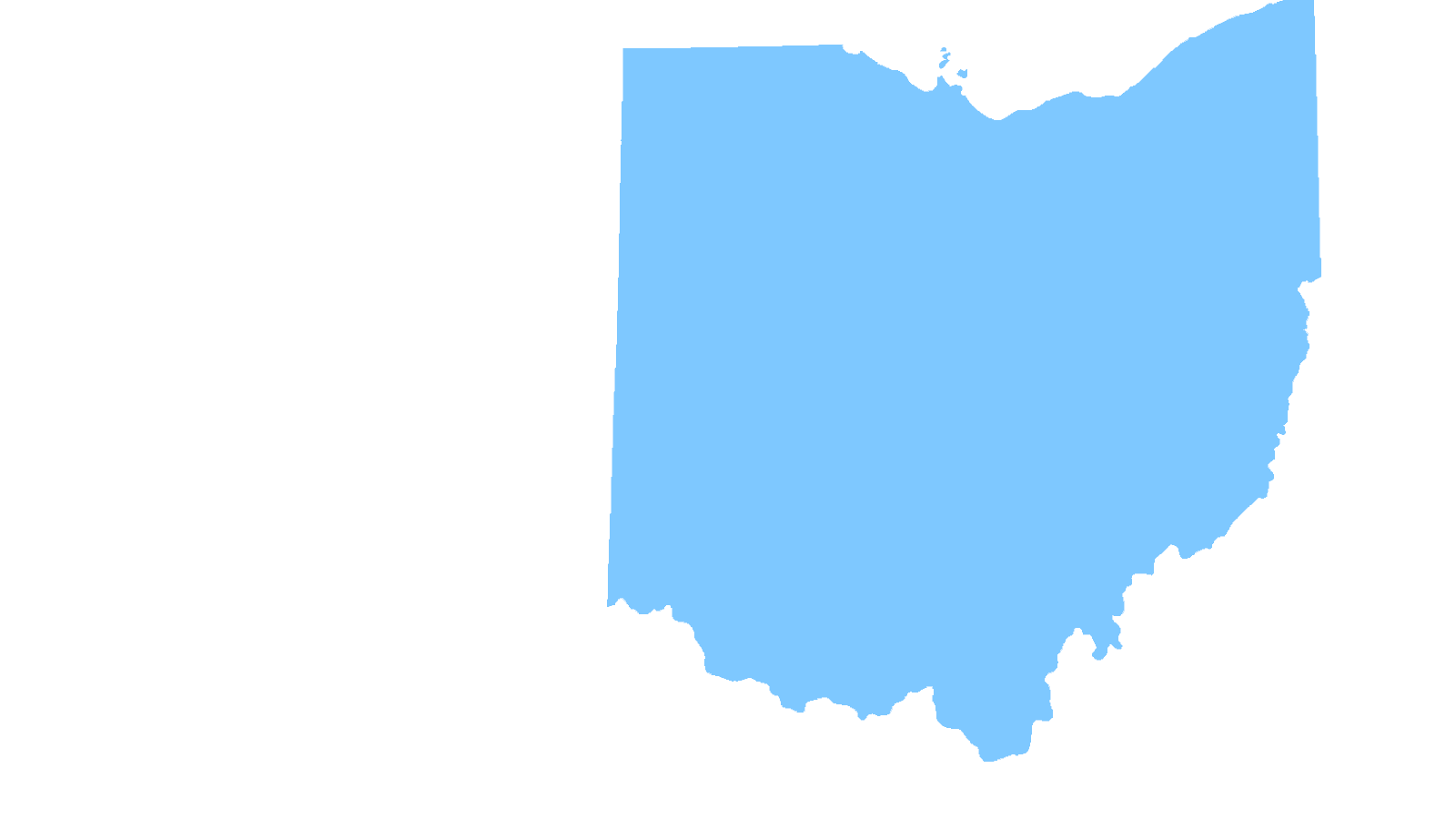
Durable goods have items that don't wear out quickly and can provide utility for a prolonged period. These products are more durable than nondurable goods which can only be used once. They are likely to continue providing the same or even greater utility for years. A durable car, for example, will last many years.
Nondurable goods may be consumed immediately
Nondurable goods can be consumed right away, in contrast to durable goods which last a long time. In a recession, consumers tend to avoid spending money on durable goods but continue to purchase nondurable goods. These items are typically low-priced and can be bought with cash. Examples of nondurable goods include meat, fruits, vegetables, dairy products, and bakery products. Others include dish soap, detergent, and cosmetics.
Nondurable goods generally last less than three years and are therefore the most affordable. They are also purchased relatively often, allowing consumers to buy them frequently without concern for their future value. Most nondurable goods are also disposable and can be bought only one time, such as packaged food and laundry detergent. However, service goods are intangible and are created in response to customer needs. Consumers plan their purchases based on how they perceive a product, which can vary depending on its price.
