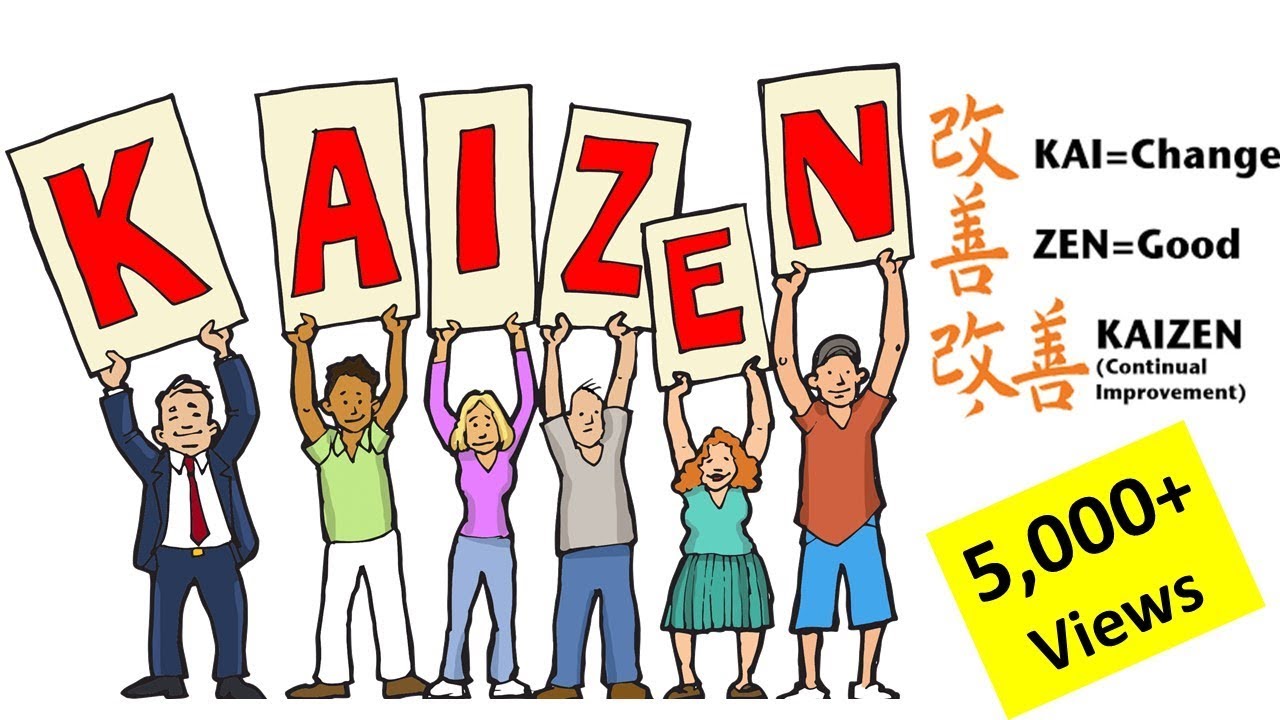
Despite the recent economic boom, the US manufacturing industry remains a vital contributor to the country's economy. It supports 12.8 million jobs, accounts for one-third of private-sector employment, and employs a wider workforce than the average American. However, it has seen its share in the national output decline since the Great Recession. And its employment rate has fallen to just 12 percent. The manufacturing industry has been facing structural problems, including trade deficits, productivity, and output. These issues are being worked on, but their long-term impacts remain unclear. Although the US manufacturing sector appears to be in a positive place, it is up to the United States to decide if it should rebound.
Manufacturing is a capital-intensive business. This sector is evolving as new technologies are developed. Firms invest in new technologies to improve productivity and increase the skillset of their workers. They are also developing a pipeline of future workers. Manufacturers are also investing in the upskilling of their current workforce. This helps to improve their marketability. Firms are also working to improve their supply chains in order to prevent future disruptions.

Manufacturers are now facing increasing supply chain costs and are being challenged. The US has the ability to overcome these challenges by strengthening their innovation system. The US will have to avoid tariff warfare with other countries who want to export to the US. It also needs to maintain open trade policy to ensure its manufacturers remain competitive.
