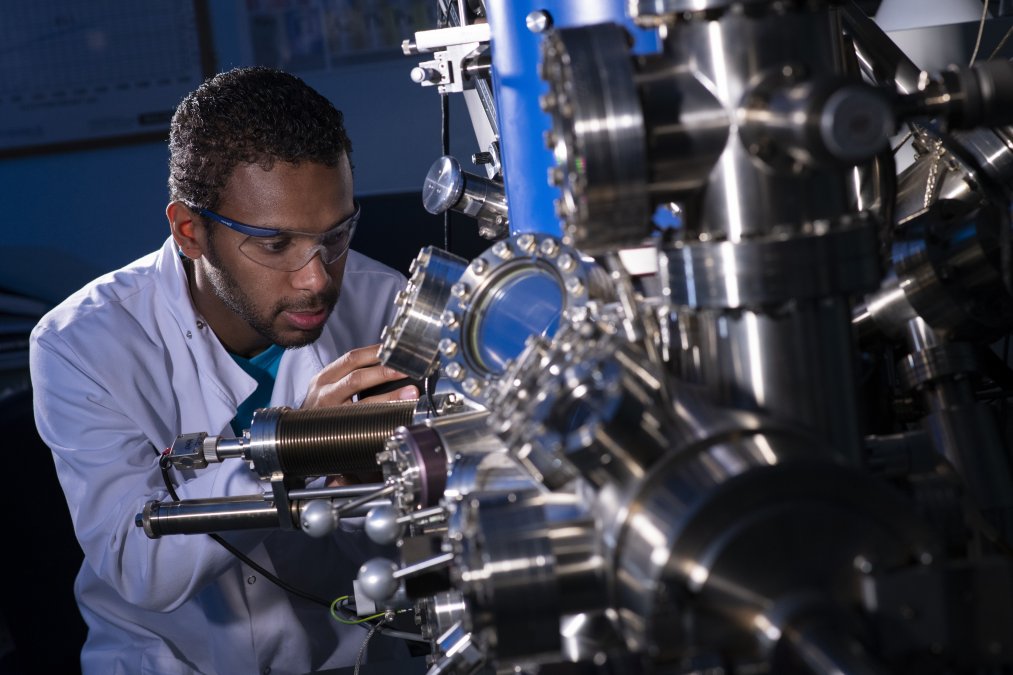
Japanese factories make high-quality products at affordable prices. They account for five percent of the country’s total GDP. However, they have struggled with tighter standards, growing competition and the cost pressures of the recent recession.
Last year, for example, a white paper by the government found that Japanese companies weren't prepared to cope with a reduction in parts procurement. The recession was a severe blow to the Japanese automotive industry. The auto manufacturing industry relies on over 30,000 parts. Any disruption to the supply chain could cause the production to cease. Some parts are not available in substitutes.
Japanese manufacturers collaborate closely with suppliers in order to fix problems and improve efficiency. This is to ensure that their products are high quality. They also encourage workers, salesmen, and quality inspectors to give feedback.
Japanese manufacturers have been worried about the rising number of factory accidents. A series of safety scandals have rocked the country's manufacturing industry. This has led to increased scrutiny of the standard of factory work.
Non-regular staff is another problem that has impacted the production of Japanese products. While non-regular employees can help companies reduce labor costs, they also increase the risk for accidents and de-skill their production floor. To make their workers safer and more productive, companies have started to train regular employees.
Japan's growing labor shortage is due to the country's declining birthrate. The proportion of companies complaining about a labor shortage has reached a 25-year peak. Japanese companies will face greater difficulties if the labor force shrinks.
Despite the shortage of skilled workers, a large percentage of factories have been cutting costs. Many "factories" are now employing fewer than ten workers. These workshops are known for producing the highest quality equipment in the world.
Japan's manufacturing sector is being challenged by South Korea and China. Many factories are now trying to increase productivity and reduce costs. Nevertheless, the Japanese government has warned that the industry will suffer if it loses its competitive edge in overseas markets.
Japan is facing increasing competition from Asia and elsewhere, and the question of whether it can adapt its processes to keep up with demand and adapt fast enough. Even if it is able to adapt, skilled workers are expected to increase.
Japanese factories are a crucial source of components that can be used in global markets. They are also a source of advanced materials, such as silicon chips, that are used in computers and smart phones. While Chinese factories can perform low-cost assembly operations well, essential components are sourced from Japan.
The Japanese are now facing increased competition from foreigners, despite their efforts to improve their productivity. Due to the economic downturn, their products were less valued in the domestic markets. This has forced them to cut costs. But despite these challenges, the Japanese have been able to achieve a high level of excellence in their production.
