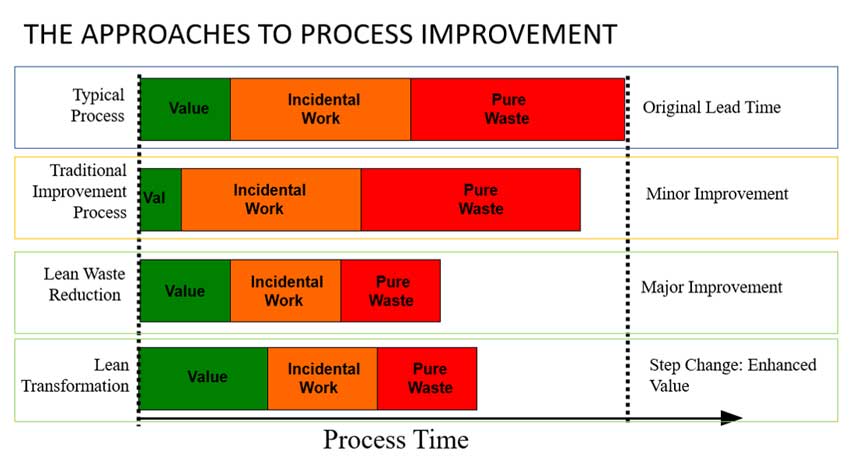
Manufacturing Extension Partnership (MEP) Centers provide a broad range of services to help small and medium-sized manufacturers grow and thrive. MEP Centers have been established in every state, including Puerto Rico. These centers are trusted business advisors that help solve manufacturers' challenges while identifying opportunities for expansion.
MEP centers employ subject matter experts with specific knowledge and experience in their local industry. They also have experience helping small and medium-sized manufacturing companies. They can help in various areas, including productivity, quality assurance, cybersecurity protection, growth of businesses, and advanced technology. Sharon Ohman of Purdue University’s MEP center, Fort Wayne, said that SMMs could also use the tools they create internally or in collaboration with their suppliers.
Centers receive federal funding, of which one-half is allocated to each. The remaining funds are provided by state or local governments and/or by private entities. The American Innovation and Competitiveness Act of 2017 adjusted the MEP cost share ratio, allowing the centers to retain more funding from nonfederal sources.
Most MEP centres are non-profit or affiliated with universities. Other MEP centers are operated by the state government or an agency within the same state as the center.
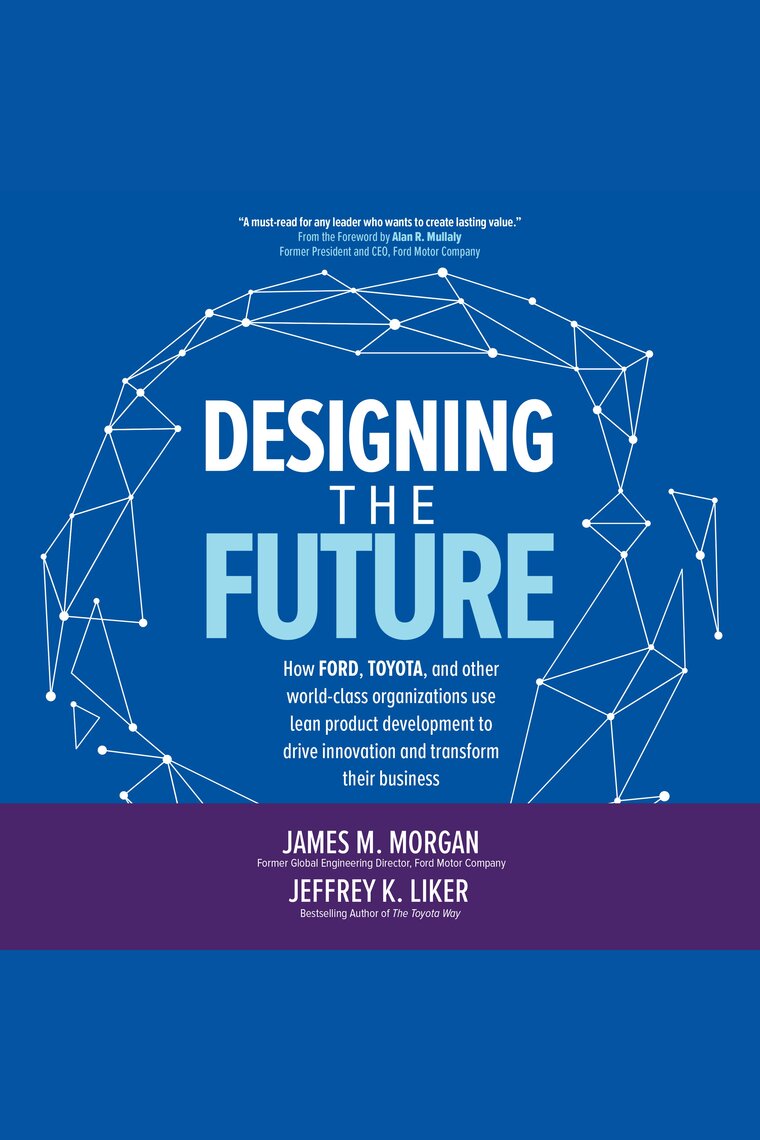
These centers may have managers, consultants, or professional technicians on staff. Some centers may be more technologically sophisticated and feature laboratories or a dedicated research center.
Some centers provide training and consulting to other companies. For example, the Nebraska MEP provides support to manufacturers on implementing new technology.
