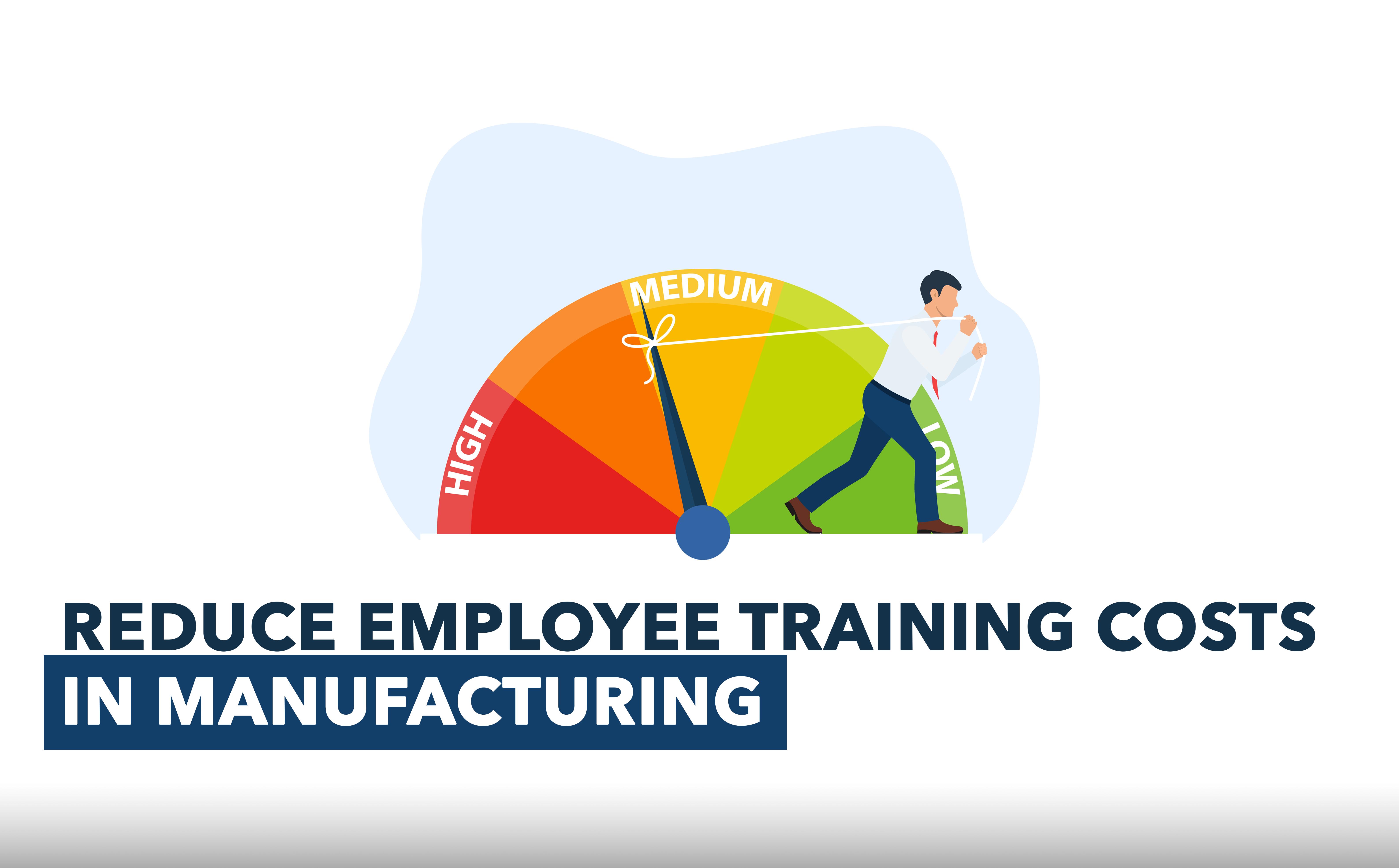
Located in Gibson County, Indiana, Toyota Motor Manufacturing Indiana Inc. is the first Toyota plant to be wholly owned by Toyota in the United States. It is home to Toyota's full-size pickup trucks (including the Avalon/Corolla) and also the Sienna van. The Toyota RAV4 Hybrid hybrid is also manufactured here. It is the most successful Toyota hybrid ever.
The plant was originally intended to make the Toyota Highlander. Instead, it moved to Gibson County, Indiana. Since 2011, the Toyota RAV4 Hybrid compact SUV has been produced here, as well as the Lexus ES 350. Toyota spent over $1.33 billion on the plant in 2017.
Toyota Safety Sense 2.5+ can also be manufactured here. This feature includes automatic emergency braking. It is also currently preparing all the 2018 Camry models. The new model boasts a new transmission with more power and a more stylish look. It will retail for $25,900
The largest American manufacturer of the Toyota Camry, Toyota. It is the most popular midsize sedan in America and has been so for 15 years. Toyota has sold 10 million Camry vehicles in Kentucky. The hybrid model was manufactured at the plant, which is the only one in North America.
Toyota Production System is an assortment of practices and techniques that improve efficiency and quality. This system also includes the Toyota Production Engineering and Manufacturing Center, which will house 600 Toyota engineers. It will be the first center to build hydrogen fuel cell modules for heavy-duty commercial trucks. The facility can build up to 100,000 vehicles per year.
Toyota has spent $1.5 billion on the plant in the last five year. The plant has also been home to 700 additional employees. The investment will result in 470,100 new jobs in the United States by 2020. Toyota has made over $147 Million in Kentucky non-profit partners since 1986.
The Toyota Camry is a reliable vehicle that is also highly stylish. It has the GA-K platform, and a new transmission. It is fun to drive. Consumer Reports listed the Toyota Camry as the number one selling car in America in July.