FAQ
What is production plan?
Production Planning is the creation of a plan to cover all aspects, such as scheduling, budgeting. Location, crew, equipment, props and other details. This document is designed to make sure everything is ready for when you're ready to shoot. This document should include information about how to achieve the best results on-set. This information includes locations, crew details and equipment requirements.
The first step is to outline what you want to film. You may already know where you want the film to be shot, or perhaps you have specific locations and sets you wish to use. Once you've identified the locations and scenes you want to use, you can begin to plan what elements you need for each scene. You might decide you need a car, but not sure what make or model. This is where you can look up car models online and narrow down your options by choosing from different makes and models.
Once you have found the right vehicle, you can think about adding accessories. Do you have people who need to be seated in the front seat? Maybe you need someone to move around in the back. Maybe you want to change the interior color from black to white? These questions will help to determine the style and feel of your car. Also, think about what kind of shots you would like to capture. What type of shots will you choose? Perhaps you want to show the engine or the steering wheel? This will allow you to determine the type of car you want.
Once you have all the information, you are ready to create a plan. You can use a schedule to determine when and where you need it to be shot. The schedule will show you when to get there, what time to leave, and when to return home. Everyone knows exactly what they should do and when. You can also make sure to book extra staff in advance if you have to hire them. There is no point in hiring someone who won't turn up because you didn't let him know.
When creating your schedule, you will also need to consider the number of days you need to film. Some projects are quick and easy, while others take weeks. While creating your schedule, it is important to remember whether you will require more than one shot per day. Shooting multiple takes over the same location will increase costs and take longer to complete. If you are unsure if you need multiple takes, it is better to err on the side of caution and shoot fewer takes rather than risk wasting money.
Budgeting is another crucial aspect of production plan. It is important to set a realistic budget so you can work within your budget. Keep in mind that you can always reduce your budget if you face unexpected difficulties. You shouldn't underestimate the amount you'll spend. You will end up spending less money if you underestimate the cost of something.
Production planning can be a complex process. However, once you know how everything works together it will become easier to plan future projects.
How does a Production Planner differ from a Project Manager?
The major difference between a Production Planner and a Project Manager is that a Project Manager is often the person responsible for organizing and planning the entire project. While a Production Planner is involved mainly in the planning stage,
How can manufacturing prevent production bottlenecks?
Avoiding production bottlenecks is as simple as keeping all processes running smoothly, from the time an order is received until the product ships.
This includes both quality control and capacity planning.
Continuous improvement techniques such Six Sigma can help you achieve this.
Six Sigma is a management system used to improve quality and reduce waste in every aspect of your organization.
It emphasizes consistency and eliminating variance in your work.
Statistics
- You can multiply the result by 100 to get the total percent of monthly overhead. (investopedia.com)
- Many factories witnessed a 30% increase in output due to the shift to electric motors. (en.wikipedia.org)
- According to the United Nations Industrial Development Organization (UNIDO), China is the top manufacturer worldwide by 2019 output, producing 28.7% of the total global manufacturing output, followed by the United States, Japan, Germany, and India.[52][53] (en.wikipedia.org)
- (2:04) MTO is a production technique wherein products are customized according to customer specifications, and production only starts after an order is received. (oracle.com)
- According to a Statista study, U.S. businesses spent $1.63 trillion on logistics in 2019, moving goods from origin to end user through various supply chain network segments. (netsuite.com)
External Links
How To
How to use 5S to increase Productivity in Manufacturing
5S stands for "Sort", 'Set In Order", 'Standardize', & Separate>. The 5S methodology was developed at Toyota Motor Corporation in 1954. This methodology helps companies improve their work environment to increase efficiency.
This approach aims to standardize production procedures, making them predictable, repeatable, and easily measurable. This means that daily tasks such as cleaning and sorting, storage, packing, labeling, and packaging are possible. These actions allow workers to perform their job more efficiently, knowing what to expect.
Five steps are required to implement 5S: Sort, Set In Order, Standardize. Separate. Each step requires a different action, which increases efficiency. For example, when you sort things, you make them easy to find later. You arrange items by placing them in an order. Once you have separated your inventory into groups and organized them, you will store these groups in easily accessible containers. Labeling your containers will ensure that everything is correctly labeled.
This requires employees to critically evaluate how they work. Employees must understand why they do certain tasks and decide if there's another way to accomplish them without relying on the old ways of doing things. To implement the 5S system, employees must acquire new skills and techniques.
The 5S method increases efficiency and morale among employees. Once they start to notice improvements, they are motivated to keep working towards their goal of increasing efficiency.