MEP Services can be offered to a manufacturer’s employees or the company. Some centers send specialists to manufacturing sites to work with the manufacturer's management team on specific goals.
MEP centres have been able to connect with more than 3000 manufacturers during the past 12 months. This helped them generate $14.4 Billion in sales, $1.5 Billion in cost savings, and $5.2 Billion in new client investment. They also helped create and maintain 125 746 jobs in the U.S.
The MEP National Network includes 51 MEP Centers (including the NIST MEP Office) and an MEP Board. These partners can play an important part in the success the MEP system. They will help ensure that it is effective and has the capability to expand to U.S. manufacturer in the near future.
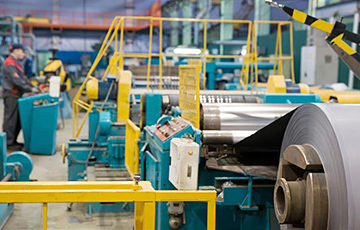
MEP Network's information infrastructure and pilots help MEP Centers and smaller manufacturers access the technical data they need to run their businesses. These projects aim to accelerate electronic commerce adoption by MEP centres and smaller manufacturers.
MEP National Network, in addition to being a critical component of the larger national strategy for increasing the ability of small and mid-sized manufacturers to adopt new technology to support business growth and economic development. The MEP National Network works with over 7,000 manufacturers each year and helps to boost innovation, economic growth and job creation in the United States.
FAQ
What is the responsibility of a production planner?
Production planners make sure that every aspect of the project is delivered on-time, within budget, and within schedule. They ensure that the product or service is of high quality and meets client requirements.
What is the role of a manager in manufacturing?
Manufacturing managers must ensure that manufacturing processes are efficient, effective, and cost-effective. They should be alert for any potential problems in the company and react accordingly.
They should also learn how to communicate effectively with other departments, including sales and marketing.
They should also be aware of the latest trends in their industry and be able to use this information to help improve productivity and efficiency.
How can manufacturing reduce production bottlenecks?
To avoid production bottlenecks, ensure that all processes run smoothly from the moment you receive your order to the time the product ships.
This includes both planning for capacity and quality control.
Continuous improvement techniques such Six Sigma can help you achieve this.
Six Sigma Management System is a method to increase quality and reduce waste throughout your organization.
It focuses on eliminating variation and creating consistency in your work.
What is the difference between Production Planning and Scheduling?
Production Planning (PP), also known as forecasting and identifying production capacities, is the process that determines what product needs to be produced at any particular time. Forecasting demand is one way to do this.
Scheduling refers the process by which tasks are assigned dates so that they can all be completed within the given timeframe.
What does it mean to warehouse?
A warehouse, or storage facility, is where goods are stored prior to being sold. It can be either an indoor or outdoor space. It could be one or both.
What jobs are available in logistics?
There are many types of jobs in logistics. Here are some examples:
-
Warehouse workers – They load and unload pallets and trucks.
-
Transportation drivers – They drive trucks or trailers to transport goods and perform pick-ups.
-
Freight handlers – They sort and package freight at warehouses.
-
Inventory managers – They manage the inventory in warehouses.
-
Sales representatives - They sell products to customers.
-
Logistics coordinators are responsible for organizing and planning logistics operations.
-
Purchasing agents: They are responsible for purchasing goods and services to support company operations.
-
Customer service representatives - They answer calls and emails from customers.
-
Shipping clerks: They process shipping requests and issue bills.
-
Order fillers are people who fill orders based only on what was ordered.
-
Quality control inspectors: They inspect outgoing and incoming products for any defects.
-
Others - There are many types of jobs in logistics such as transport supervisors and cargo specialists.
Statistics
- [54][55] These are the top 50 countries by the total value of manufacturing output in US dollars for its noted year according to World Bank.[56] (en.wikipedia.org)
- Job #1 is delivering the ordered product according to specifications: color, size, brand, and quantity. (netsuite.com)
- According to the United Nations Industrial Development Organization (UNIDO), China is the top manufacturer worldwide by 2019 output, producing 28.7% of the total global manufacturing output, followed by the United States, Japan, Germany, and India.[52][53] (en.wikipedia.org)
- It's estimated that 10.8% of the U.S. GDP in 2020 was contributed to manufacturing. (investopedia.com)
- Many factories witnessed a 30% increase in output due to the shift to electric motors. (en.wikipedia.org)
External Links
How To
Six Sigma in Manufacturing:
Six Sigma is "the application statistical process control (SPC), techniques for continuous improvement." Motorola's Quality Improvement Department developed it at their Tokyo plant in Japan in 1986. Six Sigma's basic concept is to improve quality and eliminate defects through standardization. In recent years, many companies have adopted this method because they believe there is no such thing as perfect products or services. Six Sigma seeks to reduce variation between the mean production value. This means that if you take a sample of your product, then measure its performance against the average, you can find out what percentage of the time the process deviates from the norm. If this deviation is too big, you know something needs fixing.
The first step toward implementing Six Sigma is understanding how variability works in your business. Once you've understood that, you'll want to identify sources of variation. These variations can also be classified as random or systematic. Random variations happen when people make errors; systematic variations are caused externally. If you make widgets and some of them end up on the assembly line, then those are considered random variations. If however, you notice that each time you assemble a widget it falls apart in exactly the same spot, that is a problem.
Once you identify the problem areas, it is time to create solutions. That solution might involve changing the way you do things or redesigning the process altogether. After implementing the new changes, you should test them again to see if they worked. If they didn't work, then you'll need to go back to the drawing board and come up with another plan.