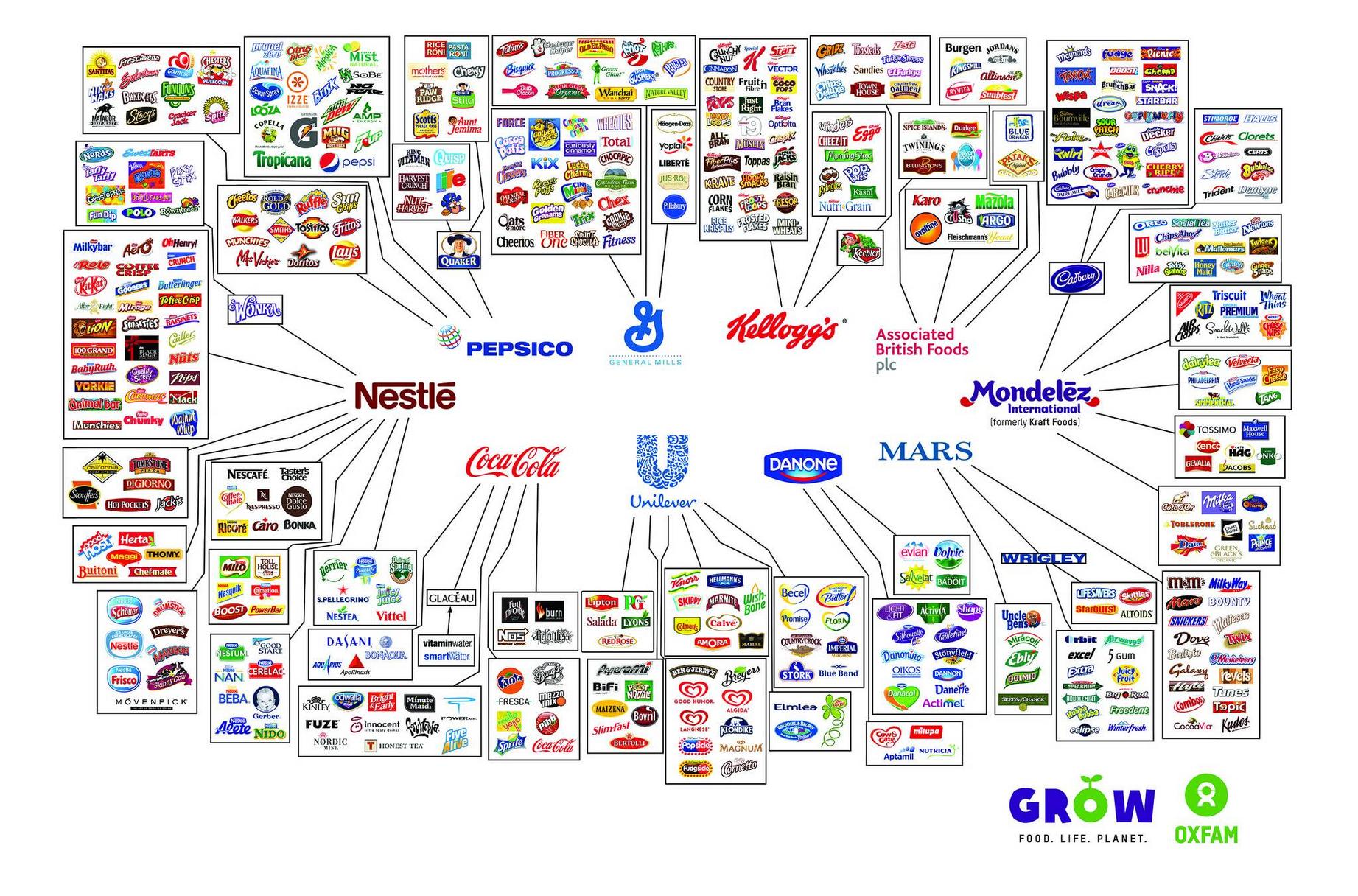
The Defense Industrial Base or DIB is a network of approximately 200,000 companies that supply goods to the Department of Defense. It includes startups, big corporations, small businesses. The Government Accountability Office has released a new report that highlights the risks and challenges facing the DIB, as well its efforts to address these.
The defense industrial sector has suffered a nearly 40 percent decline over the past decade. As a result, the Department of Defense has struggled to attract new entrants into the sector. To address this issue, the Defense Department has tried a variety of efforts to encourage new businesses to participate. Despite these attempts, many smaller firms are being left behind. This has increased national security risks.
Multiple DOD offices currently work to mitigate the risks associated with the DIB. The department doesn't have a comprehensive strategy to manage these risks. GAO reviewed several reports and interviewed DOD personnel to determine areas that could be improved. GAO identified five key elements that could aid the department in reaching its goals.
