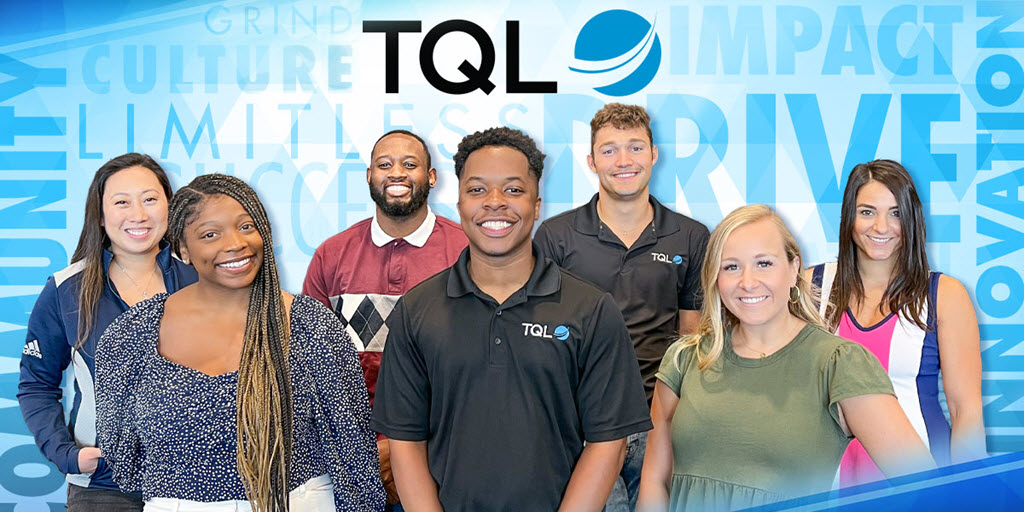
Understanding the five s’s of lean manufacturing is essential if you want to transform your manufacturing processes into a lean machine. They are Standardize, Straighten, Shine, and Sustain. These are some of these steps. You need to train your frontline personnel and team leaders in order to make the most of your lean transformation.
Standardize
Clean and organize the workspace. This is the first step to the 5S process. This may be a one-time job, but if you standardize the process, it can become a routine. To make sure you have a consistent approach when performing 5S tasks, visual cues or checklist templates are all options.
These five s's can help your workplace be more productive and efficient. This will encourage staff to be organised and make their work easier. This will help improve your efficiency by organizing your work area. These five s’s are helpful for improving safety in the workplace. A well-organized workplace will reduce accidents and mistakes, increase productivity, and help you avoid them.
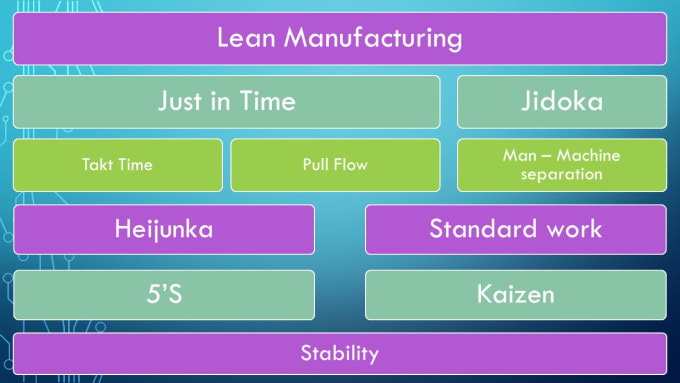
Straighten
Straightening your 5 s's of lean doesn't have to be difficult. Businesses can improve their business processes if they follow lean principles. Workers will be able find the parts they need faster if the components are organized in an assembly plant. This will save time searching for the wrong parts and reduce company safety.
By reducing the number of items in each work area, you'll also save money on consumables and tools. This allows you to significantly reduce your office supplies bill. Straightening the work cells can save you money and improve productivity.
Shine
Shine is about inspecting your workspace and identifying possible issues. Shine is a process that examines equipment and tools to improve flow and reduce waste. Shine can improve the maintenance of a workspace. It allows workers to spot potential problems before they hinder production. Shine can also be used to standardize a workspace to improve output.
Shine is one of the 5S tools used in lean manufacturing. This technique helps to automate work processes and reduce waste. It can be applied to any industry, including manufacturing. It applies the 5S principles to all business. It reduces inventory, work in progress, and supplies stock.