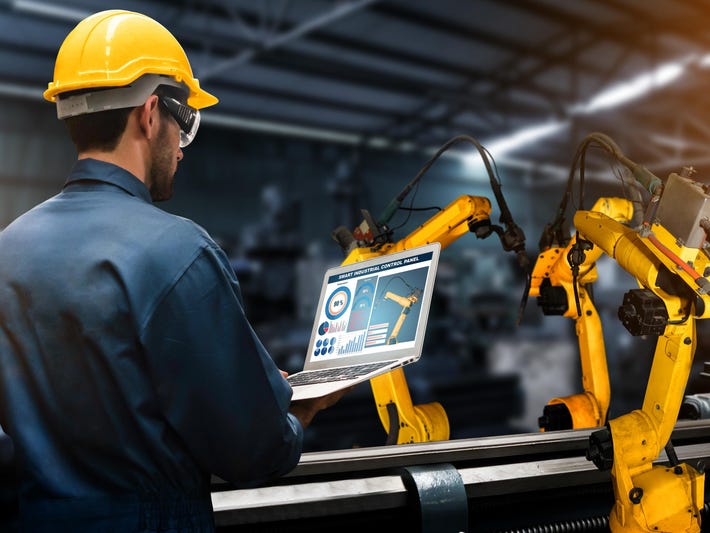
Durable goods are, in contrast, products that are expected provide a steady flow of utility over a time period. These products are often called consumer durables. They include automobiles, household furniture, sporting items, and jewelry. Durables tend be purchased during periods of economic growth while nondurables may be purchased in times when there is economic recession.
Durable goods can last for more than a year
Durable goods are tangible commodities which last at least one year with normal usage. They can be broken down into producer durables and consumers durables. Consumer durables include household goods such as cars, boats, and furniture, while producer durables include machinery, appliances, and fine jewelry.
Durable goods are expected to last at least three years, but they may require servicing or repair. The design of durable goods is so that there is little chance of breakage during the first few years of use. If you take care of your durable goods properly, they can last for up to 20 more years.
When the economy is experiencing growth, the demand for durable goods is often a leading economic indicator. In order to increase employment and improve investment returns, durable goods should be sold more often. On the other hand, declining sales of durable products could signal a decline economic activity. This is because consumers use their money to repair and service existing products rather than spending it on new items. In this way, a slowdown of durable goods might lead to a downturn.
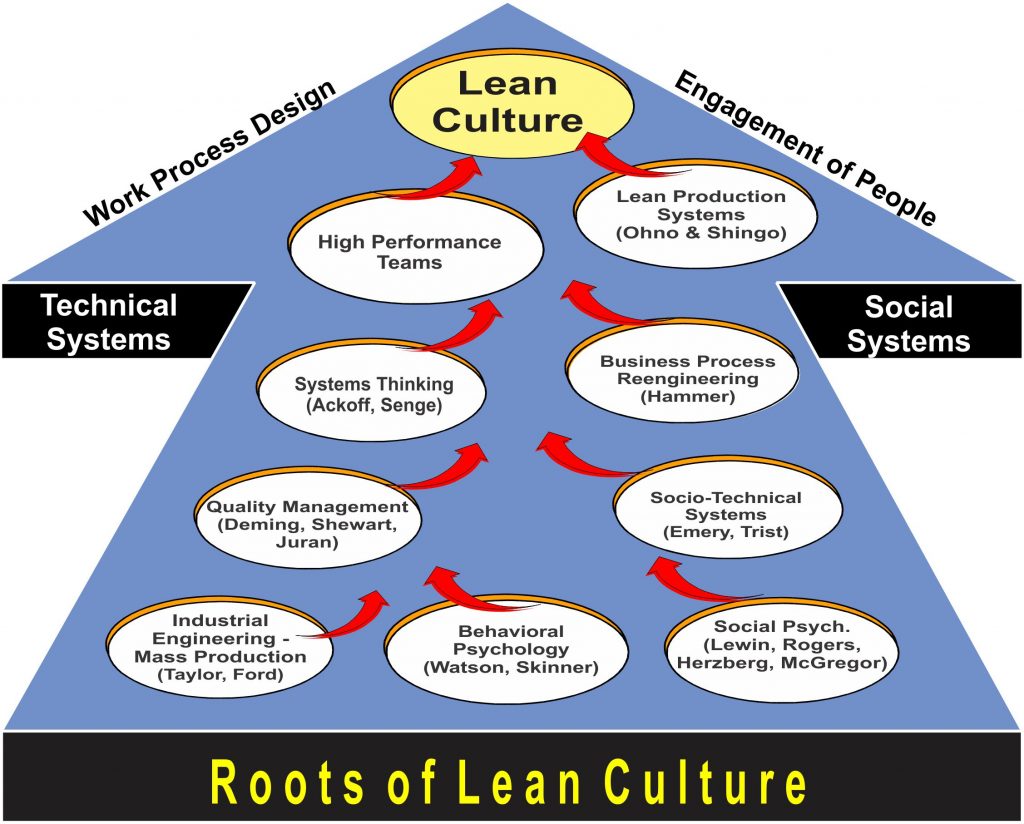
Impact of the COVID-19 pandemic sur durable goods
COVID-19, a pandemic that caused widespread illness, has impacted consumer spending, including on durable goods. People stopped going to the gym and stopped attending social events as a result of the disease. Also, they stopped hailing cabs which resulted to decreased consumer spending. People instead spent more time in their own homes, producing things and engaging in leisure activities. This in turn led to lower consumer spending for restaurants and other services.