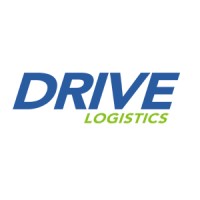
Loss of commercial suppliers is one of the greatest concerns. Many of these businesses provide parts for weapon systems used by the Pentagon. The industry's small business sector has been declining over the last decade. It is not easy to know how many new companies will enter the market.
Other problems include material shortages as well as reliance on foreign vendors. The acquisition process of the military is often slowed down by intellectual property restrictions. There is also no standard definition of "new entrant" in the defense industrial bases.
GAO recommended that Defense review its policy regarding mitigating risk in the DIB. Additionally, the GAO recommends that the Department of Defence continue to engage traditional defence contractors and create tools that make it easier to allow commercial technology providers to enter DoD's marketplace. These recommendations should be part of an overall strategy for addressing industrial base concerns.
As part of this strategy the Defense Department should think about how its OTAs or CSOs can be utilized to speed up acquisition strategy development. Supply chain restructuring can lead to dynamic outcomes if it is done with the right people processes and technologies.
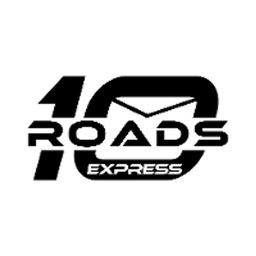
While the number of new entrants has decreased in the defense industry over the past decade it is still growing. For example, many companies are not comfortable with the traditional Federal Acquisition Regulation (FAR) process. A current landscape might make it more difficult for small businesses compete.
Innovation is key for the defense industrial sector. Small businesses and startups play a crucial role. Part of the resilient DIB, companies can support National Security needs while allowing Department of Defense to develop new and better military equipment.
Overall, the defense industrial base is a complex industry that requires a comprehensive strategy to ensure that resources are aligned with the needs of the military. The Department of Defense should continue to learn about the best practices for integrating technology in its business processes. This will enable it to create more innovative products and services.
FAQ
Why should you automate your warehouse?
Modern warehouses have become more dependent on automation. The rise of e-commerce has led to increased demand for faster delivery times and more efficient processes.
Warehouses should be able adapt quickly to new needs. They must invest heavily in technology to do this. Automation warehouses can bring many benefits. These are just a few reasons to invest in automation.
-
Increases throughput/productivity
-
Reduces errors
-
Improves accuracy
-
Safety enhancements
-
Eliminates bottlenecks
-
Allows companies to scale more easily
-
Workers are more productive
-
It gives visibility to everything that happens inside the warehouse
-
Enhances customer experience
-
Improves employee satisfaction
-
It reduces downtime, and increases uptime
-
High quality products delivered on-time
-
Removes human error
-
Helps ensure compliance with regulations
What are manufacturing & logistics?
Manufacturing refers the process of producing goods from raw materials through machines and processes. Logistics is the management of all aspects of supply chain activities, including procurement, production planning, distribution, warehousing, inventory control, transportation, and customer service. As a broad term, manufacturing and logistics often refer to both the creation and delivery of products.
What do you mean by warehouse?
A warehouse is a place where goods are stored until they are sold. It can be an outdoor or indoor area. It may also be an indoor space or an outdoor area.
Statistics
- You can multiply the result by 100 to get the total percent of monthly overhead. (investopedia.com)
- According to a Statista study, U.S. businesses spent $1.63 trillion on logistics in 2019, moving goods from origin to end user through various supply chain network segments. (netsuite.com)
- Many factories witnessed a 30% increase in output due to the shift to electric motors. (en.wikipedia.org)
- In the United States, for example, manufacturing makes up 15% of the economic output. (twi-global.com)
- Job #1 is delivering the ordered product according to specifications: color, size, brand, and quantity. (netsuite.com)
External Links
How To
How to Use 5S for Increasing Productivity in Manufacturing
5S stands as "Sort", Set In Order", Standardize", Separate" and "Store". Toyota Motor Corporation was the first to develop the 5S approach in 1954. It helps companies achieve higher levels of efficiency by improving their work environment.
This method aims to standardize production processes so that they are repeatable, measurable and predictable. This means that tasks such as cleaning, sorting, storing, packing, and labeling are performed daily. This knowledge allows workers to be more efficient in their work because they are aware of what to expect.
Five steps are required to implement 5S: Sort, Set In Order, Standardize. Separate. Each step requires a different action to increase efficiency. You can make it easy for people to find things later by sorting them. Once you have placed items in an ordered fashion, you will put them together. Then, after you separate your inventory into groups, you store those groups in containers that are easy to access. Labeling your containers will ensure that everything is correctly labeled.
Employees need to reflect on how they do their jobs. Employees need to be able understand their motivations and discover alternative ways to do them. They will need to develop new skills and techniques in order for the 5S system to be implemented.
The 5S method increases efficiency and morale among employees. Once they start to notice improvements, they are motivated to keep working towards their goal of increasing efficiency.