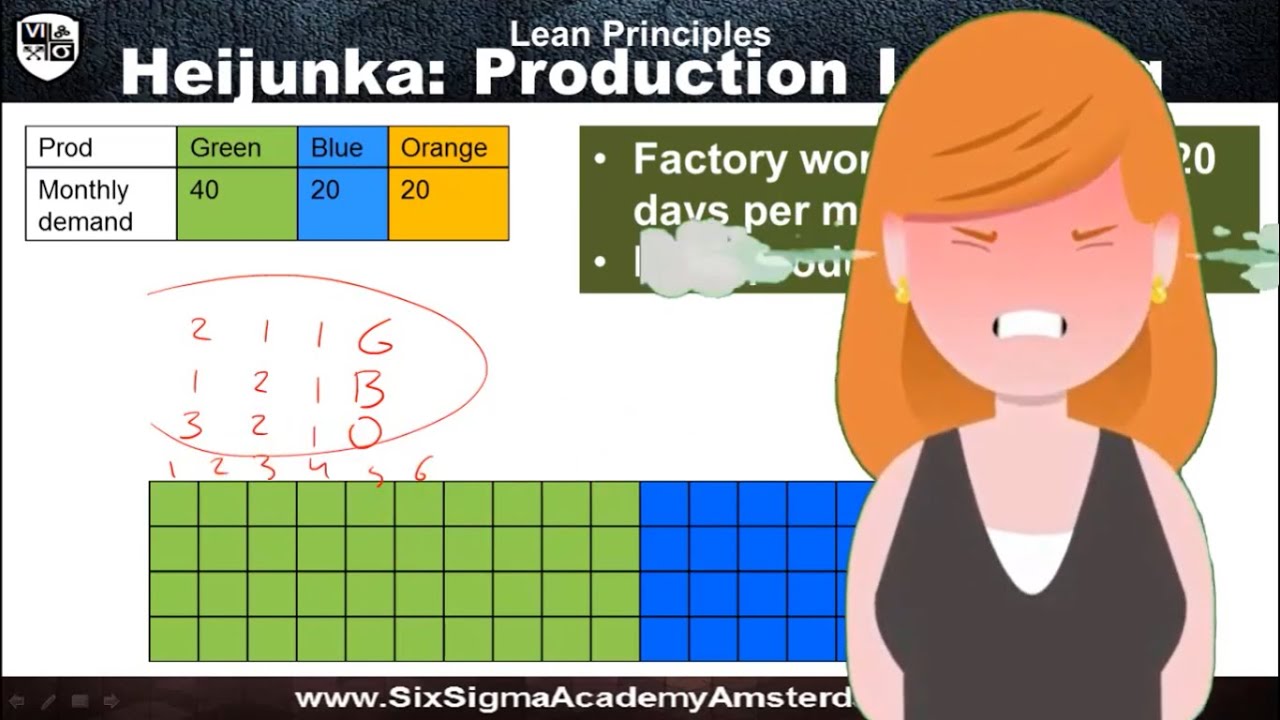
Be a good citizen
The 5 s's are about introducing a standardized system to a facility in order to maintain the 5S. This process is intended to be ongoing and should be repeated to ensure that the facility is functioning at its best. Employees should be trained to conduct 5S audits.
The 5S method emphasizes reducing waste, increasing productivity, and maintaining an orderly work environment. The five principles of Toyota Production System are applied to it. It's a system that organizes workplaces. This system was created by Hiroyuki Hirano, a post-war Japanese engineer, to increase efficiency in manufacturing plants.
FAQ
How can manufacturing excess production be decreased?
It is essential to find better ways to manage inventory to reduce overproduction. This would decrease the time that is spent on inefficient activities like purchasing, storing, or maintaining excess stock. By doing this, we could free up resources for other productive tasks.
This can be done by using a Kanban system. A Kanban board, a visual display to show the progress of work, is called a Kanban board. In a Kanban system, work items move through a sequence of states until they reach their final destination. Each state represents a different priority level.
When work is completed, it can be transferred to the next stage. It is possible to keep a task in the beginning stages until it gets to the end.
This keeps work moving and ensures no work is lost. Managers can view the Kanban board to see how much work they have done. This information allows managers to adjust their workflow based off real-time data.
Lean manufacturing, another method to control inventory levels, is also an option. Lean manufacturing is about eliminating waste from all stages of the production process. Anything that doesn't add value to the product is considered waste. Here are some examples of common types.
-
Overproduction
-
Inventory
-
Packaging not required
-
Overstock materials
These ideas can help manufacturers improve efficiency and reduce costs.
What are the 7 Rs of logistics management?
The acronym 7R's of Logistic is an acronym that stands for seven fundamental principles of logistics management. It was developed by the International Association of Business Logisticians (IABL) and published in 2004 as part of its "Seven Principles of Logistics Management" series.
The acronym is made up of the following letters:
-
Responsible - ensure that all actions taken are within legal requirements and are not harmful to others.