The United States is a world leader with a growing presence over the past century. Because of this, the United States holds a large percentage of the global oil-and-gas demand. It is still the world's most important manufacturing country, but it is at risk. Its aging population and low international immigration are two reasons for this. It can also become more competitive by investing into new technologies that will improve production efficiency, and make it more sustainably.
US manufacturing sectors account for $2.3 Trillion in GDP. This figure is 20 percent of the nation’s capital investment, and 35 percent productivity growth. Q1 2018 saw record manufacturing output of $2.00 trillion. This record-breaking figure for US manufacturing was set in Q1 2018. It's also the highest since the Great Recession. Furthermore, the manufacturing sector is performing better than the recovery of its labor market.
The United States is second in the world in manufacturing, only behind China. The nation's 60 percent exports are made up of manufacturing, which accounts for a significant portion of R&D spending. However, manufacturing output dropped from the fourth quarter in 2007 to 2009 A few states also saw a decline in manufacturing output. Manufacturing has a stronger presence in the Eighth District States, and manufacturing output share has increased in many of those states.
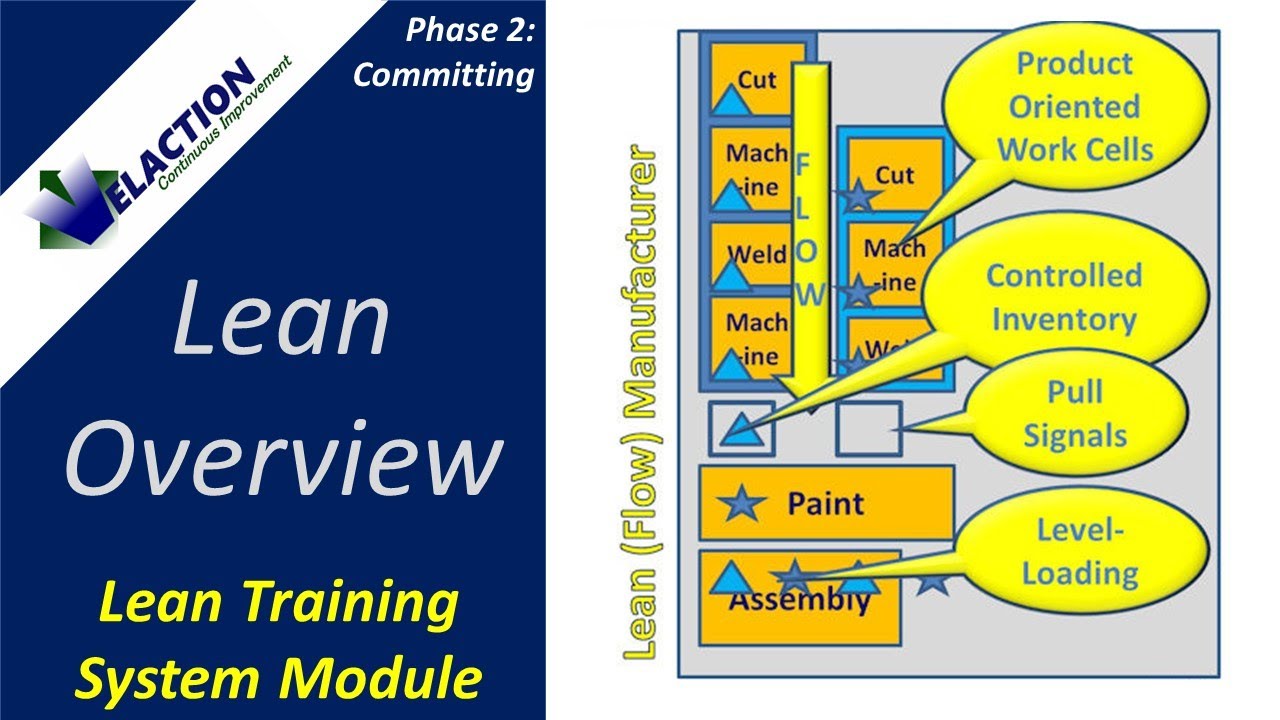
Manufacturing output dropped 15.2 percent to pre-pandemic levels during the fourth quarter 2007. Manufacturing output decreased by 6.4% in the first three quarters of 2009. However, manufacturing output increased in Illinois, Indiana, and Kentucky, as well as in Ohio and Michigan.