Toyota's production system incorporates many elements including continuous improvement and just-in time parts delivery. It also includes a sophisticated robotic welding process. Toyota's Kentucky investment is evident in the Toyota Production Engineering and Manufacturing Center.
Toyota has a new production facility design that allows them to reduce construction and cooling costs. A Visitor Center is also featured in the building. It features interactive video displays as well as exhibits about hybrid technology. Toyota will be producing up to 2,000,000 vehicles in North America over the next 10 year. This is the largest Toyota facility outside Japan.
Toyota's New Global Architecture marks a major improvement in the company's production systems. The strategy includes an updated engine, production organization, and a module to unify the structure of vehicle parts. The new design retains Toyota's innovative spirit while reflecting Toyota's traditional values.
FAQ
Why should you automate your warehouse?
Modern warehouses are increasingly dependent on automation. With the rise of ecommerce, there is a greater demand for faster delivery times as well as more efficient processes.
Warehouses need to adapt quickly to meet changing needs. In order to do this, they need to invest in technology. Automation of warehouses offers many benefits. Here are some benefits of investing in automation
-
Increases throughput/productivity
-
Reduces errors
-
Increases accuracy
-
Boosts safety
-
Eliminates bottlenecks
-
Companies can scale more easily
-
It makes workers more efficient
-
The warehouse can be viewed from all angles.
-
Enhances customer experience
-
Improves employee satisfaction
-
Reduces downtime and improves uptime
-
This ensures that quality products are delivered promptly
-
Eliminates human error
-
This helps to ensure compliance with regulations
Why is logistics so important in manufacturing?
Logistics are essential to any business. Logistics can help you achieve amazing results by helping to manage product flow from raw materials to finished products.
Logistics also play a major role in reducing costs and increasing efficiency.
What do you mean by warehouse?
A warehouse is an area where goods are stored before being sold. It can be either an indoor or outdoor space. In some cases, it may be a combination of both.
Statistics
- (2:04) MTO is a production technique wherein products are customized according to customer specifications, and production only starts after an order is received. (oracle.com)
- In 2021, an estimated 12.1 million Americans work in the manufacturing sector.6 (investopedia.com)
- According to the United Nations Industrial Development Organization (UNIDO), China is the top manufacturer worldwide by 2019 output, producing 28.7% of the total global manufacturing output, followed by the United States, Japan, Germany, and India.[52][53] (en.wikipedia.org)
- In the United States, for example, manufacturing makes up 15% of the economic output. (twi-global.com)
- You can multiply the result by 100 to get the total percent of monthly overhead. (investopedia.com)
External Links
How To
How to Use lean manufacturing in the Production of Goods
Lean manufacturing (or lean manufacturing) is a style of management that aims to increase efficiency, reduce waste and improve performance through continuous improvement. It was developed by Taiichi Okono in Japan, during the 1970s & 1980s. TPS founder Kanji Takoda awarded him the Toyota Production System Award (TPS). The first book published on lean manufacturing was titled "The Machine That Changed the World" written by Michael L. Watkins and published in 1990.
Lean manufacturing is often described as a set if principles that help improve the quality and speed of products and services. It emphasizes the elimination of defects and waste throughout the value stream. The five-steps of Lean Manufacturing are just-in time (JIT), zero defect and total productive maintenance (TPM), as well as 5S. Lean manufacturing eliminates non-value-added tasks like inspection, rework, waiting.
Lean manufacturing not only improves product quality but also reduces costs. Companies can also achieve their goals faster by reducing employee turnover. Lean manufacturing is a great way to manage the entire value chain including customers, suppliers, distributors and retailers as well as employees. Lean manufacturing is widely practiced in many industries around the world. For example, Toyota's philosophy underpins its success in automobiles, electronics, appliances, healthcare, chemical engineering, aerospace, paper, food, etc.
Lean manufacturing is based on five principles:
-
Define value - Find out what your business contributes to society, and what makes it different from other competitors.
-
Reduce Waste - Remove any activity which doesn't add value to your supply chain.
-
Create Flow – Ensure that work flows smoothly throughout the process.
-
Standardize and Simplify – Make processes as consistent, repeatable, and as simple as possible.
-
Build Relationships - Establish personal relationships with both internal and external stakeholders.
Although lean manufacturing isn't a new concept in business, it has gained popularity due to renewed interest in the economy after the 2008 global financial crisis. Many businesses have adopted lean manufacturing techniques to help them become more competitive. In fact, some economists believe that lean manufacturing will be an important factor in economic recovery.
Lean manufacturing is becoming a popular practice in automotive. It has many advantages. These include improved customer satisfaction, reduced inventory levels, lower operating costs, increased productivity, and better overall safety.
The principles of lean manufacturing can be applied in almost any area of an organization. It is especially useful for the production aspect of an organization, as it ensures that every step in the value chain is efficient and effective.
There are three main types:
-
Just-in Time Manufacturing, (JIT): This kind of lean manufacturing is also commonly known as "pull-systems." JIT refers to a system in which components are assembled at the point of use instead of being produced ahead of time. This approach reduces lead time, increases availability and reduces inventory.
-
Zero Defects Manufacturing (ZDM),: ZDM is a system that ensures no defective units are left the manufacturing facility. If a part is required to be repaired on the assembly line, it should not be scrapped. This is true even for finished products that only require minor repairs prior to shipping.
-
Continuous Improvement (CI): CI aims to improve the efficiency of operations by continuously identifying problems and making changes in order to eliminate or minimize waste. Continuous improvement involves continuous improvement of processes and people as well as tools.