production Planning (PP), is the process of deciding what production needs to take place at any given time. Forecasting demand is one way to do this.
Scheduling refers the process by which tasks are assigned dates so that they can all be completed within the given timeframe.
Is it necessary to be familiar with Manufacturing Processes before we learn about Logistics.
No. No. Knowing about manufacturing processes will help you understand how logistics works.
Why automate your warehouse
Modern warehouses are increasingly dependent on automation. Increased demand for efficient and faster delivery has resulted in a rise in e-commerce.
Warehouses must adapt quickly to meet changing customer needs. To do so, they must invest heavily in technology. Automating warehouses has many benefits. These are just a few reasons to invest in automation.
-
Increases throughput/productivity
-
Reduces errors
-
Accuracy is improved
-
Safety Boosts
-
Eliminates bottlenecks
-
Companies can scale up more easily
-
Increases efficiency of workers
-
The warehouse can be viewed from all angles.
-
Enhances customer experience
-
Improves employee satisfaction
-
It reduces downtime, and increases uptime
-
Quality products delivered on time
-
Eliminates human error
-
It helps ensure compliance with regulations
Statistics
- Job #1 is delivering the ordered product according to specifications: color, size, brand, and quantity. (netsuite.com)
- (2:04) MTO is a production technique wherein products are customized according to customer specifications, and production only starts after an order is received. (oracle.com)
- [54][55] These are the top 50 countries by the total value of manufacturing output in US dollars for its noted year according to World Bank.[56] (en.wikipedia.org)
- In the United States, for example, manufacturing makes up 15% of the economic output. (twi-global.com)
- You can multiply the result by 100 to get the total percent of monthly overhead. (investopedia.com)
External Links
How To
How to use 5S in Manufacturing to Increase Productivity
5S stands in for "Sort", the "Set In Order", "Standardize", or "Separate". The 5S methodology was developed at Toyota Motor Corporation in 1954. This methodology helps companies improve their work environment to increase efficiency.
This method aims to standardize production processes so that they are repeatable, measurable and predictable. This means that tasks such as cleaning, sorting, storing, packing, and labeling are performed daily. These actions allow workers to perform their job more efficiently, knowing what to expect.
There are five steps that you need to follow in order to implement 5S. Each step is a different action that leads to greater efficiency. If you sort items, it makes them easier to find later. You arrange items by placing them in an order. After you have divided your inventory into groups you can store them in easy-to-reach containers. Finally, when you label your containers, you ensure everything is labeled correctly.
This process requires employees to think critically about how they do their job. Employees must be able to see why they do what they do and find a way to achieve them without having to rely on their old methods. They must learn new skills and techniques in order to implement the 5S system.
The 5S method increases efficiency and morale among employees. They are more motivated to achieve higher efficiency levels as they start to see improvement.