The impact of the COVID-19 pandemic on the US economy has been striking. In addition to the increase in durable goods, strong fiscal policies were implemented by the government that led to an increase in household disposable income. This effect could be responsible for half the rise in consumer durable good spending in 2020.
The COVID-19 outbreak has affected individuals and communities as well businesses. While the impact on fast-moving goods has received much attention, less coverage has focused on the impact of the disease on durable goods. NielsenIQ BASES just released a new survey showing that over 33% of Americans have made durable goods purchases to combat the disease. Many people's purchasing habits have been affected by the disease, which is a result of more time spent at home with their kids.
FAQ
What jobs are available in logistics?
There are many kinds of jobs available within logistics. Here are some examples:
-
Warehouse workers - They load trucks and pallets.
-
Transportation drivers - They drive trucks and trailers to deliver goods and carry out pick-ups.
-
Freight handlers - They sort and pack freight in warehouses.
-
Inventory managers: They are responsible for the inventory and management of warehouses.
-
Sales reps are people who sell products to customers.
-
Logistics coordinators – They plan and coordinate logistics operations.
-
Purchasing agents - They purchase goods and services needed for company operations.
-
Customer service representatives are available to answer customer calls and emails.
-
Ship clerks - They issue bills and process shipping orders.
-
Order fillers are people who fill orders based only on what was ordered.
-
Quality control inspectors are responsible for inspecting incoming and outgoing products looking for defects.
-
Others - There are many types of jobs in logistics such as transport supervisors and cargo specialists.
What is the job of a production plan?
A production planner makes sure all project elements are delivered on schedule, within budget, as well as within the agreed scope. They also ensure the quality of the product and service meets the client's requirements.
What skills should a production planner have?
Being a production planner is not easy. You need to be organized and flexible. Also, you must be able and willing to communicate with clients and coworkers.
What does manufacturing industry mean?
Manufacturing Industries refers to businesses that manufacture products. These products are sold to consumers. These companies employ many processes to achieve this purpose, such as production and distribution, retailing, management and so on. They manufacture goods from raw materials using machines and other equipment. This covers all types of manufactured goods including clothing, food, building supplies and furniture, as well as electronics, tools, machinery, vehicles and pharmaceuticals.
Statistics
- Job #1 is delivering the ordered product according to specifications: color, size, brand, and quantity. (netsuite.com)
- According to a Statista study, U.S. businesses spent $1.63 trillion on logistics in 2019, moving goods from origin to end user through various supply chain network segments. (netsuite.com)
- In 2021, an estimated 12.1 million Americans work in the manufacturing sector.6 (investopedia.com)
- Many factories witnessed a 30% increase in output due to the shift to electric motors. (en.wikipedia.org)
- You can multiply the result by 100 to get the total percent of monthly overhead. (investopedia.com)
External Links
How To
How to Use 5S to Increase Productivity in Manufacturing
5S stands for "Sort", "Set In Order", "Standardize", "Separate" and "Store". Toyota Motor Corporation created the 5S methodology in 1954. This methodology helps companies improve their work environment to increase efficiency.
The idea behind standardizing production processes is to make them repeatable and measurable. It means tasks like cleaning, sorting or packing, labeling, and storing are done every day. Because workers know what they can expect, this helps them perform their jobs more efficiently.
Implementing 5S requires five steps. These are Sort, Set In Order, Standardize. Separate. And Store. Each step is a different action that leads to greater efficiency. Sorting things makes it easier to find them later. When you arrange items, you place them together. Then, after you separate your inventory into groups, you store those groups in containers that are easy to access. Finally, when you label your containers, you ensure everything is labeled correctly.
Employees must be able to critically examine their work practices. Employees must understand why they do certain tasks and decide if there's another way to accomplish them without relying on the old ways of doing things. They must learn new skills and techniques in order to implement the 5S system.
The 5S method not only increases efficiency but also boosts morale and teamwork. Once they start to notice improvements, they are motivated to keep working towards their goal of increasing efficiency.