FAQ
What type of jobs is there in logistics
There are many kinds of jobs available within logistics. These are some of the jobs available in logistics:
-
Warehouse workers - They load and unload trucks and pallets.
-
Transport drivers - These are people who drive trucks and trailers to transport goods or perform pick-ups.
-
Freight handlers, - They sort out and pack freight in warehouses.
-
Inventory managers – They manage the inventory in warehouses.
-
Sales representatives - They sell products to customers.
-
Logistics coordinators – They plan and coordinate logistics operations.
-
Purchasing agents - They purchase goods and services needed for company operations.
-
Customer service representatives - Answer calls and email from customers.
-
Shippers clerks - They process shipping order and issue bills.
-
Order fillers are people who fill orders based only on what was ordered.
-
Quality control inspectors: They inspect outgoing and incoming products for any defects.
-
Others - There are many types of jobs in logistics such as transport supervisors and cargo specialists.
What are the 7 Rs of logistics management?
The acronym 7R's for Logistics stands to represent the seven basic principles in logistics management. It was developed and published by the International Association of Business Logisticians in 2004 as part of the "Seven Principles of Logistics Management".
The following letters form the acronym:
-
Responsible - to ensure that all actions are within the legal requirements and are not detrimental to others.
-
Reliable – have faith in your ability and capability to keep promises.
-
Reasonable - use resources efficiently and don't waste them.
-
Realistic – Consider all aspects, including cost-effectiveness as well as environmental impact.
-
Respectful – Treat others fairly and equitably.
-
Reliable - Find ways to save money and increase your productivity.
-
Recognizable - provide customers with value-added services.
What's the difference between Production Planning & Scheduling?
Production Planning (PP), or production planning, is the process by which you determine what products are needed at any given time. This is accomplished by forecasting the demand and identifying production resources.
Scheduling involves the assignment of dates and times to tasks in order to complete them within the timeframe.
What are manufacturing & logistics?
Manufacturing refers the process of producing goods from raw materials through machines and processes. Logistics manages all aspects of the supply chain, including procurement, production planning and distribution, inventory control, transportation, customer service, and transport. Manufacturing and logistics are often considered together as a broader term that encompasses both the process of creating products and delivering them to customers.
Statistics
- According to the United Nations Industrial Development Organization (UNIDO), China is the top manufacturer worldwide by 2019 output, producing 28.7% of the total global manufacturing output, followed by the United States, Japan, Germany, and India.[52][53] (en.wikipedia.org)
- It's estimated that 10.8% of the U.S. GDP in 2020 was contributed to manufacturing. (investopedia.com)
- In the United States, for example, manufacturing makes up 15% of the economic output. (twi-global.com)
- Job #1 is delivering the ordered product according to specifications: color, size, brand, and quantity. (netsuite.com)
- [54][55] These are the top 50 countries by the total value of manufacturing output in US dollars for its noted year according to World Bank.[56] (en.wikipedia.org)
External Links
How To
How to use 5S in Manufacturing to Increase Productivity
5S stands to stand for "Sort", “Set In Order", “Standardize", and "Store". Toyota Motor Corporation created the 5S methodology in 1954. It improves the work environment and helps companies to achieve greater efficiency.
This method aims to standardize production processes so that they are repeatable, measurable and predictable. This means that tasks such as cleaning, sorting, storing, packing, and labeling are performed daily. Through these actions, workers can perform their jobs more efficiently because they know what to expect from them.
There are five steps to implementing 5S, including Sort, Set In Order, Standardize, Separate and Store. Each step has a different action and leads to higher efficiency. If you sort items, it makes them easier to find later. You arrange items by placing them in an order. Once you have separated your inventory into groups and organized them, you will store these groups in easily accessible containers. Finally, when you label your containers, you ensure everything is labeled correctly.
This requires employees to critically evaluate how they work. Employees must be able to see why they do what they do and find a way to achieve them without having to rely on their old methods. To be successful in the 5S system, employees will need to acquire new skills and techniques.
The 5S method not only increases efficiency but also boosts morale and teamwork. As they begin to see improvements, they feel motivated to continue working towards the goal of achieving higher levels of efficiency.