-
Reliable – have faith in your ability and capability to keep promises.
-
It is reasonable to use resources efficiently and not waste them.
-
Realistic - Consider all aspects of operations, including environmental impact and cost effectiveness.
-
Respectful: Treat others with fairness and equity
-
Be resourceful: Look for opportunities to save money or increase productivity.
-
Recognizable is a company that provides customers with value-added solutions.
Is it possible to automate certain parts of manufacturing
Yes! Yes. The Egyptians invent the wheel thousands of year ago. To help us build assembly lines, we now have robots.
In fact, there are several applications of robotics in manufacturing today. These include:
-
Assembly line robots
-
Robot welding
-
Robot painting
-
Robotics inspection
-
Robots that produce products
Automation could also be used to improve manufacturing. 3D printing, for example, allows us to create custom products without waiting for them to be made.
How does a production planner differ from a project manager?
The primary difference between a producer planner and a manager of a project is that the manager usually plans and organizes the whole project, while a production planner is only involved in the planning stage.
What do we need to know about Manufacturing Processes in order to learn more about Logistics?
No. No. But, being familiar with manufacturing processes will give you a better understanding about how logistics works.
What are the responsibilities of a manufacturing manager
A manufacturing manager must ensure that all manufacturing processes are efficient and effective. They must also be alert to any potential problems and take appropriate action.
They should also learn how to communicate effectively with other departments, including sales and marketing.
They should be up to date on the latest trends and be able apply this knowledge to increase productivity and efficiency.
Statistics
- (2:04) MTO is a production technique wherein products are customized according to customer specifications, and production only starts after an order is received. (oracle.com)
- Many factories witnessed a 30% increase in output due to the shift to electric motors. (en.wikipedia.org)
- Job #1 is delivering the ordered product according to specifications: color, size, brand, and quantity. (netsuite.com)
- In 2021, an estimated 12.1 million Americans work in the manufacturing sector.6 (investopedia.com)
- According to a Statista study, U.S. businesses spent $1.63 trillion on logistics in 2019, moving goods from origin to end user through various supply chain network segments. (netsuite.com)
External Links
How To
How to use the Just In-Time Production Method
Just-in time (JIT), is a process that reduces costs and increases efficiency in business operations. This is where you have the right resources at the right time. This means that you only pay the amount you actually use. Frederick Taylor developed the concept while working as foreman in early 1900s. After observing how workers were paid overtime for late work, he realized that overtime was a common practice. He decided to ensure workers have enough time to do their jobs before starting work to improve productivity.
JIT is an acronym that means you need to plan ahead so you don’t waste your money. Also, you should look at the whole project from start-to-finish and make sure you have the resources necessary to address any issues. If you expect problems to arise, you will be able to provide the necessary equipment and personnel to address them. This way, you won't end up paying extra money for things that weren't really necessary.
There are several types of JIT techniques:
-
Demand-driven: This type of JIT allows you to order the parts/materials required for your project on a regular basis. This will allow to track how much material has been used up. You'll also be able to estimate how long it will take to produce more.
-
Inventory-based: This allows you to store the materials necessary for your projects in advance. This allows you predict the amount you can expect to sell.
-
Project-driven: This method allows you to set aside enough funds for your project. Once you have an idea of how much material you will need, you can purchase the necessary materials.
-
Resource-based JIT : This is probably the most popular type of JIT. You assign certain resources based off demand. For example, if there is a lot of work coming in, you will have more people assigned to them. You'll have fewer orders if you have fewer.
-
Cost-based: This is the same as resource-based except that you don't care how many people there are but how much each one of them costs.
-
Price-based: This is a variant of cost-based. However, instead of focusing on the individual workers' costs, this looks at the total price of the company.
-
Material-based is an alternative to cost-based. Instead of looking at the total cost in the company, this method focuses on the average amount of raw materials that you consume.
-
Time-based JIT is another form of resource-based JIT. Instead of focusing solely on the amount each employee costs, focus on how long it takes for the project to be completed.
-
Quality-based: This is yet another variation of resource-based JIT. Instead of thinking about the cost of each employee or the time it takes to produce something, you focus on how good your product quality.
-
Value-based JIT : This is the newest type of JIT. You don't worry about whether the products work or if they meet customer expectations. Instead, your goal is to add value to the market.
-
Stock-based: This stock-based method focuses on the actual quantity of products being made at any given time. It's useful when you want maximum production and minimal inventory.
-
Just-in time (JIT), planning: This is a combination JIT/supply chain management. It's the process of scheduling delivery of components immediately after they are ordered. It's important because it reduces lead times and increases throughput.